Ходова частина автомобіля будова – частини автомобіля частини автомобіля англійською ходова частина автомобіля ходова частина автомобіля будова ходова частина автомобіля складається ходова частина автомобіля призначення ходова частина автомобіля вікіпедія часть автомобиля 5 букв часть авто
- 26.04.2020
Ходова частина автомобіля
МІНІСТЕРСТВО ОСВІТИ І НАУКИ Свердловської областіКачканарских професійне училище
ДИПЛОМНА РОБОТА
Тема: Ходова частина автомобіля
ДР 30.20 червня 5777 ПЗ
Пояснювальна записка
Група 81
Розробив
Керівник
Нормоконтроль
Заст. директора з УПР Вязовецкая С.В.
Дата защіти______________ Оценка________________
2006 Введення. 3
1. Основна частина. 4
1.1.Общая розділ .. 4
1.1.1. Призначення ходової частини. 4
1.1.2. Матеріали та їх властивості. 4
1.1.3. Аналіз технічних вимог. 5
1.1.4. Пристрій ходової частини. 5
1.1.5. Робота амортизатора. 8
1.2. Технологічний розділ. 9
1.2.1. Технічне обслуговування ходової частини. 9
1.2.2. Вибір обладнання та пристроїв для ремонту ходової частини. 13
2. Організаційна частина. 14
Безпека праці при виконанні шиномонтажних робіт. 14
3. Екологічна частина. 15
Автоматизоване управління міським транспортом. 15
Висновок. 17
Література .. 18 Значне зростання всіх галузей народного господарства вимагає переміщення великої кількості вантажів і пасажирів. Висока маневреність, прохідність і пристосованість для роботи в різних умовах робить автомобіль одним з основних засобів перевезення вантажів і пасажирів.
Автомобільний транспорт створений в результаті розвитку нової галузі народного господарства — автомобільної промисловості, яка на сучасному етапі є одним з основних ланок вітчизняного машинобудування.
У своїй дипломній роботі в основний її частини викладу про ходової частини автомобіля, її призначення, пристрій і роботу. Технологічний розділ присвячений технічному обслуговуванню ходової частини та вибору устаткування і пристроїв для її ремонту. В організаційній частині викладено матеріал про безпеку праці при виконанні шиномонтажних робіт. Екологічна частина присвячена впливу автотранспорту на навколишнє середовище.
1.1.1. Призначення ходової частини
Рама — це несуча система вантажного автомобіля. Вона сприймає всі навантаження, що виникають при русі автомобіля і служить основою, на якій монтують двигун, агрегати трансмісії, механізми органів управління, додаткове обладнання, а також кабіну і кузов.Балки мостів служать для сприйняття вертикальних, поперечних і поздовжніх зусиль, що діють на колеса.
Амортизатори гасять коливання ресор, викликані наїздом колеса на перешкоду.
Колеса автомобіля забезпечують безпосередній зв’язок з дорогою, беруть участь у створенні й зміні напряму його руху, передають навантаження від маси автомобіля на дорогу. Вони поглинають невеликі поштовхи і удари від нерівностей дороги під час руху.
1.1.2. Матеріали та їх властивості
Сталь. Зі сталі в ходовій частині виготовляють: болти маточин коліс, гайки тощо, зубчастих коліс головної передачі, поворотних цапф, передніх осей, шкворни поворотних цапф, передню балку, ресори, пружини, автомобільних рам.Сталь можна кувати, прокатувати, штампувати, зварювати і паяти. З неї можна волочити дріт, отримувати різні виливки. Сталь легко обробляється різальним інструментом. Сталь має високу міцність, в’язкістю і пластичністю і піддається термічній і хіміко-термічної обробки.
З латуні в ходовій частині виготовляють: втулки, затискних гвинтів і різної арматури. Латунь добре кується, прокатується в листи різної товщини і штампується.
З бронзи виготовляють втулки, а також використовується в амортизаторах.
Бронза володіє високою міцністю і стійкістю проти стирання і щодо дії атмосферного повітря і кислот. Бронза добре заповнює ливарні форми, дає малу усадку і добре піддається механічній обробці.
1.1.3. Аналіз технічних вимог
На рамі не повинно бути тріщин, погнутостей, тріщин по отворах під заклепки, порушення міцності клепаних з’єднань. На передній осі не повинно є: погнутости балки, зносу втулок під шворінь в цапфі, люфту в підшипників маточин коліс, зриву різьблення на цапфі, погнутости дисків коліс.На ресорі не повинні є тріщини або обломи на аркушах, втрати пружності, зносу втулок.
Амортизатор повинен працювати справно, не повинно бути тугого переміщення важеля, кількість рідини має строго відповідати технічним умовам.
1.1.4. Пристрій ходової частини
Рама. На вантажних автомобілях найбільшого поширення набули лонжеронний рами. Вони складаються з двох поздовжніх паралельних блок-лонжеронів, з’єднаних поперечинами, з використанням заклепок або зварювання. У зонах, що піддаються найбільшим навантаженням, лонжерони мають більш високий профіль, а іноді підсилюють вставками. Для кріплення агрегатів на рамі встановлені кронштейни, до яких закріплені паливний бак, крила, підніжки, ресори. Спереду до лонжеронів кріплять передній буфер, що оберігає автомобіль від пошкоджень, і буксирні гаки.Балки мостів. Балки провідних мостів пустотілі, всередині їх встановлені головна передача, диференціал і піввісь.
Балки задніх мостів автомобілів ГАЗ і ЗИЛ штамповано-зварні. У середній частині балка заднього моста має отвір з кільцевим пояском, до якого кріпиться корпус головної передачі. На цю балку з обох кінців напресовується фланці для кріплення опорних дисків гальмівних механізмів коліс.
Балка переднього ведучого моста автомобіля закінчується фланцями, до яких кріпляться кульові опори поворотних кулаків.
Колеса. Колеса вантажних автомобілів забезпечені дисками з плоским ободом. На ободі монтують однобортової знімне розрізне кільце, одночасно виконує функції замкового кільця.
На дисках коліс виконані конічні отвори, якими колесо встановлюють на шпильки. Гайки коліс теж мають конус. Збіг конусів гайок і отворів на дисках забезпечують точну установку коліс. У вантажних автомобілів на провідні задні півосі встановлюють по два колеса. Диски внутрішніх коліс закріплені на шпильках колпачковой гайками з внутрішньою і зовнішньою різьбою, а диски зовнішніх коліс — гайками з конусом. Щоб запобігти самоотвертиваніе гайок при прискоренні і гальмуванні автомобіля, гайки лівого боку мають ліву різьбу, а гайки правого боку — праву.
