Применение кулачковых кривошипно шатунных и рычажных механизмов в машинах – Кривошипно-шатунный Механизм Двигателя, Назначение, Принцип Действия и Характеристика КШМ, Диагностика и Ремонт Неисправностей, Конструкция с Чертежами и Схемами
- 24.11.2020
Кривошипно-шатунный и кулачковый механизмы: устройство, назначение область применения.
⇐ ПредыдущаяСтр 22 из 22В современных машинах и приборах широкое применение получили рычажные механизмы и в первую очередь кривошипно – шатунный механизм (см. модель), состоящий из стойки 1, кривошипа 2, шатуна 3, ползуна 4
Кривошипно-шатунный механизм служит для преобразования вращательного движения кривошипа в возвратно-поступательное прямолинейное движение ползуна. Наоборот, когда ведущим звеном является ползун, возвратно-поступательное прямолинейное движение ползуна преобразовывается во вращательное движение кривошипа и связанного с ним вала.
Кривошипно-шатунные механизмы широко применяют в поршневых двигателях, компрессорах, прессах, насосах и т. д.
Если прямая хх, по которой движется центр шарнира, проходит через ось вращения кривошипа О, то механизм носит название центрального.
В некоторых случаях необходимо найти аналитические зависимости — перемещения, скорости и ускорения ползуна кривошипно-шатунного механизма от угла поворота кривошипа.
Перемещение ползуна в зависимости от угла поворота кривошипа:
S = r (1-cos a)
Скорость ползуна определяется:
V=S/a = w r sin a
Ускорение ползуна:
a = w2r cos a
Кулачковые механизмы применяют в тех случаях, когда перемещение, скорость и ускорение ведомого звена должны изменяться по заранее заданному закону, в частности, когда ведомое звено должно периодически останавливаться при непрерывном движении ведущего звена.
Чаще всего кулачковый механизм состоит из трех звеньев
кулачка 1, толкателя 2 и стойки З. На рис. Б представлен четырехзвенный кулачковый механизм (четвертое звено — ролик 4)
Кулачковьте механизмы подразделяются на плоские и пространственные. Плоскими называют такие кулачковые механизмы, у которых кулачок и толкатель перемещаются в одной или параллельных плоскостях; пространственным и — такие, у которых
На рис. представлена схема пространственного и цилиндрического кулачкового механизма с профильным пазом на боковой поверхиости. Для увеличения стойкости кулачки изготовляют из высококачественной стали с рабочей поверхностью высокой твердости. С целью уменьшения трения и износа на толкателе устанавливают ролик, который вращается на оси и катится без скольжения по рабочей поверхности кулачка (рис. 1, б).
Кроме износа звеньев недостатком кулачковых механизмов является необходимость обеспечивать постоянное соприкосновение (замыкание) между звеньями. В процессе работы кулачкового механизма могут возникать большие усилия, главным образом инерционные, направленные на отрыв рабочей поверхности толкателя от кулачка. Для восприятия этих усилий применяется либо геометрическое (кинематическое), либо силовое замыкание кинематической цепи.
Геометрическое (кинематическое) замыкание применено в механизме с пазовым кулачком. Толкатель движется поступательно. При вращении кулачка ролик толкателя соприкасается с боковыми сторонами паза, про резанного на кулачке. Паз создает два рабочих профиля кулачка, которые перемещают ролик толкателя в обоих направлениях.
При силовой замыкании толкатель во всех положениях при жат к кулачку с силой, которая больше силы, стремящейся оторвать толкатель от кулачка. Замыкающая сила в подавляющем большинстве случаев создается пружиной
К числу недостатков кулачковых механизмов следует отнести сложность изготовления профиля кулачка, от которого требуется большая точность. В тех случаях, когда толкатель должен перемещать с периодическими остановками, участки профиля кулачка, соответствующие этим периодам, должны быть очерчены дугами окружности, проведенными из центра вращения кулачка.
15.Основные требования к машинам и деталям машин. Характеристики некоторых машиностроительных материалов. Краткие сведения о стандартизации и взаимозаменяемости машин.
