Кузов из чего состоит: что это такое и из чего состоит, назначение и конструкция, а также толщина металла деталей, частей и элементов, алюминиевый – Устройство кузова легкового автомобиля
- 07.03.2021
Из чего изготавливают кузов автомобиля? Какие материалы используются при производстве?

Добрый день, сегодня мы расскажем о том, из чего изготавливают автомобильный кузов, какие материалы применяют при производстве, а также при помощи, каких технологий осуществляется этот важный процесс. Кроме того, узнаем, какие существуют основные разновидности металлов, пластика и прочих материалов, которые зачастую используются при производстве элементов кузова транспортного средства, а также рассмотрим, какими преимуществами с недостатками обладает то или иное сырье в отдельности каждого вида. В заключении мы поговорим о том, какой материал на сегодняшний день является самым востребованным у автопроизводителей, а также от чего зависит качество и долговечность готового кузова машины.

КАК СОБИРАЮТ АВТОМОБИЛИ LEXUS И TOYOTA?
Кузов любого автомобиля играет роль несущей конструкцией, в котором использовано при производстве огромное многообразие различных материалов и комплектующих. Чтобы кузов машины отслужил свой срок службы надежно, а также качественно, необходимо понимать, как за ним правильно следить и эксплуатировать. Чтобы это понимать, нужно знать из чего изготовлена несущая конструкция транспортного средства, а также какая технология сварки и производства применялась. Благодаря этой информации, мы сможем без труда определить преимущества и недостатки того или иного типа кузова.
Справочно заметим, что для изготовления кузова нужны сотни отдельно взятых запасных частей, компонентов и деталей, которые затем необходимо очень точно, а также грамотно соединить в единую конструкцию, которая будет объединять в себе все элементы транспортного средства. Чтобы изготовить прочный, при этом безопасный, легкий и по приемлемой стоимости кузов современного автомобиля, нужно постоянно искать различные компромиссы, а также новые технологии с материалами.

1. Изготовление кузова автомобиля из стали: преимущества и недостатки
Большинство кузовов автомобиля, а точнее его детали изготавливается из разных сортов стали, алюминиевых сплавов и даже пластмассы с добавлением стекловолокна. Но основным материалом на сегодняшний день все же выступает низкоуглеродистая листовая сталь с примерной толщиной в 0,7-2 миллиметра. Благодаря использованию тонкого листа стали, автопроизводителям удалось уменьшить общую массу транспортного средства и при этом увеличить жесткость кузова.

Высокая прочность кузова получается благодаря специальным свойствам и составу стали, а также его способностью к глубокой вытяжке, то есть можно изготавливать детали сложных форм. Кроме того, нельзя забывать, что новые технологии в сварке помогают получать высокотехнологичные соединения. Однако сталь обладает высокой плотностью и слабой коррозионной стойкостью, поэтому такой материал требует специальных дополнительных мероприятий для защиты от коррозии.

В процессе создания кузовов из стали, задача конструкторов заключается в том, чтобы наделить материал прочностью и обеспечить высокий уровень пассивной безопасности. Задача технологов заключается в правильном подборе состава стали, его сочетание с другими сплавами и компонентами, чтобы материал был хорошо штампуем. Задача же металлургов заключается в том, чтобы правильно отлить нужную по составу и качеству сталь. Справочно заметим, что ежегодно разрабатываются десятки новых сортов и марок стали, которые позволяют упростить производство, а также получить заданные специалистами свойства несущей конструкции транспортного средства.

Как правило, изготовление кузова происходит в несколько стадий производственного процесса. Первоначально происходит изготовление, а затем прокатка стальных листов, которые обладают разной толщиной. После этого листы подвергают штамповке для создания определенных деталей машино-комплекта. На заключительной стадии готовые отштампованные детали свариваются специальным методом и собираются в единый несущий узел, он же кузов. Справочно заметим, что почти вся сварка на автозаводах производится специальными высокоточными роботами.

Положительные стороны стали при производстве автомобильных кузовов:
— низкая стоимость материала в сравнении с другим сырьем;
— четко отработанная технология изготовления и утилизации материала;
— оптимальная ремонтопригодность готового кузова.