Пневматична шина складається з покришки, камери й ободной стрічки. Покришки складаються з каркаса, протектора (бігової доріжки), бічний і бортовий частин. Для хороших доріг застосовують шини з дрібним дорожнім малюнком протектора, а для поганих доріг і бездоріжжя-з великим.
ДР 30.20 червня 5777 ПЗ |
Балку вантажних автомобілів виготовляють з кованої сталі у вигляді двутавра з відігнутими нагору кінцями. Вигнута вниз середня частина дозволяє більш низько встановити двигун. На кінцях балки розташовані бобишки з вушками, в яких вставлені шкворни, що з’єднують балку з поворотними цапфами коліс. Щоб полегшити поворот коліс, між бобишками і вушком цапфи поміщений опорний кульковий підшипник. На осі цапфи в двох конічних роликових підшипниках встановлено втулка переднього керованого колеса. Регулювальною гайкою можна регулювати затяжку підшипників під час експлуатації.
Шворінь нерухомо закріплений в бобишках балки клиновим болтом. Поворотна цапфа встановлена на шворні в бронзових втулках, запресованих в отвори її вушок. Поворотні важелі вставлені в конічні отвори вушок цапфи і закріплені гайками.
Осьовий зазор між поворотною цапфою і балкою регулюють прокладками. До поворотної цапфи болтами прикріплений щит гальмівного барабана. Цей щит — опора колісного гальмового механізму.
Для кріплення ресор на балці виконані майданчика. Верхня частина поворотних цапф з’єднана через поворотний важіль з рульовим механізмом, а нижня частина через важіль рульової тяги — з рульовою тягою.
Передня підвіска. Ця підвіска здійснена на поздовжніх напівеліптичних ресорах. Додатково до ресорам, вона забезпечена гідравлічними амортизаторами.
Кріплення ресор до рами виконано на гумових подушках. У передні кронштейни ресор у спеціальні гнізда додатково встановлені наполегливі гумові подушки, що сприймають зусилля.
Прогини ресор обмежують гумові буфери. Подібним чином виконана передня підвіска і на інших автомобілях. На відміну від раніше згаданих, в ресорах листи від зсуву один від одного фіксуються під час роботи виступами і поглибленнями виштампуваними в листах ресор, а не стяжками болтами і хомутами.
Задня підвіска. У задній підвісці автомобіля крім основних ресор є додаткові ресори. Вони закріплені на балці заднього моста разом з основною ресорою драбинами, а їх кінці перебувають проти полиць опорних кронштейнів.
Амортизатори. На автомобілях застосовують рідинні телескопічні амортизатори подвійної дії. Вони складаються з циліндра, штока з поршнем, циліндричного резервуара і клапанів. У поршні виконані калібровані отвори і встановлені перепускний клапан і клапан віддачі. У нижній частині циліндра змонтовані впускний клапан і клапан зниження. Шток у верхній частині з’єднаний з кронштейном рами, а нижня частина резервуара з передньою віссю.
1.1.5. Робота амортизатора
У резервуар амортизатора заливають суміш, що складається з 50% трансформаторного і 50% турбінного масла, або амортизаторні рідина.Принцип дії амортизатора заснований на тому, що в результаті відносних переміщень Підресорне і не Підресорне мас автомобіля, опір рідини при перетіканні її під дією поршня через малі отвори гальмує переміщення рухомих частин амортизатора і разом з ними Підресорне мас. Амортизатори двосторонньої дії чинять опір при прогині і віддачі ресор.
При віддачі ресори амортизатор розтягується. У порожнині над поршнем створюється тиск, а клапан віддачі відкривається, і рідина через отвори малого прохідного перерізу в поршні і клапан віддачі протікає в порожнину під поршнем. Крім того, частина рідини через відкрився впускний клапан завдяки розрідженню надходить з резервуара в порожнину під поршнем.
1.2. Технологічний розділ
1.2.1. Технічне обслуговування ходової частини
Несправності елементів ходової частини (рами, підвіски осей і коліс) в основному виникають при експлуатації автомобілів з навантаженням, що перевищує максимальну вантажопідйомність, а також при експлуатації у важких умовах непрофіллірованних доріг.До основних несправностей передньої осі відносять прогин балки передньої осі, знос шкворней і шкворневих втулок, розробка посадочних місць обойм підшипників коліс, порушення кутів їх установки, в результаті чого погіршується керованість автомобілем і підвищується знос шин. Поломка ресор або просадка пружин підвіски, а також відмова в роботі амортизаторів викликають в кінцевому підсумку підвищений знос шин.
Несправність агрегатів і вузлів ходової частини виявляють частково оглядом при ЄВ. В обсяг робіт ТО-1 входять перевірка стану і кріплення передніх і задніх підвісок і амортизаторів, вимірювання люфта в підшипниках маточин коліс і шкворней поворотних цапф, а також оцінка стану рами і балки передньої осі. За графіком відповідно до карти змащування змащують шарнірні опори або підшипники шкворней поворотних цапф. Перевіряють стан шин і тиск повітря в них, яке при необхідності доводять до норми.
При ТО-2 на додаток до перерахованих робіт перевіряють і при необхідності регулюють правильність установки переднього і заднього мостів, кути установки передніх коліс, закріплюють хомути, драбини і пальці передніх і задніх ресор, подушки ресор і амортизатори, встановлюють мінімальні зазори в підшипниках коліс.
Огляд рами дозволяє встановити зміни її геометричної форми і розмірів, наявність тріщин, погнутість лонжеронів і поперечин, стан кріплень до рами кронштейнів ресор, подрессорніков і амортизаторів.
Перевірка геометричної форми рами може бути виконана виміром ширини рами спереду і ззаду по зовнішніх площинах лонжеронів. Різниця в ширині повинна бути для автомобілів ГАЗ не більше 4мм. Поздовжнє зсув лонжеронів рами від початкового положення можна визначити, заміряючи діагоналі між поперечиною рами на окремих її ділянках. Довжина діагоналей на кожній ділянці повинна бути однаковою. Допускається мінімальне відхилення не більше 5 мм.
Стан підвісок перевіряють при технічних обслуговуваннях зовнішнім оглядом, а кріплення їх — додатком зусилля. При огляді ресор виявляють поламані або тріснуті листи. Ресора не повинна мати видимого поздовжнього зміщення, що може статися через зрізу центрального болта. Перевіряючи правильність встановлення ресор, необхідно звертати особливу увагу на ступінь затягування гайок драбин і відсутність зносу втулок шарнірних кріплень ресор. Якщо ресори мають кріплення кінців у гумових подушках, звертають увагу на їх цілість, а також на правильне положення в опорі. Гайки кріплення драбин і хомутів ресор затягують рівномірно спочатку передні (по ходу автомобіля), а потім задні.