Как указано в решениях ГОСТ, потребности социалистического производства, имеющего основной целью всемерное неуклонное повышение благосостояния трудящихся, определяют основные тенденции в развитии советского машиностроения: увеличение производительности и мощности машин, скоростей, давлений и других показателей интенсивности технологических процессов, повышение к. п. д. машин, уменьшение их массы и габаритов, широкую автоматизацию управления машинами, повышение их надежности и долговечности, снижение стоимости изготовления, повышение экономической эффективности эксплуатации, удобства и безопасности обслуживания.
С этими тенденциями непосредственно связаны общие требования, предъявляемые к машинам независимо от их назначения: высокая производительность; высокий к. п. д.; удобство и простота сборки, разборки, обслуживания и управления; низкая стоимость изготовления; надежность; долговечность и безопасность в работе; малые габариты и масса. Отсюда вытекают следующие основные требования к деталям любой машины:
прочность — деталь не должна разрушаться или получать остаточные деформации под влиянием действующих на нее сил в течение заданного срока службы;
жесткость — упругие перемещения, возникающие в детали под влиянием действующих на нее сил, не должны превышать некоторых допустимых заранее заданных величин;
износостойкость — износ детали в течение заданного срока службы не должен вызывать нарушения характера сопряжения ее с другими деталями и приводить к недопустимому уменьшению ее прочности;
недефицитность материалов — удовлетворение всех предыдущих требований не должно осуществляться за счет применения дефицитных материалов, так как использование таких материалов приводит к резкому увеличению стоимости детали;
технологичность — форму и материал детали желательно выбирать такими, чтобы изготовление ее требовало наименьших затрат труда и времени;
соответствие государственным стандартам — деталь должна удовлетворять действующим стандартам на формы, размеры, сорта и марки материала.
Наиболее распространенными материалами в машиностроении являются стали различных марок, чугуны, бронза, пластмассы, древесина, резина и др. Работа с таблицей стр. 170
Краткие сведенья о стандартизации и взаимозаменяймости деталей машин
Стандартизацией называется установление обязательных норм, которым должны соответствовать типы, сорта (марки), параметры (в частности, размеры), качественные характеристики, методы испытаний, правила маркировки, упаковки, хранения продукции (сырья, полуфабрикатов, изделии).
Для обеспечения единых норм и технических требований к продукции, обязательных для всех отраслей народного хозяйства СССР, установлены Государственные общесоюзные стандарты — ГОСТы.
В машиностроении, например, стандартизованы:
— обозначения общетехнических величин, правила оформления чертежей: ряды чисел, распространяемые на линейные размеры;
— точность и качество поверхностей деталей;
— материалы, их химический состав, основные механические свойства и термообработка;
— форма и размеры деталей и узлов наиболее массового применения: болтов, винтов, шпилек, гаек, шайб, шплинтов, заклепок, штифтов, шпонок, ремней, цепей, муфт, подшипников качения;
Кроме общесоюзной существует также ведомственная стандартизация, которую принято называть нормализацией. Нормализация проводится в пределах какой-либо одной отрасли производства или даже одного завода. Со стандартизацией тесно связана унификация деталей и узлов машин.
Унификацией называется устранение излишнего многообразия изготовляемых изделий, сортамента материалов и т. п. путем сокращения их номенклатуры, а также использования в ранных (по размерам и назначению) машинах общих узлов и деталей.
Таким образом, узлы и детали, спроектированные однажды для какой-либо машины, без изменений используются в других машинах.
Широкое внедрение стандартизации обеспечивает возможность массового производства деталей на специализированных заводах, приводит к уменьшению трудоемкости и стоимости их изготовления.
Важнейшей чертой современного машиностроения является взаимозаменяемость, без которой невозможно было бы серийное и массовое производство машин.
Взаимозаменяемостью называется свойство деталей или узлов машин, обеспечивающее возможность их использования при сборке без дополнительной обработки (пригонки) при соблюдении технических требований, предъявляемых к работе данного узла, механизма, машины.
Для стран — членов Социалистического Экономического Содружества предусмотрена комплексная программа по стандартизации. Разработана единая для этих стран система допусков и посадок (ЕСДП СЭВ) и установлен ряд стандартов, соблюдение которых обязательно.
Реализация Комплексной программы СЭВ по стандартизации повышает эффективность экономического и научно-технического сотрудничества стран — членов СЭВ (взаимозаменяемость, единство технической документации) для успешного сотрудничества стран — членов СЭВ в области машиностроения и приборостроения.