— высокая масса материала и готового кузова;
— в обязательном порядке рекомендуется антикоррозионная обработка для защиты от коррозии и ржавчины;
— потребность в специальной штамповке и большом количестве штампов для скрепления деталей;
— не высокий срок службы готового кузова.

Что касается негативных сторон при производстве кузова из стали, то благодаря постоянному совершенствованию технологий изготовления автомобильных деталей, а также процесса штамповки, данный материал становится наиболее оптимальным для автопроизводителей. На сегодняшний день, доля высокопрочных сталей в структуре кузова постоянно увеличивается. Сегодня большинство автопроизводителей применяют сверхвысокопрочные сплавы стали нового поколения.

К таким видам материала относят такую марку стали, как TWIP, которая содержит большое количество марганца в своем составе, доля вещества может доходить до 25 процентов. Сталь такого типа обладает высокой пластичностью, устойчивостью к частым деформациям, благодаря чему материал можно подвергать относительному удлинению. Удлинение «ТВИП-стали» может происходит на 50-70 процентов, а пределом прочности служит показатель в 1450 МегаПаскаль. Для сравнения, прочность обычной стали составляет не более 250 МегаПаскаль, а высокопрочной до 600 МегаПаскаль.

ЧТО ТАКОЕ КРУПНОУЗЛОВАЯ СБОРКА АВТОМОБИЛЕЙ?
2. Изготовление кузова автомобиля из алюминия: преимущества и недостатки
Что касается автомобильных кузовов из алюминиевых сплавов, то их стали производить совсем недавно, примерно около 15 лет назад, для промышленности это считается маленьким сроком. Как правило, алюминий в автомобилестроении применяют для изготовления отдельных частей кузова, реже всего целиком. В большинстве случаев алюминий используется для производства капотов, крыльев, дверей, крышки багажника, а также прочих элементов и деталей.

Автопроизводителями на сегодняшний день сплавы из алюминия используются в ограниченном количестве. Все это из-за того, что жесткость и прочность алюминиевых сплавов намного ниже, чем у той же стали. В связи с чем толщину деталей из этого материала производители увеличивают, поэтому значительного снижения массы готового кузова получить почти невозможно. Кроме того, такой параметр, как шумоизоляция у алюминиевых деталей также хуже, чем у элементов из стали, к тому же при производстве требуются более сложные процедуры, чтобы достичь оптимального акустического эффекта и добиться положительных характеристик кузова по этому показателю.

Что касается производственного процесса, на котором изготавливают готовый алюминиевый кузов, то он очень схож с ранее описанной процедурой создания несущей конструкции из стали. На первой стадии, детали из листа алюминия подвергают штамповке, а затем собираются в единый цельный узел. При сварке применяется аргон, детали соединяются при помощи специальных заклепок или клея. На завершающей стадии, основные участки будущего кузова подвергают точечной сварке, а затем к стальному каркасу, изготовленному из труб разного сечения, прикрепляются кузовные панели и машино-комплекты.

Положительные стороны алюминия при производстве автомобильных кузовов:
— появляется возможность производства кузовных элементов любой формы и сложности;
— масса готового алюминиевого кузова значительно легче стального, при равной прочности;
— материал легко подвергается обработке, процесс утилизации прост;
— высокая устойчивость к коррозии и ржавчине;
— низкая стоимость технологических процессов при производстве.

— высокая сложность ремонта деталей;
— при производстве используются дорогостоящие крепежи для соединения панелей;
— необходимость наличия специального высокоточного оборудования;
— намного дороже стали, в связи с высокими энергозатратами.