Технічне обслуговування амортизаторів полягає у перевірці їх кріплень, своєчасної заміни зношених гумових втулок. Особлива увага приділяється контролю герметичності. Якщо амортизатор має на поверхні патьоки рідини і втратив амортизуючі властивості, його ремонтують, піддають випробуванню після ремонту і встановлюють на автомобіль.
Несправності автомобільних коліс є наслідком неправильної експлуатації. До них відносять розробку отворів під шпильки або гайки кріплення, тріщини у дисках коліс, пошкодження і погнутість закраїн і ободів, бортових і замкових кілець, биття колеса в результаті невмілого монтажу шини на обід, дисбаланс колеса, корозію і порушення лакофарбового покриття обода колеса. Зазначені несправності виявляють при зовнішньому огляді, а биття перевіряють обертанням вивішеного колеса.
Шини, що мають незначні пошкодження покришок або проколи камер, ремонтують в умовах АТП. Для цієї мети використовують електровулканізатори і латки з сирої гуми. Покришки із зношеним протектором, але придатним каркасом, здають для відновлення проектора на шиноремонтному підприємство.
Для рівномірного зносу протектора шин рекомендується періодично через 6-8 тис. км переставляти колеса з задньою на передню вісь згідно схемі перестановки, включаючи сюди і запасне колесо. При перестановці коліс слід враховувати малюнок протектора (якщо він спрямованої дії), що позначається стрілкою на боковині покришки. При правильній установці колеса стрілка і переважний напрямок обертання при русі вперед повинні збігатися.
Монтаж шини ведуть тільки на справний обід. Перед монтажем завжди перевіряють стан обода. Він повинен мати правильну круглу форму, закраїни та посадочні полки також не повинні мати ушкоджень, забоїн і погнутостей, порушень лакофарбового покриття.
Демонтаж і монтаж шин легкових автомобілів виконують на стаціонарному стенді Ш-501М. Він складається з опорного диска (стола) з дротом від реверсивного електродвигуна, пневматичної натискного пристрою, стійки демонтажного важеля і апаратного шафи. Робочими органами стенду є опорний стіл, куди кріплять колесо, два важелі, які приводяться пневмоциліндром і хитні у вертикальній площині на загальній осі. Кінець кожного важеля забезпечений горизонтальним диском, службовцям для віджиму борту шини від обода. Важелі переміщуються у вертикальній площині зусиллям пневматичного циліндра, подача повітря в який здійснюється педаллю, що управляє одночасно вмиканням електродвигуна.
Після складання колеса легкових і вантажних автомобілів в обов’язковому порядку балансують.
Балансування коліс проводять для усунення їх неврівноваженості (дисбалансу), яка є наслідком нерівномірного розподілу маси колеса щодо осі або вертикальній площині симетрії. Дисбаланс при обертанні колеса викликає його биття і нерівномірний посилений знос шин. Для зменшення впливу дисбалансу колеса піддають статичної та динамічної балансуванню.
Статичну балансування можна виконати прямо на автомобілі на маточині переднього колеса. Для цього вивішують колесо, послаблюють затяжку і кріплять на неї проверяемое колесо. Приводять колесо в обертання за годинниковою стрілкою і дають йому самостійно зупинитися, відзначаючи крейдою на боковині покришки верхнє положення зупинки на вертикалі, що проходить через вісь обертання. Повторюють те ж саме при обертанні проти годинникової стрілки, відзначаючи крейдою після зупинки другу верхню позначку. Відстань між двома мітками ділять навпіл і відзначають нову середню позначку, яка буде вказувати на найбільш важке місце колеса, розташоване діаметрально навпаки отриманої мітки. Щоб врівноважити більш важку частина колеса, біля середньої мітки, по обидві сторони від неї на відстані приблизно половини радіусу обода навішують на закраину обода балансувальні тягарці рівної маси і знову дають поштовх на обертання колеса, стежачи за тим, де воно зупиниться. Якщо колесо зупиняється в положенні, при якому важки виявляються нижче осі обертання, значить, їх маси досить, щоб врівноважити колесо. В іншому випадку підбирають важки більшої маси.
Після підбору тягарців, послідовно розсовуючи їх від середньої мітки і перевіряючи обертанням, знаходять положення байдужої рівноваги, тобто можливості зупинятися після припинення обертання в будь-якому положенні.
1.2.2. Вибір обладнання та пристроїв для ремонту ходової частини
Для розбирання клепаних з’єднань рами застосовують пневматичні рубальні молотки.Якість виправлення деталей рами контролюють перевірочними лінійками і шаблонами. При складанні рам застосовують гідравлічну клепальні установку. Якість заклепкових робіт перевіряють контрольним молотком.
Розбирання і складання ресор здійснюють на спеціальних пристосуваннях або в лещатах. Прогин ресор встановлюється шаблонами. Зібрані ресори випробовують на спеціальному стенді.
На спеціальному стенді здійснюють перевірку амортизаторів на герметичність. Для зняття коліс використовують Пневмогайковерти. Шини вантажних автомобілів і автобусів розбирають і збирають на стаціонарному стенді Ш-509, Ш-153.
Для перевірки тиску в шинах використовують манометр.
Кути установки передніх коліс перевіряють і регулюють на оптичному або механічному стенді. Перевірку сходження передніх коліс на спеціальних постах, а також при індивідуальному обслуговуванні може бути виконана телескопічною лінійкою.
Для змащення тяг, шкворней в поворотній цапфі використовують шприц. Для розбирання та складання ходової частини використовують різноманітні ключі. Шиномонтажні роботи проводять у встановленому місці з застосуванням запобіжних огороджень. Не слід виправляти становище шини на диску постукуванням, ударяти по замкового кільця молотком або кувалдою при накачуванні. Слюсар повинен стежити за тим, щоб були справними і чистими диск колеса і замкове кільце. Не можна виробляти підкачування шини без демонтажу при зниженні тиску в ній більше ніж на 40%. Необхідно користуватися дозатором тиску або манометром, так як без них можлива перекачка шини, що може стати причиною нещасного випадку. Неприпустимо вибивати диск колеса вручну кувалдою. На даній операції необхідно використовувати стенд демонтажу і гайковерт для коліс. Під вивішеній частиною автомобіля повинен бути встановлений козелок, а під незняте колесами — упори. Забороняється переміщати колеса і шини вручну. Неприпустимо застосування викрутки, шила або ножа для видалення предметів, що застрягли в шині.