ПРИМЕНЕНИЕ КУЛАЧКОВЫХКРИВОШАТУННЫХ И РЫЧАЖНЫХ МЕХАНИЗМОВ РАБОТУ ВЫПОЛНИЛ ШЛЯХТОВ
ПРИМЕНЕНИЕ КУЛАЧКОВЫХКРИВОШАТУННЫХ И РЫЧАЖНЫХ МЕХАНИЗМОВ РАБОТУ ВЫПОЛНИЛ ШЛЯХТОВ ДМИТРИЙ
Кривошипно-шатунные механизмы q Кривошипно-шатунные механизмы служат для преобразования вращательного движения в возвратнопоступательное и наоборот. Основными деталями кривошипно-шатунного механизма являются: кривошипный вал, шатун и ползун, связанные между собой шарнирно. q В кривошипно-шатунном механизме вместо кривошипного вала часто применяют коленчатый вал. От этого сущность действия механизма не меняется. Коленчатый вал может быть как с одним коленом, так и с несколькими. q В некоторых кривошипно-шатунных механизмах приходится менять и длину хода ползуна. У кривошипного вала это делается обычно так. Вместо цельного выгнутого кривошипа на конец вала насаживается диск (планшайба). Шип (поводок, на что надевается шатун) вставляется в прорез, сделанный по радиусу планшайбы. Перемещая шип по прорезу, то есть удаляя его от центра или приближая к нему, мы меняем размер хода ползуна.
Кулачковые механизмы q Кулачковые механизмы служат для преобразования вращательного движения (кулачка) в возвратнопоступательное или другой заданный вид движения. Механизм состоит из кулачка — криволинейного диска, насаженного на вал, и стержня, который одним концом опирается на криволинейную поверхность диска. Стержень вставлен в направляющую втулку. Для лучшего прилегания к кулачку, стержень снабжается нажимной пружиной. Чтобы стержень легко скользил по кулачку, на его конце устанавливается ролик. q Но бывают дисковые кулачки другой конструкции. Тогда ролик скользит не по контуру диска, а по криволинейному пазу, вынутому сбоку диска. В этом случае нажимной пружины не требуется. Движение ролика со стержнем в сторону осуществляется самим пазом. q Кроме рассмотренных нами плоских кулачков , можно встретить кулачки барабанного типа. Такие кулачки представляют собой цилиндр с криволинейным пазом по окружности. В пазу установлен ролик со стержнем. Кулачок, вращаясь, водит криволинейным пазом ролик и этим сообщает стержню нужное движение. Цилиндрические кулачки бывают не только с пазом, но и односторонние — с торцовым профилем. В этом случае нажим ролика к профилю кулачка производится пружиной.
Длину хода стержня или рычага кулачкового механизма можно легко рассчитать. Она будет равна разнице между малым радиусом кулачка и большим. Например, если большой радиус равен 30 мм, а малый 15, то ход будет 30 -15 = =15 мм. В механизме с цилиндрическим кулачком длина хода равняется величине смещения паза вдоль оси цилиндра.
Шарнирно-рычажные механизмы q Часто в машинах требуется изменить направление движения какой-либо части. Допустим, движение происходит горизонтально, а его надо направить вертикально, вправо, влево или под каким-либо углом. Кроме того, иногда длину хода рабочего рычага нужно увеличить или уменьшить. Во всех этих случаях применяют шарнирно-рычажные механизмы.
Кулисный механизм: виды, конструкция, назначение
Кулисная пара – это разновидность рычажных механизмов. Она преобразует вращательное движение в возвратно-поступательное или наоборот. При этом вращающееся звено может совершать не полный оборот. Тогда его называют качательным. Механизм состоит их двух основных звеньев- кулисы и ползуна. Один конец кулисы закреплен на неподвижной оси.
Кулисный механизм
Кулиса представляет собой прямой или изогнутый рычаг с прорезью, в которой скользит конец другого рычага. Он движется относительно кулисы прямолинейно. Кулисные механизмы бывают качающиеся, вращающиеся и прямые.
Кривошипно-кулисные механизмы способны обеспечивать высокую скорость линейного перемещения исполнительных органов. Характерным примером механизма кулисного типа служит система управления клапанами в автомобильных моторах, устройство управления реверсом парового двигателя и т. д.