Алюминий обладает средней пластичностью и устойчивостью к разного рода деформациям. Такой материал не рекомендуется подвергать удлинению, в связи с тонкой номинальной толщиной. Пределом прочности алюминия служит показатель в 180-210 МегаПаскаль. Для сравнения, прочность стандартной стали составляет около 240-250 МегаПаскаль, а высокопрочной в районе 500-600 МегаПаскаль.
3. Изготовление кузова автомобиля из стеклопластика и пластмассы: преимущества и недостатки
Что касается производства кузова из стеклопластика, то имеется в виду такой материал, как волокнистый наполнитель, который специально пропитывается полимерными смолами. Как правило, материал такого вида используется для облегчения общей массы готового кузова. Самыми известными наполнителями, он же стеклопластик являются стеклоткань, кевлар и карбон.

Справочно заметим, что примерно 85 процентов пластмасс, которые применяются в автомобилестроении, приходятся на 5 основных видов материалов, такие как полиуретаны, поливинилхлориды, ABS-пластик, полипропилены и стеклопластики. Около 15 оставшихся процентов приходится на полиэтилены, полиакрилаты, полиамиды, поликрбонаты и прочие материалы.

Кроме того, из разных видов стеклопластика производят наружные панели кузовов, что в свою очередь обеспечивает значительное снижение массы готового транспортного средства. Например из полиуретана изготавливают подушки и спинки сидений, накладки противоударного типа и прочие компоненты. Буквально, как пару лет назад из стеклопластика начали в массовом порядке производить такие элементы кузова, как капоты, крылья, двери и крышки багажников.

Положительные стороны стеклопластика при производстве автомобильных кузовов:
— имея высокую прочность, деталь имеет небольшой вес;
— внешняя поверхность элементов обладает оптимальными декоративными параметрами;
— простота изготовления элементов, которые имеют сложную форму;
— имеется возможность производства деталей крупных размеров.

Отрицательные стороны стеклопластика при производстве автомобильных кузовов:
— сравнительно высокая цена на наполнители;
— высокие требования к точности форм, разметке и готовой детали;
— производство деталей осуществляется продолжительное время;
— высокая сложность в ремонте при повреждении деталей.