Автоматизоване управління міським транспортом
Зниженню шкідливих викидів автомобілів сприяє рівномірний рух машин на вулицях, ліквідація заторів, скорочення затримок транспорту на перехрестях.Велику роль у регулюванні руху відіграє звичний для всіх нас скромний світлофор. Дивна на перший погляд взаємозв’язок світлофора з чистотою повітря і економією палива та електроенергії пояснюється досить просто: у результаті вмілого управління транспортними потоками автомобілі менше простоюють на перехрестях, вхолосту витрачаючи пальне і забруднюючи повітря відпрацьованими газами, а трамваї не витрачають додаткову електроенергію на розгін і гальмування. Саме це завдання успішно вирішує «електронний регулювальник», обладнаний ЕОМ, спеціальними датчиками, встановленими на проїжджій частині, і отримує інформацію про рух транспорту з сусідніх перехресть.
Давно невід’ємною частиною міського пейзажу стали світлофори. У міру сил вони справно несуть службу, проте, їх можливості нас уже не влаштовують. Світлофори поки чисто механічно виконують свою роботу. Дотримуючись закладеної в них програмі, вони через певні проміжки часу перемикають сигнали і абсолютно «байдужі» до мінливою транспортної ситуації. Саме тому їм на допомогу повинні приходити люди. Нерідко працівник ДАІ вручну починає перемикати сигнали, щоб розвантажити найбільш напружений на даний момент напрямок.
Але навіть найдосвідченіший регулювальник здатний розвести потоки машин лише там, де він зараз перебуває, до того ж без урахування обстановки на інших перехрестях, не кажучи вже про магістралі або району, в цілому. От якщо б винайти такого регулювальника, який був би здатний стежити за розвитком транспортної ситуації на всіх основних напрямках у масштабі району, а то і всього міста та миттєво приймати необхідні, єдино правильне рішення.
В даний час такий регулювальник створений. Ім’я йому — система «СТАРТ», яка стала до ладу в Москві, найбільш насиченому автотранспортному місті країни.
«СТАРТ» — автоматизована система керування дорожнім рухом. Вона принципово відрізняється від більш простих подібних систем, які у Москві і в багатьох інших містах. Завдяки застосуванню досконалих технічних засобів, математичних методів та обчислювальної техніки, ця система дозволяє оптимально управляти рухом транспорту у всьому місті і повністю звільняє людину від обов’язків, безпосередньо, регулювальника автомобільними потоками.
Будь-які питання організації дорожнього руху необхідно розглядати не тільки з точки зору забезпечення його безпеки, а й зменшення токсичності відпрацьованих газів. Чому, скажімо, гранична швидкість руху в місті встановлено не вісімдесят, а шістдесят кілометрів на годину? Саме на цю швидкість у легкових автомобілів припадати мінімум шкідливих викидів. При різкому ж збільшення або зменшення швидкості руху, викид зростає більш ніж удвічі.
У поліпшенні організації та підвищення безпеки руху транспорту, роль техніки регулювання в даний час дуже велика. Автомобільна промисловість країни постійно вдосконалює конструкцію автомобілів, що випускаються з метою зниження витрати палива, зменшення забруднення навколишнього середовища, підвищення безпеки дорожнього руху.
У порівнянні з існуючими нові моделі й модифікації автомобілів ускладнюються, в їх системах з’являються сучасні прилади та пристрої. Проте ефективне використання автомобілів залежить не тільки від досконалості конструкції. Багато в чому воно визначається якістю технічного обслуговування при експлуатації. Крім того, задоволення зростаючих потреб в автомобільних перевезеннях не може бути забезпечено тільки за рахунок випуску нових автомобілів. Одним з головних резервів збільшення автомобільного парку є ремонт автомобілів. Таким чином, питання влаштування, технічного обслуговування і ремонту автомобілів тісно взаємопов’язані. 1. Боровських Ю.І., Буралев Ю.В. Пристрій і технічне обслуговування автомобілів М.: Вища школа, 1999.
2. Голубєв І.Р., Новіков Ю.В. Навколишнє середовище і транспорт М.: Вітапресс, 1999.
3. Калисский В.С., Мазон А.І. Автомобіль М.: Транспорт, 1998.
4. Кузнєцов М.А., Ітінская Н.І. Автотракторні експлуатаційні матеріали. М.: Вища школа, 1998.
5. Цибульниками А.В., Турге А.К. Охорона праці при експлуатації та ремонті автомобіля. М.: Вища школа, 2001
Шасі (автомобіль) — Вікіпедія
Матеріал з Вікіпедії — вільної енциклопедії.
У Вікіпедії є статті про інші значення цього терміна: Шасі.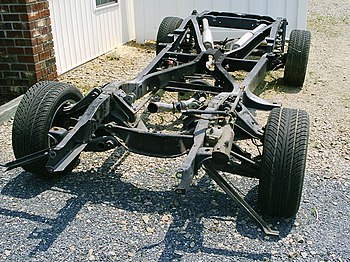
Шасі́ (від фр. châssis — основа, рама) — сукупність агрегатів і вузлів сухопутних транспортних засобів та інших самохідних машин, змонтованих на спільній рамі. Вузли та агрегати шасі забезпечують привід від двигуна на рушій (рушії) транспортного засобу та відповідають за його керованість на дорозі, вантажопідйомність та маневреність.
Основні складові шасі[ред. | ред. код]
До основних елементів шасі автомобіля відносяться:
Трансмісія[ред. | ред. код]
Трансмісія автомобіля призначена для передачі обертаючого моменту від двигуна до ведучих коліс автомобіля, зміни його напрямку і величини, а також перерозподілу між ведучими колесами (на повнопривідних автомобілях). Складові трансмісії:
Ходова частина[ред. | ред. код]
Ходова частина забезпечує рух автомобіля з визначеним рівнем комфорту. Механізми і деталі ходової частини зв’язують колеса з кузовом, гасять його коливання, сприймають і передають сили, що діють на автомобіль. Будова ходової частини:
Системи керування[ред. | ред. код]
До систем керування автомобілем відносять систему кермового управління і гальмівну систему. Кермове управління забезпечує зміну напрямку руху автомобіля, а гальмівна система дозволяє знижувати швидкість, аж до повної зупинки, і утримувати автомобіль на місці.
1.3.Загальна будова та призначення основних складових частин трактора автомобіля
Трактор – складна самохідна машина, призначена для переміщення та приводу в дію робочих органів мобільних машин і знарядь, перевезення вантажів на причепах, приводу стаціонарних машин від вала відбору потужності або приводного шківа. Трактор складається із взаємозв’язаних механізмів, які за призначенням поділяються на такі групи (або агрегати): двигун, силова передача, ходова частина, органи керування, робоче, допоміжне і електричне обладнання (рис. 1.1).
Двигун – це енергетичний пристрій, енергія якого використовується для привода трактора та виконання корисної роботи. На сучасних тракторах енергетичним пристроєм є поршневий двигун внутрішнього згоряння (ДВЗ). ДВЗ перетворює теплову енергію палива, що згоряє в його циліндрах, у механічну роботу – обертальний рух колінчастого вала.