Используются кулисные пары в металлообрабатывающих и деревообрабатывающих станках, там, где рабочий орган должен совершать многократные линейные перемещения с возвратным ходом.
Еще одна область применения- аналоговые вычислительные устройства, там кулисные пары помогают определять значения синусов либо тангенсов заданных углов.
Виды кулисных механизмов
В исходя из типа подвижного звена рычажной схемы в установках и подвижных узлах используются следующие виды кулисных пар:
- Ползунный. Система рычагов, состоящая из четырех звеньев. Основные части- это кулиса и ползун с зафиксированной направляющей. Она дает ползуну единственную степень свободы, для совершения линейных перемещений. Качания кулисы превращаются устройством в линейное перемещение ползуна. Кинематическая схема обратима- возможно и обратное преобразование движения.
- Кривошипный. Кривошипно-кулисного механизм построен по четырехрычажной кинематической схеме. Передает вращение кривошипа кулисе, также вращающейся или качающейся. Распространен в промышленных установках, например — в продольно-долбежных и строгальных. Для них применяют кривошипно-коромысловый механизм c вращающейся кулисой. Такая схема обеспечивает очень высокую скорость прямого ходя и медленный возврат. Применяется также в установках для упаковки.
- Двухкулисный. В кинематической четырехзвенной схеме есть пара кулис. Передается вращение или качание через промежуточный рычаг. Передаточное число неизменно и всегда составляет единицу. Применяется в компенсирующих муфтах.
- Коромысловый. Состоит из коромысла, кулисы и связывающего их шатуна. Позволяет располагать оси симметрии зон движения, ведущего и ведомого звеньев под углом около 60°. Находит применение в автоматизированных производственных линиях
Реже находит применение в транспортных средствах и некоторых измерительных приборах стоящий несколько особняком прямолинейно- направляющий или конхоидальный механизм.
Конструктивные особенности
Устройство является одним из подвидов кривошипно-шатунного механизма. Большинство кулисных пар построены по четырехзвенной кинематической схеме.
Третье звено определяет тип механизма: двухкулисный, ползунный, коромысловый или кривошипный.
Схема содержит как минимум две неподвижные оси и от одной до двух подвижных осей.
В середине кулисы располагается прорезь, по которой перемещается подвижная ось. К ней шарнирно закреплен конец (или другая часть) ползуна, коромысла или второй кулисы.
В зависимости от соотношения длин в каждый момент исполнительный орган может описывать как простые траектории (линейные, круговые или часть окружности), таки сложные в виде многоугольников или замкнутых кривых. Вид траектории определяется законом движения кинематической пары – функцией координат исполнительного органа от угла поворота оси, положения ползуна или от времени.
Принцип действия механизма
Принцип действия основывается на базовых законах прикладной механики, кинематики и статики, описывающий взаимодействие системы рычагов, имеющих как подвижные, так и неподвижные оси. Элементы системы полагаются абсолютно жесткими, но обладающими конечными размерами и массой. Исходя из распределения масс рассчитывается динамика кулисного механизма, строятся диаграммы ускорений, скоростей, перемещений, рассчитываются эпюры нагрузок и моментов инерции элементов.
Силы считаются приложенными к бесконечно малым точкам.
Рычажное устройство, имеющее два подвижных элемента (кулиса и кулисный камень) называют кинематической парой, в данном случае кулисной.
Чаще всего встречаются плоские схемы из четырех звеньев. Исходя из вида третьего звена рычажного механизма, различают кривошипные, коромысловые, двухкулисные и ползунные механизмы. Каждый из них обладает собственным способом преобразования вида движения, но все они используют единый прицеп действия- линейное или вращательное перемещение рычагов под действием приложенных сил.
Траектория движения каждой точки кривошипно кулисного механизма определяется соотношением длин плеч и рабочими радиусами элементов схемы.