Справочно заметим, что довольно часто такие материалы, как поливинилхлориды используются для производства фасонных деталей, например рукояток, панелей приборов и прочие элементы. Зачастую поливинилхлориды применяют совместно с обивочными материалами, на примере разных тканей. Что касается полипропилена, то из него часто изготавливают корпуса фар, рулевые колонки, воздуховоды и прочие элементы. ABS-пластик используют для облицовки деталей, как интерьера, так и экстерьера автомобиля.
Видео: «Из чего изготавливают кузов автомобиля? Какие материалы используются при производстве?»
В заключении отметим, что автомобильная промышленность сегодня не стоит месте и старается развиваться лицом к покупателю, который хочет динамичную, экономичную, надежную, безопасную и при этом недорогую машину. Все это ведет автомобилестроение к тому, что в производстве транспортных средств применяются новые технологии и материалы, которые отвечают современным требованиям, а также стандартам.
БЛАГОДАРИМ ВАС ЗА ВНИМАНИЕ. ПОДПИСЫВАЙТЕСЬ НА НАШИ НОВОСТИ. ДЕЛИТЕСЬ С ДРУЗЬЯМИ.
История кузова автомобиля | История, Кузов автомобиля
В книгах, написанных лет сто тому назад, говорилось, что «от экипажа требуется красота, изящество и удобство, как и от хорошего дома». Также не раз приходилось слышать, как кузов называют одеждой, костюмом автомобиля. Это образное название было достаточно верным, когда на раме шасси автомобиля укрепляли кузов старинного образца. Костяком, остовом машины служила рама; на ней монтировали все механизмы, а кузов играл роль красивой оболочки для зашиты пассажиров от ветра, пыли, холода и непогоды. Действительно, это был нарядный «костюм» автомобиля.
Каретные, а затем автокузовные мастера старались придать своим детищам как можно больше сходства с сооружениями строительной архитектуры, с мебелью и отделкой гостиных. Они не связывали своего творчества с идеей быстрого передвижения.
Громоздкие объемы, сложные формы, витиеватые украшения экипажей XIX века были вначале целиком перенесены на автомобили.
Однако со временем все возрастающая скорость потребовала изменения тогдашних привычных форм экипажа.
Для разработки нового вида автомобиля был использован опыт постройки гоночных машин, которые раньше других стали делать длинными, низкими, похожими на рыб. Автомобиль приобрел знакомые нам черты. Правда, сначала он представлял собой еще нечто среднее между каретой и гоночным автомобилем-снарядом. Но линии и формы его постепенно выпрямлялись, сглаживались. Развитие массового производства, особенно холодной штамповки, переход к металлическим закрытым кузовам после первой мировой войны еще более упростили форму автомобиля.
Одновременно с изменением формы автомобильного кузова прошла сложный путь и его конструкция.
Каркас кузова до середины 20-х годов был деревянным, с металлической, фанерной или кожаной облицовкой, как у карет. Крепление к раме осуществлялось болтами с войлочными прокладками или пружинами. Полуэластичное крепление вынуждало делать кузова массивными, иначе они быстро расшатывались, в них появлялись скрипы и стуки. Кузова с деревянным каркасом были дороги в производстве и почти неприемлемы для массового изготовления, в особенности тогда, когда форма их стала более скругленной.
Все это заставило конструкторов работать над созданием цельнометаллических, легких и удобных для массового производства кузовов. Внедрение их осуществлялось путем постепенной замены деревянных деталей металлическими, пока дерево не было полностью устранено из конструкции. Понемногу начали устранять и сами детали каркаса, заменяя их ребрами жесткости, выштампованными в панелях облицовки. Прогресс в холодной штамповке позволил применять панели больших размеров и сложной скругленной формы.
Кузов стал таким прочным и жестким, что невольно напрашивалась мысль использовать эти его качества для монтажа на нем механизмов, а тяжелую, громоздкую раму устранить.
Так и сделали.
Если прежнюю плоскую раму, покоящуюся на рессорах над передней и задней осями, можно сравнить по прочности и жесткости, с дощатым мостиком, переброшенным через канаву, то решетчатый стальной корпус несущего кузова подобен фермам хорошего металлического железнодорожного моста.
При правильном конструктивном решении общий вес несущей системы снижается на 10—15 процентов по сравнению с весом прежних рамы и кузова, вместе взятых.
С исчезновением рамы потеряло значение понятие «шасси». Кстати сказать, слово «шасси» по-французски означает — рама. Автомобиль с несущим кузовом не может существовать и передвигаться без кузова. Отнимите у него кузов — и механизмы повиснут в воздухе. Кузов и механизмы срослись в единое целое, и «костюм» сам стал своего рода механизмом, костяком автомобиля.