Силова передача (трансмісія) призначена для передачі обертального руху та крутного моменту від двигуна до ходової частини та зміни їх за величиною та напрямом.
Складається силова передача з муфти зчеплення, проміжного з’єднання, або карданної передачі, коробки передач, головної передачі, диференціала (колісні трактори) або планетарного механізму чи муфт керування (гусеничні трактори), а також кінцевої передачі.
Ходова частина підтримує остов, перетворює обертальний рух коліс або зірочок у поступальний рух трактора та пом’якшує удари від нерівностей поля чи дороги.
У колісних тракторів ходова частина складається з рами, задніх ведучих й передніх напрямних коліс та елементів, що з’єднують колеса з остовом. У гусеничних тракторів ходова частина складається з рами, опорних котків і підтримуючих роликів, ведучих зірочок, натяжних коліс і гусениць.
Органи керування призначені для керування трактором, встановленими на ньому агрегатами та робочим обладнанням.
До органів керування належать: рульове колесо або важелі муфт поворотів чи планетарного механізму, педалі й важелі гальм, важелі переключення передач й діапазонів, педалі муфт зчеплення, важелі розподільників гідравлічних систем та інші.
Робоче обладнання трактора призначене для використання потужності його двигуна, а також приведення в дію механізмів навісних, напівнавісних, причіпних і стаціонарних машин, для приєднання машин, причепів і напівпричепів, для накачування шин.
До робочого обладнання належать: гідравлічна система з механізмом навішування, виносними циліндрами і донавантажувачем ведучих коліс, причіпний пристрій, гідрофікований гак, вали відбору потужності (ВВП), шків та компресор.
Допоміжне обладнання забезпечує трактористу комфортні умови роботи. До нього відноситься кабіна з пристроями опалення і вентиляції, м’яким сидінням, приладами освітлення і сигналізації, змивачами скла, склоочисника, контрольними приладами, кондиціонер тощо.
Електричне обладнання призначене для пуску двигуна, освітлення і сигналізації.
1.4. Основні напрямки розвитку і удосконалення конструкції тракторів і автомобілів.
2. Загальна будова і робота двигунів внутрішнього згоряння (двз)
Тема 2. Загальна будова трактора, самохідних шасі, автомобіля.
⇐ ПредыдущаяСтр 2 из 19Следующая ⇒
Питання, що виносяться на самостійне вивчення:
1. Основні частини трактора та автомобіля.
2. Класифікація тракторів і автомобілів.
3. Коротка технічна характеристика основних моделей тракторів і автомобілів.
4. Порівняльна характеристика техніко-економічних показників сучасних вітчизняних тракторів і автомобілів порівняно із зарубіжними.
/1/, с. 11…22.
Методичні вказівки:
1. Основні частини трактора та автомобіля.
Трактор — складна самохідна машина, призначена для переміщення й приводу робочих органів мобільних машин та знарядь, перевезення вантажів на причепах, приводу стаціонарних машин за допомогою вала відбирання потужності (ВВП) або привідного шківа.
Трактор складається з двигуна, трансмісії, ходової частини, механізмів керування, робочого, електричного та допоміжного обладнання (рис. 1.).
Двигун
Рис. 1. Основні частини трактора:
1 — ходова частина; 2— двигун; 3 — допоміжне обладнання; 4— робоче обладнання; 5-трансмісія; 6— механізми керування.
Трансмісія передає крутний момент від колінчастого вала двигуна до рушіїв та до приймальних валів машин, що агрегатуються з трактором, забезпечує можливість зміни його напрямку і величини.
Ходова частина є опорою і перетворює обертальний рух коліс чи зірочок на поступальний рух машини.
Робоче обладнання забезпечує використання потужності двигуна для приводу робочих органів машин чи знарядь, керування ними та виконання інших функцій. Складається з роздільно-агрегатної гідравлічної начіпної системи, гідродовантажувачів ведучих коліс, ВВП, тягових та опорно-зчіпних пристроїв, приводного шківа.
Електричне обладнання застосовують для пуску двигуна, запалювання робочої суміші (в бензинових двигунах), сигналізації,
Рис. 2. Основні частини вантажного автомобіля:
1 — двигун; 2 — кузов; 3 — гальмівна система; 4 — шасі; 5 — ходова частина; 6 — кермове керування; 7 — трансмісія.
освітлення, живлення приладів та допоміжного обладнання.
Допоміжне обладнання — кабіна з підресорним сидінням, опалюванням та вентиляцією; вантажі для збільшення зчіпної ваги трактора.
Трактор, сполучений з машинами або знаряддями, становить машинно-тракторний агрегат.
Автомобіль — колісний безрейковий транспортний засіб, що приводиться в дію власним джерелом енергії. Складається з двигуна, шасі і кузова (рис. 2).
На більшості автомобілів застосовують поршневі двигуни внутрішнього згоряння, паливом для яких є бензин, дизельне або газове паливо.
Шасі об’єднує трансмісію, ходову частину та механізми керування.
Кузов служить для розміщення вантажу, що перевозиться. В кузові легкового автомобіля чи автобуса розміщуються і пасажири, і водій. Кузов вантажного автомобіля складається з платформи під вантаж і кабіни водія.
Автомобіль та причіп або напівпричіп, що ним буксирується, є автомобільним поїздом.
У багатьох сучасних вантажних автомобілях для збільшення розмірів вантажної платформи кабіну розміщують над двигуном. Для збільшення пасажирського приміщення кузова у деяких легкових автомобілях двигун розміщують попереду поперек поздовжньої осі машини, а привід здійснюється до передніх коліс. Отже, компонування сучасних автомобілів може бути досить різним.
2. Класифікація тракторів і автомобілів
Сільськогосподарськими називають трактори, які призначені для виконання робіт у рослинництві та в тваринництві.
Типаж тракторів — це технологічно й економічно обґрунтована сукупність моделей, які застосовують у сільськогосподарському виробництві. Головною класифікаційною ознакою є номінальне тягове зусилля, що визначає основний експлуатаційний показник трактора.
Типаж тракторів включає певну кількість базових моделей, що різняться за величиною мінімального тягового зусилля і призначенням, а також необхідну кількість модифікацій, уніфікованих з базовими моделями, але з конструктивними відмінностями для забезпечення ефективної роботи цих машин у спеціальних умовах. Уніфікація механізмів і деталей полегшує виготовлення, освоєння та використання тракторів, дає змогу скоротити перелік запасних частин.
Трактори загального призначення використовують для робіт у рослинництві й кормо виробництві за винятком обробітку просапних культур. Вони мають значну потужність двигуна та надійне зчеплення з ґрунтом, що дає змогу розвивати досить велику силу тяги.