Вращающееся или качающееся звено системы рычагов оказывает воздействие на поступательно движущееся звено в точке их сочленения. Оно начинает перемещение в направляющих, оставляющих этому звену только одну степень свободы, и движется до тех пор, пока не займет крайнее положение. Это положение соответствует либо первому фазовому углу вращающегося звена, либо крайнему угловому положению качающегося. После этого при продолжении вращения или качании в обратную сторону прямолинейно движущееся звено начинает перемещение в обратном направлении. Обратный ход продолжается до тех пор, пока не будет достигнуто крайнее положение, соответствующее либо полному обороту вращающегося звена, либо второй граничной позиции качающегося.
После этого рабочий цикл повторяется.
Если кулисный механизм, наоборот, преобразует поступательное движение во вращательное, взаимодействие осуществляется в обратном порядке. Усилие, передаваемое через сочленение от ползуна, прикладывается в стороне от оси вращения звена, обладающего возможностью поворота. Возникает крутящий момент, и вращающееся звено начинает поворачиваться.
Преимущества и недостатки кулисного механизма
Основным достоинством устройства служит его способность обеспечить высокую линейную скорость возвратного движения. Это свойство нашло применение в станках и механизмах, которые по условиям работы имеют холостой возвратный ход. Это прежде всего долбежные и строгальные станки. Применение кулисно-рычажного механизма привода позволяет существенно повысить общую эффективность использования установки, сократив время на непроизводительные такты.
Преимуществом двухкулисных систем, применяемых в аналоговых вычислительных устройствах, служит высокая надежность и стабильность их работы. Они отличаются высокой устойчивостью к таким факторам внешней среды, ка вибрации и электромагнитные импульсы. Это обуславливало их широкое применение в системах сопровождения целей и наведения вооружений.
Недостатком данной кинематической схемы является малые передаваемые усилия. Кривошипно-шатунная схема позволяет предавать в несколько раз большую мощность.
Недостатком аналоговых вычислительных устройств является исключительная сложность или даже невозможность их перепрограммирования. Они могут вычислять только одну, наперед заданную функцию. Для вычислительных систем общего назначения это неприемлемо. С развитием программно- аппаратных средств цифровой техники, повышением ее надежности и устойчивости к воздействиям внешней среды такие вычислительные системы сохраняются в нишах узкоспециальных применений.
Проектирование (производство) кулисного механизма
Несмотря на кажущуюся простоту устройств кулисного механизма, для того, чтобы он работал эффективно, требуется провести большую работу по его расчету и проектированию. При этом рассматриваются следующие основные аспекты:
- производительность и КПД;
- себестоимость производства и эксплуатации;
- отказоустойчивость и межремонтный ресурс;
- точность действия;
- безопасность.
Учитывая сложность взаимовлияния этих аспектов друг на друга, расчет кривошипно-кулисного механизма представляет из себя многоступенчатую итеративную задачу.
В ходе проектирования проводят следующие виды расчета и моделирования:
- расчет кинематики;
- динамический расчет;
- статический расчет.
Обычно проектирование и расчет разбивается на следующие этапы:
- Определение требуемого закона движения расчетно-аналитическим или графоаналитическим методом.
- Кинематическое моделирование. Выполнение общего плана, скоростного плана, графическое моделирование моментов инерции, графика энерго-массовых зависимостей.
- Силовое моделирование. Построение плана ускорений, эпюр сил, приложенных к звеньям в нескольких положения.
- Синтез кулисно-рычажного механизма. Построение графиков перемещения, скорости, ускорений графико-дифференциальным методом. расчет динамики кулисного механизма и его динамический синтез.
- Проверка на соответствие закону движения. Окончательное профилирование кулис.
- Проверка на соблюдение норм безопасности и охраны труда.
- Выпуск чертежей.
Расчет и проектирование кулисного механизма долгое время представлял собой весьма трудоемкий процесс, требовавший большого сосредоточения и внимательности от конструктора. В последнее время развитие средств вычислительной техники и программных продуктов семейства CAD-CAE существенно облегчил все рутинные операции по расчету. Конструктору достаточно выбрать подходящую кинематическую пару или звено из поставляемых производителем программ библиотек и задать их параметры на трехмерной модели. Существуют модули, на которых достаточно отобразить графически закон движения, и система сама подберет и предложит на выбор несколько вариантов кинематической его реализации.
Область применения
Кулисные механизмы находят применение в тех устройствах и установках, где требуется преобразовать вращение или качание в продольно- поступательное перемещение или сделать обратное преобразование.