Несущими кузовами снабжены советские автомобили «Москвич», «Победа», «Волга», ЗИМ, автобусы Московского, Павловского и Львовского заводов.
У грузовых автомобилей дело обстоит иначе. Здесь, как правило, кузов не может заменить раму, так как кабина занимает небольшую часть длины автомобиля и жесткое соединение ее с рамой не может повлиять на жесткость конструкции в целом. Платформа же для грузов, занимающая большую часть длины машины, не является замкнутой коробкой и не может выполнять роль несущей конструкции. Однако в закрытых грузовых кузовах-фургонах все чаще применяется несущая конструкция.
Типы кузовов очень разнообразны. Основной тип кузова легкового автомобиля — закрытый, так называемый «седан» или «лимузин». В южных районах удобно применять кузов с откры вающейся крышей — «кабриолет» или «фаэтон». Специальные кузова имеют автомобили-фургоны для почты и развозки мелких товаров, кареты скорой помощи и другие.
Не менее обширен типаж кузовов грузовых автомобилей. Среди них платформы с откидными бортами, без бортов и с высокими решетчатыми бортами для легких сельскохозяйственных грузов, закрытые кузова, изотермические кузова с холодильными установками для скоропортящихся продуктов, кузова-самосвалы для перевозки сыпучих строительных материалов, цистерны для жидкостей, передвижные ремонтные мастерские, киноустановки.
Если добавить сюда городские, пригородные, туристские и междугородные автобусы, машины для уборки улиц, ремонта трамвайных проводов, пожарные, военные, то окажется, что количество основных марок легковых и грузовых автомобилей в несколько раз умножено разновидностями кузовов.
Современный кузов
Современный кузов — сложное сочетание механизмов и устройств. Так, кузов легкового автомобиля типа «Победа» — «Волга» состоит из 7—8 тысяч деталей. В то время как для большинства деталей двигателя и ходовой части материалом служит сталь, для кузова, кроме тонких стальных листов, требуются дерево, изделия из искусственного и натурального каучука, стекло и пластические массы, кожа, ткани, картон и десятки иных материалов.
Для изготовления и сборки деталей кузова приходится применять, кроме механической обработки, ковки, прокатки, еще и холодную штамповку на гигантских тысячетонных прессах, литье под давлением, сварку всех видов, чеканку, пайку, эмалирование, окраску, металлопокрытия.
Поэтому на современных автозаводах многие цехи в той или иной степени заняты производством кузовов и их деталей. Существуют и специальные кузовные цехи и даже кузовные заводы.
На долю кузова падает около половины веса автомобиля и примерно такая же часть его стоимости. Эта доля увеличилась особенно в последнее время, когда требования к удобствам кузова неизмеримо возросли.
Вентиляционно-отопительная установка, например, состоит из встроенных в корпус кузова труб, по которым свежий воздух вентиляторами подается в пассажирское помещение; фильтров, очищающих, осушающих или увлажняющих воздух; обогревателя (одного или нескольких).
Обогреватель заполнен горячей водой из системы охлаждения двигателя. Его створки направляют теплый воздух к сиденьям, а отходящие от него патрубки — к переднему стеклу. Это предохраняет стекло от запотевания и обледенения. Чтобы вентиляционно-отопительная установка работала надежно, чтобы кузов не слишком нагревался от солнечных лучей и не слишком охлаждался на морозе и ветре, не гудел, как барабан, при колебаниях автомобиля, внутреннюю поверхность кузова покрывают многослойной тепло- и звукоизоляцией из войлока, асбеста, резины, битумной мастики, пластических масс. Затем все это закрывают красивой обивкой.
Самый изысканный комнатный диван кажется очень простым по сравнению с автомобильным сиденьем. Пружины сиденья в кузове заключены в матерчатые чехлы. Чехлы предотвращают шум от касания одной пружины о другую, а заключенный в них воздух служит дополнительным пружинящим элементом подушки. Пружинный каркас подушки покрыт матрацем, в который входят разные материалы, как-то: войлок, прорезиненный волос, или губчатая резина, вата. В новейших конструкциях, впрочем, отказываются от таких сложных и дорогостоящих сидений, тем более, что эластичные шины и рессоры современного автомобиля хорошо защищают кузов от толчков.
Сиденье водителя снабжено специальным механизмом, с помощью которого оно, в зависимости от роста и телосложения водителя, может быть придвинуто к рулю и педалям или отодвинуто от них.