Сільськогосподарські трактори загального призначення, пристосовані також для обробітку просапних культур, називають універсальними.
Просапні трактори призначені для обробітку посівів та збирання врожаю просапних культур.
Просапні трактори, що можуть виконувати такі роботи, як і трактори загального призначення, називають універсально-просапними. Вони різняться значним агротехнічним просвітом і можливістю зміни ширини колії.
Тракторне самохідне шасі — універсально-просапний трактор з незайнятою в між мостовому просторі рамою для розміщення начіпних машин чи знарядь, призначених для обробітку рослин і збирання врожаю просапних культур, які посіяні переважно вузькорядним способом.
Для виконання певного виду робіт чи робіт в особливих виробничих умовах призначені спеціалізовані трактори. Серед них — бавовницький, виноградниковий, рисівницький, буряківничий, тепличний, портальний (для виконання робіт з вирощування кущових культур), для чайних плантацій, низькоклі-ренсний, гірський, малогабаритний (для виконання робіт у рослинництві на дрібноконтурних ділянках, терасах і в комунальному господарстві).
Залежно від конструкції рушія трактори поділяють на гусеничні і колісні. Значна площа опорної поверхні гусеничних тракторів забезпечує добре зчеплення їх з ґрунтом, що зумовлює високі тягово-зчіпні показники. Колісні трактори універсальніші, однак поступаються перед гусеничними у зчепленні з ґрунтом і більше його ущільнюють.
Сільськогосподарські трактори, що мають гусеничні та колісні рушії і переміщуються за допомогою тільки гусеничного або тільки колісного, називають колісно-гусеничними.
За типом остова розрізняють трактори рамні, остов яких утворений звареною чи клепаною рамою, та напіврамні, остовом яких є дві поздовжні балки, прикріплені до корпусу трансмісії.
Трактори класу тяги 0,6 (номінальне тягове зусилля б кН) призначені для виконання малоенергомістких робіт в овочівництві, садівництві, кормовиробництві, на транспорті тощо. Базова модель — трактор Т-25А, яку виготовляє Володимирський тракторний завод, розпочато виготовлення сучасної моделі Т-ЗОА. Вітчизняний — ХТЗ-2511.
Трактори класу тяги 0,9 (9 кН) використовують для міжрядного обробітку просапних культур, транспортування вантажів, робіт загального призначення, приводу робочих органів стаціонарних машин. Базовою моделлю є універсально-просапний трактор Т-40М Липецького тракторного заводу. Вітчизняний — ХТЗ-5020.
Трактори класу тяги 1,4 (14 кН) — найбільш масові універсально-просапні трактори. Це МТЗ-80, МТЗ-102, МТЗ-82, МТЗ-100, які виготовляє Мінський тракторний завод, та ЮМЗ-6АЛ, ЮМЗ-6АМ — Південного машинобудівного заводу (м. Дніпропетровськ). Тягово-зчіпні якості, питома енергонасиченість, надійність, оснащеність робочим та допоміжним обладнанням цих тракторів такі, що кількість машин і знарядь, з якими вони можуть агрегатуватися, перевищує 200 назв.
Трактори класу тяги 2 (20 кН) використовують для механізації робіт на бурякових плантаціях, виноградниках, у садах. Це трактори Т-70С, Т-90С Кишинівського тракторного заводу.
Трактори класу тяги З (30 кН) — загального призначення. Базовими моделями є гусеничний Т-150 та колісний Т-150К трактори виробництва Харківського, ДТ-175С — Волгоградського і ДТ-75М — Павлодарського тракторних заводів.
До тракторів класу тяги 4 (40 кН) належить гусеничний трактор Т-4А виробництва Алтайського тракторного заводу (м. Рубцовськ), який використовують на роботах загального призначення.
Трактори класу тяги 5 (50 кН) — Санкт-Петербурзького Кі-ровського заводу (К-701) призначені для виконання робіт на значних площах і транспортування вантажів.
Трактори класу тяги 6 (60 кН) — гусеничні Т-130 Челябінського тракторного заводу. їх використовують для енергомістких робіт.
§ 2.9. Система живлення двигунів газобалонних автомобілів
Газове паливо для автомобільних двигунів застосовують у стисненому або зрідженому стані. Метан стискають до тиску в середньому 20 МПа і зберігають у товстостінних балонах. Етан, пропан і бутан переходять у рідкий стан при стисканні до 1,6 МПа. їх також зберігають у балонах.
Газоповітряні суміші порівняно з бензоповітряними мають вищі антидетонаційні властивості, що дає змогу підвищити ступінь стискання й поліпшити економічні показники двигуна. Газові двигуни характеризуються повнішим згорянням суміші й набагато нижчою токсичністю (шкідливістю) відпрацьованих газів, завдяки чому зменшується забруднення навколишнього середовища.
У разі застосування газу не змивається плівка оливи зі стінок гільз і поршнів, зменшується нагароутворення в камерах згоряння; через відсутність конденсації пари бензину на стінках гільз циліндрів не розріджується олива, завдяки чому в 1,5…2 рази збільшуються термін служби двигуна й період зміни оливи.
Однак у газобалонних автомобілів складна система живлення, підвищуються вимоги щодо пожежо й вибухобезпечності, потужність газових двигунів на 10…20 % менша порівняно з карбюраторними, оскільки в суміші з повітрям газ займає більший об’єм, ніж бензин. Автомобіль втрачає частину своєї вантажопідйомності через велику масу газобалонної установки.
Двигуни, що працюють на стиснених або зріджених газах, створюють на базі карбюраторних. Для цього останні обладнують спеціальною газовою апаратурою й балонами, але вони зберігають здатність працювати також і на бензині. При цьому висока детонаційна стійкість газу, октанове число якого перевищує 100 од., належно не реалізується, бо ступінь стискання двигуна вибирають відповідно до набагато меншого, ніж у газу, октанового числа бензину.
Установка для роботи на стисненому газі. Вісім балонів, згрупованих по чотири (рис. 2.55), розміщують під платформою кузова й кожну групу обладнують вентилем, що дає змогу витрачати газ із будь-якої групи або відразу з обох. Газом балони наповнюються крізь вентиль 10,
Із балонів газ крізь витратні вентилі 9і /’/надходить у підігрівник 18, що призначається для захисту системи від замерзання внаслідок великого зниження температури газу під час його розширення в редукторі високого тиску 20. Між підігрівником газу, що обігрівається теплотою відпрацьованих газів, і балонами встановлено основний витратний вентиль 13. На редукторі високого тиску ^установлено датчик контрольної лампи, яка засвічується в разі зниження тиску газу в редукторі до значення менше ніж 0,45 МПа. Це сигналізує водієві про те, що газу в балонах залишилося на 10…12 км.