Наиболее широко они используются в таких металлообрабатывающих станках, как строгальные и долбежные. Важное преимущество кулисно-рычажного механизма, заключается в его способности обеспечивать высокую скорость движения на обратном ходе. Это дает возможность существенно повысить общую производительность оборудование и его энергоэффективность, сократив время, затрачиваемое на непроизводительные, холостые движения рабочих органов. Здесь же находит применение кулисный механизм с регулируемой длиной ползуна. Это позволяет наилучшим образом настаивать кинематическую схему исходя из длины заготовки.
Механизм конхоидального типа применяется в легком колесном транспорте, приводимом в действие ножной мускульной силой человека- так называемом шагоходе. Человек, управляющий машиной, имитируя шаги, поочередно нажимает на педали механизма, закрепленные на оси с одного конца. Кулисная пара преобразует качательное движение во вращение приводного вала, передаваемое далее цепным или карданным приводом на ведущее колесо.
В аналоговых вычислительных машинах широко применялись так называемые синусные и тангенсные кулисные механизмы. Для визуализации различных функции в них применяются ползунные и двухкулисные схемы. Такие механизмы использовались в том числе в системах сопровождения целей и наведения вооружений. Их отличительной чертой являлась исключительная надежность и устойчивость к неблагоприятным воздействиям внешней среды (особенно- электромагнитных импульсов) на фоне достаточной для решения поставленных задач точности. С развитием программных и аппаратных средств цифровой техники область применения механических аналоговых вычислителей сильно сократилась.
Еще одна важная сфера применения кулисных пар- устройства, в которых требуется обеспечить равенство угловых скоростей кулис при сохранении угла между ними. Муфты, в которых допускается неполная соосность валов, системы питания автомобильных двигателей, устройство реверса на паровом двигателе.
Если вы нашли ошибку, пожалуйста, выделите фрагмент текста и нажмите Ctrl+Enter.
Статья на тему «Рычажные механизмы Часть 1»
Описание
Рычажные механизмы. Часть 1
К рычажным механизмам относятся механизмы, состоящие из звеньев совершающих вращательное, поступательное или плоско – параллельное движение. Эти механизмы отличаются простотой, высоким КПД и большой нагрузочной способностью, однако они не могут обеспечить любой закон движения ведомого звена, что в некоторой степени ограничивает их применение в технике.
В технологическом оборудовании широко используются следующие виды рычажных механизмов: механизмы шарнирного четырехзвенника, кривошипно-шатунные механизмы, кулисные механизмы. Рассмотрим примеры и конструктивные особенности рычажных механизмов.
Механизмы шарнирного четырехзвенника
Механизмы шарнирного четырехзвенника в свою очередь делятся на три типа: двухкривошипные, в которых ведущее и ведомое звено могут совершать полный оборот (см. Рис. 1а), кривошипно-коромысловые, в которых ведущее звено кривошип вращается, а ведомое коромысло совершает качательное движение (см. Рис. 1б) и двух коромысловые, в которых и ведущее и ведомое звенья совершают качательное движение (см. Рис. 1в).
Примером двухкривошипного механизма может служить механизм переноса длинномерной заготовки из углового проката со стеллажа на рольганг технологического оборудования, конструктивная схема которого показана на Рис. 2. Он состоит из двух четырехлучевых звездочек 1 и 2, установленных на валах 3 и шарнирно соединенных между собою посредством осей 5 четырьмя ложементами 4, в которые укладываются при переносе заготовки 6, образуя, таким образом, четыре двухкривошипных механизма. При этом валы 3 на подшипниках скольжения расположены в корпусах 7 и 8, которые посредством кронштейнов 9 установлены на общей раме 10.
Еще одним представителем механизмов шарнирного четырехзвенника являются двухкоромысловые механизмы (см. Рис. 3), которые применяется, как правило, для изменения (увеличения, уменьшения) угла качания ведомого коромысла или изменения создаваемого на нем усилия.