На дверях кузова смонтированы шестеренчатые, а иногда и кнопочные электрические или гидравлические механизмы подъема и опускания стекол, хитроумные замки, ограничители открывания дверей, резиновые уплотнители дверного проема, направляющие шипы и буферы. Окна кузова выполнены из небьющегося или безосколочного стекла.
И все это должно быть очень легким, прочным и дешевым.
Несущий кузов — Википедия
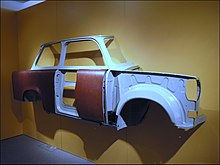
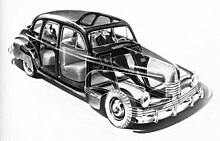
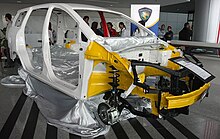
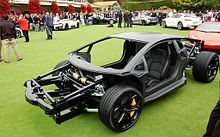
Несущий кузов — разновидность несущей системы автомобиля, при которой все элементы и связи кузова участвуют в воспринятии воздействующих на него нагрузок.
Автомобили с несущим кузовом также называют безрамными, так как функции рамы такого автомобиля выполняет сам кузов.
Стоит иметь в виду, что не во всех иностранных языках имеется термин, напрямую аналогичный понятию «несущий кузов». Так, если немецкое Selbsttragende Karosserie полностью соответствует по смыслу русскому «(само)несущий кузов», то уже английское Unibody, Unitised Body, обычно переводимое тем же словосочетанием, на самом деле означает «кузов, объединённый в единый сборочный узел» и может обозначать как собственно несущий кузов, так и жёстко объединённый с рамой полунесущий — то есть, здесь определяющим признаком является не способность воспринимать нагрузки, а физическое объединение кузова с несущей системой. Во французском языке для несущих кузовов используется термин Monocoque (а в других романских языках — «кальки» с него, например, исп. Monocasco, итал. Monoscocca), хотя в с инженерной точки зрения кузова серийных автомобилей почти никогда не бывают чистыми монококами.
По используемой силовой схеме выделяют безрамные автомобили с несущим основанием и с несущим корпусом.
У автомобилей с несущим основанием основную часть рабочих нагрузок, возникающих при движении автомобиля, воспринимает усиленное плоское днище кузова; у автомобилей с несущим корпусом их восприятие осуществляет объёмный каркас кузова (при практически не нагруженных кузовных панелях) или сама образованная кузовными панелями трёхмерная структура с местным усилением.
Также выделяют несущие кузова с замкнутой силовой структурой, у которых силовая структура образует замкнутый контур благодаря наличию крыши, сводящий вместе все вертикальные силовые элементы, и с незамкнутой силовой структурой, то есть — открытые, вроде кабриолетов и родстеров, а также пикапы и фургоны типа Иж-2715, у которых крыша грузового отсека не является несущей.
По конструктивному оформлению разделяют кузова (не только несущие) каркасно-панельные, скелетные, оболочковые, бескаркасно-скорлупные.
Каркасно-панельный несущий кузов имеет каркас из труб или штампованных металлических профилей, на который крепятся облицовочные панели, в очень незначительной степени повышающие его жёсткость. Такую конструкцию имели, к примеру, кузова мотоколясок С1Л и С3А, многие автобусы (например, ПАЗ-3204), а также — некоторые кузова с наружными панелями из пластиков, например, французской мотоколяски (квадрицикла с кузовом) Aixam A741 с алюминиевым каркасом и наружными панелями из АБС-пластмассы. Такой кузов прост в кустарном ремонте, в особенности при использовании стандартных профилей для каркаса и разъёмных (болтовых, заклёпочных) креплениях наружных панелей. Однако его производство трудоёмко, что делает его пригодным только для автомобилей со сравнительно небольшими масштабами выпуска. Кроме того, каркасно-панельный кузов при прочих равных будет наиболее тяжёлым, так как наружные панели в нём не участвуют в воспринятии нагрузок, вынуждая усиливать каркас.
Этот тип несущего кузова не следует путать с кузовом с пространственной рамой, у которого наружные облицовочные панели играют исключительно декоративную роль и вообще не участвуют в воспринятии нагрузки (как, например, у дрегстеров класса Funny Car, представляющих собой полностью разгруженный пластиковый обтекатель с лёгким подкреплением внутри, установленный на несущей пространственной раме из труб).
У скелетного (полукаркасного) кузова каркас в значительной степени редуцирован, он представлен отдельными стойками, дугами и усилителями, приваренными к наружным и внутренним облицовочным панелям, наравне с ним участвующим в воспринятии нагрузки. Такой кузов легче каркасного, но всё ещё достаточно сложен и трудоёмок в массовом производстве из-за большого количества сборочных операций, многие из которых выполняются вручную и требуют взаимных подгонок деталей.