Із редуктора 20 газ надходить в електромагнітний клапан 6 із фільтром. Цей клапан відкривається під час пуску двигуна, і газ трубкою 7 надходить у редуктор низького тиску 3.
Редуктор 3 має два ступені й знижує тиск газу, що надходить у карбюратор-змішувач, майже до атмосферного (0,9…1,15 МПа), дозує газ для приготування суміші потрібного складу й вимикає газову лінію в разі зупинки двигуна. Під час роботи двигуна газ надходить у карбюратор-змішувач 21, а в режимі холостого ходу — шлангом 2 безпосередньо в за дросельний простір.
Робота двигуна на бензині забезпечується стандартною системою живлення бензином, яку підключено до карбюратора-змішувача 21.
Сталеві балони для стисненого газу виготовляють із суцільнотягнутих труб із зовнішнім діаметром 219 мм і товщиною стінок 6,5…7,0 мм. Місткість балона — 50 л.
Для вдосконалення газобалонної паливної системи й підвищення протипожежної безпеки на автомобілях ЗИЛ-138А горловини балонів можна розміщувати з правого боку автомобіля. Особливість системи полягає в тому, що редуктор високого тиску встановлюється на передній стінці кабіни під капотом. Кронштейн редуктора водночас править за підігрівник газу. Для цього до додаткового кронштейна приварюється трубка, куди шлангом із системи охолодження двигуна через кран приладу для опалювання кабіни надходить гаряча рідина. З порожнини кронштейна рідина шлангом спрямовується в радіатор приладу для опалювання кабіни, а потім до насоса системи охолодження двигуна. Для пожежної безпеки в разі випадкового розриву мембрани редуктора високого тиску газ із ковпака редуктора й від запобіжного клапана відводиться за межі підкапотного простору окремими трубопроводами.
Основні елементи газобалонної установки для роботи на стисненому газі: • газові трубопроводи; ф вентилі; + редуктор високого тиску; * підігрівник газу; 4 електромагнітний клапан; 4 газовий редуктор низького тиску; 4- дозувально-економайзерний пристрій; • карбюратор-змішувач.
Газові трубопроводи від балонів до редуктора високого тиску автомобіля ЗИЛ-138А становлять сталеві трубки із зовнішнім діаметром (10+ 0,1) мм і товщиною стінки 2 мм. Трубопровід від редуктора високого тиску до редуктора низького тиску — це трубки діаметром (10± 0,15) мм і товщиною стінки 1 мм. Усі з’єднання газових трубопроводів з пере хідникам й, вентилями та іншими елементами газової апаратури — безпрокладні ніпельні типу «врізане кільце» й допускають багаторазове розбирання. Коли затягується накидна гайка, кільце ніпеля деформується й набирає форми внутрішнього конічного отвору в штуцері, герметизуючи з’єднання. Водночас кільце врізується гострою кромкою в стінку трубки, запобігаючи вириванню її зі з’єднання під дією високого тиску.
Вентилі, встановлені в газобалонній системі автомобіля ЗИЛ-138А, мають різне призначення: один — наповню вальний, решта три — витратні. Конструкція вентилів в основному однакова: вони різняться лише різьбою на бічному штуцері (наповню вальний вентиль має спеціальну ліву різьбу). Вентиль складається з корпусу з конічною різьбою, маховика зі шпинделем, муфти та клапана. Для приєднання газопроводу на бічний штуцер вентиля нагвинчується перехідний штуцер із прокладкою. В наповню вального вентиля після заповнення балонів стисненим газом перехідний штуцер закривається запобіжним ковпачком із ланцюжком.
Редуктор високого тиску (рис. 2.56) призначається для зменшення тиску стисненого газу з 20 до 0,9…1,15 МПа. Тиск газу в редукторі знижується внаслідок його розширення під час охолодження крізь щілину між клапаном 5 і сідлом 7 у камеру низького тиску Б. У порожнину високого тиску А стиснений газ надходить крізь штуцер. Клапан 5 залишається відкритим під дією зусилля натискної пружини /, що передається на нього через мембрану 2 й штовхач 3, доти,
доки тиск газу під мембраною не врівноважить це зусилля, після чого клапан закривається під дією пружини 6. Редуктор автоматично підтримує робочий тиск. Якщо тиск нижчий від 0,45 МПа, клапан редуктора відкритий постійно, а в кабіні водія засвічується контрольна лампа. Якщо ж робочий тиск з якихось причин перевищить 1,7 МПа, спрацює запобіжний клапан.
Підігрівник потрібний для попереднього підігрівання газу, особливо взимку. Без підігрівника волога й вуглекислота, які містяться в газі, можуть замерзнути в редукторі високого тиску.
Підігрівник газу автомобіля ЗИЛ-138А складається з нижнього та верхнього корпусів, у яких стиснений природний газ обігрівається теплотою відпрацьованих газів. Вхідний патрубок підігрівника гнучким металевим рукавом сполучається з лівою приймальною трубою глушника. З підігрівника відпрацьовані гази викидаються в атмосферу вихідним патрубком.
У схемі газобалонної установки підігрівник розташовано між магістральним вентилем та редуктором високого тиску й установлено позаду останнього на лівому лонжероні рами.
Електромагнітний клапан із фільтром (рис. 2.57), куди під тиском 0,9…1,15 МПа газ надходить з редуктора високого тиску, прикріплено на кронштейні до передньої стінки кабіни. Фільтр складається з корпусу 6, електромагнітного клапана 7, повстяного фільтрувального елемента 2, алюмінієвого ковпака 3, підвідного й відвідного штуцерів. Коли запалювання ввімкнено, клапан електромагніту під дією пружини закритий і не пропускає газ у редуктор низького тиску. Після вмикання запалювання клапан відкривається, й очищений від механічних домішок газ надходить у редуктор низького тиску, а потім у змішувач і карбюратор. Ковпак фільтра під час його монтажу на корпус ущільнюється гумовим кільцем.
Газовий редуктор низького тиску (рис. 2.58) становить двоступінчастий автоматичний регулятор тиску мембранного типу з важільною передачею від діафрагми до клапанів. Основне призначення редуктора полягає у зниженні тиску газу, який надходить до змішувача Водночас в редукторі здійснюється автоматичне регулювання кількості газу, потрібного для різних режимів роботи двигуна, за допомогою дозувально-економайзерного пристрою (див. рис. 2.59).
Для створення надлишкового тиску газу на виході з редуктора й надійнішого перекриття газової лінії, коли двигун не працює, передбачено розвантажувальний пристрій мембранно-пружинного типу, який сполучається із впускним трубопроводом двигуна.