На Рис. 3а показан двухкоромысловый механизм, конструкция которого (соотношение длин и взаимное расположение коромысел 1 и 3) позволяет увеличить угол качания β ведомого коромысла 3 по отношению к углу качания α ведущего коромысла 1. На Рис. 3б показан двухкоромысловый механизм, конструкция которого (соотношение длин и взаимное расположение коромысел 1 и 3) позволяет уменьшить угол качания β ведомого коромысла 3 по отношению к углу качания α ведущего коромысла 1. Если в механизме, показанном на Рис. 3а, ведущим будет звено 3 совершающее вращение с полным оборотом, а в механизме, показанном на Рис. 3б, его ведущее звено 1 будет совершать полный оборот, то эти двухкоромысловые механизмы превратятся в кривошипно-коромысловые. Данные механизмы редко применяются в качестве силовых исполнительных механизмов машин и оборудования, поскольку могут работать только при ограниченной величине углов качания (60 – 90 град.) из-за возрастающей величины потерь при передаче усилий от ведущего звена к ведомому, при увеличении углов качания кривошипов. Такие механизмы обычно используются как вспомогательные, работающие с небольшими скоростями и нагрузками. Рассмотренный тип механизмов часто используется в качестве исполнительного в различного рода кантователях.
Рис. 4. Кантователь для опрокидывания стола формовочной машины.
На Рис 5 показана конструкция сварочного кантователя, поворотные губки
которого являются ведомыми коромыслами шарнирных четырехзвенников имеющих общее ведущие коромысло. Он содержит, установленный на раме 1, приводной пневмоцилиндр 2, шток 3 которого посредствам двуплечего рычага 7, ведомое плечо которого является ведущим коромыслом двух шарнирных четырехзвенников содержащих тяги 8 и 9, шарнирно соединенные с устновленными на общей оси 4 поворотными губками 5 и 6, являющимися ведомыми коромыслами этих четырехзвенников.
Работает кантователь следующим образом. После окончания сварки первого шва изделия 11 подается команда на включение пневмоцилиндра 2, шток 3 которого втягивается и сводит поворотные губки 5 и 6, устанавливая, при этом, свариваемое изделие 11 в вертикальное положение (в это время опорные ролики 10 перекатываются по полке изделия). В результате этого центр тяжести свариваемого изделия 11 перемещается на противоположную сторону опорной призмы (на Рис 5 не показана) и при последующем разведении рычагов 5 и 6, что происходит при выдвижении штока 3 пневмоцилиндра 2, изделие укладывается в положение удобное для сварки второго шва.
В данном разделе полной версии статьи содержится 9 примеров
конструктивного исполнения механизмов шарнирного
четырехзвенника (см. Рис. в таб.) с описание их работы
Кривошипно-шатунные механизмы
Кривошипно-шатунные механизмы из всех видов рычажных механизмов получили наибольшее распространение в технике благодаря простоте кинематики, позволяющей сравнительно легко преобразовывать вращательное движение в поступательное, что позволяет использовать их в исполнительных механизмах технологического оборудования, например, в механических прессах, и поступательное движение во вращательное, что позволяет их использовать как исполнительный меха- низм двигателя внутреннего сгорания. Кривошипно-шатунный механизм состоит из, установленного в станине с возможностью вращения кривошипа 1 (коленчатого или эксцентрикового вала), шарнирно соединенного с ним шатуна 2, который шарнирно соединен с ползуном 3, осуществляющим при вращении кривошипа 1 возвратно-поступательное движение в направляющих станины 4 (см. Рис. 9).
Рис. 9. Кривошипно-шатунный механизм.
В данном разделе полной версии статьи содержится 9 примеров
конструктивного исполнения кривошипно – шатунных
механизмов (см. Рис. в таб.) с описанием их работы
Кулисные механизмы
Кулисные механизмы – это механизмы, содержащие два специфических звена: кулису и кулисный камень (см. Рис. 16), каждое из которых, совершая вращательное или качательное движение, поступательно перемещаются друг относительно друга. Наличие двух таких звеньев в механизме приводит к различной скорости перемещения ведомого звена, при его прямом и обратном ходе, что в отдельных случаях является преимуществом механизма, а в отдельных случаях недостатком и в целом определяет область его использования. Существует два основных типа кулисных механизмов различающихся по тому, какое движение совершает кулиса, это механизмы с качательным
Где используется механизм кулисный?
Если говорить о кулисном механизме, то начать стоит с того, что «кулиса» — это французское слово, которое можно перевести на наш язык, как «деталь» или же «звено».