Оболочковые (бескаркасные) кузова наиболее распространены, большинство современных несущих кузовов принадлежат к этому типу — они свариваются точечной сваркой из крупногабаритных внутренних и наружных панелей, отштампованных как правило из стального листа, которые вместе образуют замкнутую пространственную систему, в которой роль каркаса играют выштамповки на самих панелях. Данный вариант несущего кузова наиболее приспособлен для условий массового производства, экономичен и технологичен, однако его ремонт в процессе эксплуатации в значительной степени затруднён ввиду сложной формы панелей и малого числа их сопряжений, что зачастую даже при незначительных повреждения вынуждает целиком заменять всю панель. В настоящее время происходит распространение алюминиевые или композитные сталеалюминиевые несущие кузова, в производстве которых наряду со сваркой широко используются заклёпочные соединения и склеивание.
Скорлупные кузова представляют собой монокок из неметаллических материалов (стеклопластик, углепластик, термопластик и так далее) с минимальным локальным усилением.
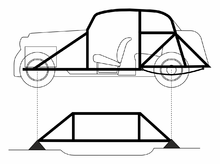
У несущего кузова различают нижний силовой пояс (днище с усилением — короба порогов, поперечины пола, раскосы пола, лонжероны), средний силовой пояс (щит передка, брызговики крыльев, вертикальные стойки, подоконные брусья) и верхний силовой пояс (каркас крыши и сама крыша). У несущего кузова с незамкнутой силовой структурой (кабриолета, отчасти пикапа) верхний силовой пояс отсутствует, а практически все нагрузки воспринимаются нижним силовым поясом.
С точки зрения характера работы несущий кузов с замкнутой силовой структурой может быть уподоблен пространственной ферме, элементы которой (стержни) образованы либо каркасом (у каркасно-панельного кузова), либо конфигурацией оболочки кузова и прикреплёнными к ней усилителями (короба порогов, стойки и прогоны крыши, подоконные брусья и т. п.). Соответственно, для приближённого расчёта несущего кузова на прочностью используются примерно те же методики, что и для мостовых ферм и подобных конструкций (в настоящее время для этой цели широко используется конечно-элементный анализ напряжённых состояний системы с использованием вычислительной техники).
Несущий кузов с незамкнутой силовой структурой (кабриолет, родстер) может с той же точки зрения быть уподоблен балке.
Кузов — это… Что такое Кузов?
Ку́зов — это часть автомобиля или другого транспортного средства, предназначенная для размещения пассажиров и груза. Кузов крепится к раме автомобиля. Распространены безрамные несущие кузова, выполняющие одновременно функцию рамы — к ним крепятся все остальные узлы и агрегаты автомобиля.
История развития
Форма автомобиля зависит от компоновки и конструкции, от применяемых материалов и технологии изготовления кузова. В свою очередь, возникновение новой формы заставляет искать новые технологические приёмы и новые материалы. На развитие формы автомобиля воздействуют социально-экономические факторы и, в силу особого качества автомобиля — его «престижности», мода.
Грузовой автомобиль
У грузовика кузов состоит из кабины водителя и грузовой платформы (часто только её и называют кузовом).
Легковой автомобиль
Первым стали систематически и целенаправленно заниматься художественным конструированием автомобиля американцы. В 1926 г. концерн General Motors создал группу по художественному конструированию. А уже в 1927 г. была выпущена модель La Salle, спроектированная художниками-конструкторами. Её успех, как отметили современники, дал профессии дизайнера отличную рекламу.
Классическая компоновка
Автомобиль быстро развивался. Двигатель занял довольно неудобное для размещения пассажиров место — между большими крыльями передних управляемых колёс; радиатор разместился спереди — для охлаждения его встречным потоком воздуха; ведущие колёса — задние, что выгодно для улучшения тяговых качеств автомобиля. С конструктивной точки зрения такая компоновочная схема оказалась вполне рациональной; совершенствуясь, она сохранилась до наших дней и получила название «классическая компоновка». Двигатель, трансмиссия, ходовая часть крепились к раме. Всё в целом называлось «шасси». Шасси могло двигаться и существовать без кузова. Кузов устанавливался на шасси как отдельный и независимый для выполнения агрегат. С кузовом получался уже автомобиль, предназначенный для выполнения определённой функции.
Галерея
-
Развитие формы кузова
-
-
Развитие классической компоновки легкового авто
-
Схема композиционного построения формы авто
-
Схема композиционного построения формы авто-2