Кожний ступінь редуктора обладнано регулювальним клапаном, плоскою мембраною з прогумованої тканини, пружиною та важелем, що з’єднує мембрану з клапаном. Обидва ступені редуктора разом Із розвантажувальним і дозувально-економайзерним пристроєм об’єднано в одному агрегаті. Коли двигун не працює й витратний вентиль на хрестовині закритий, тиск у порожнині 31 першого ступеня дорівнює атмосферному, і клапан ^/першого ступеня відкритий під дією пружини 19 (рис. 2.58).
Коли вентиль відкрито й увімкнено електромагнітний клапан, газ, пройшовши крізь фільтри вентиля, електромагнітного клапана й редуктора низького тиску, надходить у порожнину 31 першого ступеня редуктора. Газ тисне на мембрану 25, яка, долаючи зусилля пружини 19, прогинається й у момент досягання заданого тиску через важіль 18 закриває клапан 27. Тиск газу в порожнині регулюється зміною зусилля пружини 19, що діє на мембрану 25, за допомогою гайки 20.
Клапан 16 другого ступеня закритий і щільно притиснутий до сідла пружиною розвантажувальної мембрани й пружиною 39, зусилля від яких передається через шток 36 і стержень 38, важіль 4 і штовхач 5. Особливість конструкції другого ступеня полягає в застосуванні розвантажувального пристрою. Коли двигун не працює, пружина диска розвантажувального пристрою створює додаткове зусилля, що через важільну систему передається на клапан 16 і запирає його, надійно перекриваючи вихід газу до змішувача.
Під час пуску двигуна у змішувальній камері карбюратора створюється розрідження, яке шлангами (через вакуумну порожнину економайзера) передається в порожнину 32 розвантажувального пристрою. Розвантажувальна мембрана 34 внаслідок розрідження прогинає й стискає пружину диска, тим самим розвантажуючи клапан 16 другого ступеня. Зусилля пружини 39 стає недостатнім для втримання клапана 16 другого ступеня закритим, і він відкривається під тиском газу з порожнини 31 першого ступеня. Газ заповнює порожнину ^другого ступеня, а потім крізь економайзер надходить у змішувач. Тиск газу в порожнині 31 першого ступеня встановлюється в межах 0,18…0,20 МПа.
У режимі холостого ходу витрата газу невелика, і в порожнині 33 другого ступеня створюється надлишковий тиск. Зі збільшенням витрати газу тиск у порожнині 33 знижується майже до атмосферного. В міру відкривання дросельних заслінок подача газу в циліндри двигуна збільшується. Кількість газу, що визначає склад газоповітряної суміші, регулюється економайзером: в режимі часткових навантажень двигун працює на збіднених сумішах, що дає змогу досягти найкращої економічності, а для того щоб двигун розвинув максимальну потужність при повному відкритті дросельних заслінок, паливна суміш збагачується.
Склад газоповітряної суміші, що надходить до двигуна, регулюється дозувально-економайзерним пристроєм (рис. 2.59), який складається з дозувального пристрою, економайзера з пневматичним приводом та патрубка для відведення газу з редуктора.
Коли двигун працює на часткових навантаженнях (з не повністю відкритими дросельними заслінками), газ із редуктора подається крізь дозувальний отвір шайби 10. Потужнісне регулювання двигуна (в разі повного відкриття дросельних заслінок) забезпечується при відкритому клапані 8.
Простір між діафрагмою б та кришкою 5 економайзера за допомогою штуцерів і гумових трубок 1, 2 сполучається з впускним трубопроводом двигуна й розвантажувальним пристроєм газового редуктора.
У корпусі 4 дозувальне-економайзерного пристрою розміщено діафрагму 6 і пружину 7, затиснуті кришкою 5, клапан 8 з пружи-
ною 9, пластину 12 з дозувальними шайбами потужнісного 11 та економічного врегулювань. У корпусі 4економайзера є патрубок 3 для
виходу газу.
В карбюраторі-змішувачі К-91 газовий змішувач конструктивно об’єднано з пере хідником карбюратора К-88А (рис. 2.60), на якому встановлено повітряний фільтр. У пере хідник змішувач 5 газ надходить крізь патрубок 3 і зворотний клапан 4, який під час роботи двигуна в режимі холостого ходу закритий. В цьому разі газ трубкою 2 надходить у канали холостого ходу змішувальних камер карбюратора з патрубка змішувача.
Система
живлення бензином автомобіля ЗИЛ-138А
відрізняється від системи живлення
автомобіля ЗИЛ-130 тим, що між бензонасосом
і поплавцевою камерою карбюратора
встановлено електромагнітний
клапан-фільтр. Коли вимикається
запалювання, клапан автоматично
закривається. Клапан може бути закритий
і в разі ввімкненого запалювання, якщо
перемикач виду палива встановлено в
положення «О» (коли весь бензин із
бензобака витрачено) або в положення
«газ», У корпус клапана вмонтовано
стандартний фільтр тонкої очистки
бензину з керамічним фільтрувальним
елементом і знімним пластмасовим
стаканом-відстійником.
Газобалонна установка для роботи на зрідженому газі. З балона 5 крізь витратний вентиль 19 (рис. 2.61), магістральний вентиль 6 і газопровід 17 стиснений газ надходить у випарник /6, що обігрівається рідиною з системи охолодження двигуна. Потім крізь фільтр 11 газ надходить у редуктор 12, де його тиск зменшується майже до атмосферного. Контролюють роботу системи за допомогою манометрів 7 (тиск у балоні) і‘8 (тиск у редукторі).
Пуск і прогрівання двигуна здійснюють на паровій фазі газу. Для цього відкривають паровий 18 і магістральний 6 вентилі. На короткий час двигун зупиняють вимиканням запалювання, а в разі зупинки на 1…2 год перекривають магістральний вентиль.
На днищі балона 5 є запобіжний клапан 2 (відкривається при тиску 1,68 МПа), наповню вальний вентиль із зворотним клапаном, вентиль максимального заповнення балона й датчик рівня зрідженого газу.
Для наповнення балона використовують вентиль 4. Заповнюють тільки 90 % об’єму, щоб у разі розширення газу під час нагрівання
балон не зруйнувався. Рівень рідкого газу в процесі заправляння контролюється за допомогою трубки рівня вентиля* покажчика 1. Водій контролює наявність газу за допомогою покажчика 3.
• Заправляти газобалонні установки можна тільки на газонаповнювальних станціях, коли двигун не працює. Під час заправляння балонів зрідженим газом треба берегтися обмороження.
Експлуатація газобалонних автомобілів з несправним газовим обладнанням і витіканням газу забороняється. Коли не вдається усунути витікання газу, його випускають в атмосферу (якомога далі від людей і джерел вогню).
• До водіння й обслуговування газобалонних автомобілів допускаються особи, які мають відповідну підготовку і склали іспити з техмінімуму та техніки безпеки.