Общая информация
С технической точки зрения под кулисным механизмом понимают устройство, задачей которого является преобразовывать вращательное или же качательное движение в возвратно-поступательное. Однако данный механизм может выполнять и обратную функцию. Если говорить об общей классификации данного устройства, то оно может быть трех типов — это вращающийся тип, качающийся тип или движущийся прямолинейно. Однако, если разбираться в сути кулисного механизма, то становится понятно, что любую его разновидность можно отнести к рычажному типу устройств. Кроме того, важно отметить, что работа кулисы осуществляется в паре с еще одной деталью, которая называется ползун. Данная деталь также является вращающейся частью в общей конструкции механизма.
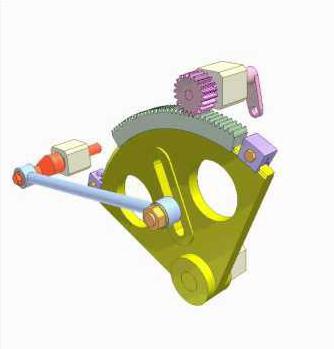
Преимущества и материал
Основным преимуществом данного механизма является обеспечение довольно высокой скорости ползуна, которую он развивает при выполнении обратного хода. Данное преимущество привело к тому, что такое устройство стало очень широко использоваться в том оборудовании, которое имеет холостой обратный ход. К тому же, если мы будем сравнивать кулисный механизм с кривошипно-шатунным, к примеру, то первый способен транслировать намного меньше усилия в сравнении со вторым.

Чаще всего кулисное устройство используется для того, чтобы как можно эффективнее преобразовывать равномерное вращательное движение кривошипа во вращательное движение непосредственно кулисы. Стоит отметить, что это движение осуществляется неравномерно. Однако бывают случаи, когда движение кулисы будет все же равномерным. Чаще всего это происходит в том случае, если расстояние между опорами кривошипа и его кулисой равняется длине самого кривошипа. В такой системе кулисный механизм будет одновременно являться еще и кривошипно-шатунным, который снабжен кулисой с равномерным движением.
Конструкция и распространение механизма
На сегодняшний день самой распространенной конструкцией кулисы является четырехзвенная. Кроме того, все конструкции этого типа можно классифицировать на несколько групп в зависимости от того, какого типа третье звено в устройстве. Существуют такие классы, как: двухзвенные, кулисно-ползунные, кулисно-коромысловые, кривошипно-кулисные.
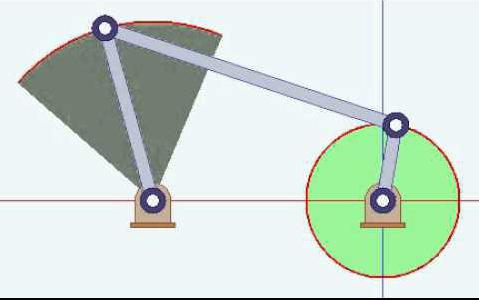
Наиболее частое применение эти механизмы находят в различного рода станках, таких как зубодолбежные, поперечно-строгальные и другие станки, которые можно отнести к металлорежущим типам. Суть кулисного механизма заключается в том, что эта одна из множества разновидностей кривошипно-шатунного. К использованию механизма с кулисой прибегают в том случае, если есть необходимость в оборудовании преобразовать вращательное движение в возвратно-поступательное. В строгальных типах станков применяется качающегося типа кулиса, а в долбежных станках устанавливается кулиса вращающегося типа.
Конструкция четырехзвенного механизма
Четырехзвенный кулисный механизм с кулисным камнем — это система, которую можно рассмотреть на примере строгального станка, где используется именно такой тип устройства. Работу данной системы можно описать следующим образом. Кривошип осуществляет круговое движение вокруг оси через кулисный камень, тем самым он побуждает кулису совершать качательное движение. Однако в это же время, если смотреть на движение кулисного камня относительно кулисы, то он будет совершать уже движение возвратно-поступательного типа. Такой вид устройства также часто используется в гидронасосах, которые обладают механизмами ротационного типа, с вращающимися лопастями. Кроме того, четырехзвенный механизм нашел свое применение и среди различных гидро- и пневмоприводов. В данном случае конструкция предполагает входной поршень на шатуне, который скользит во вращающемся или же качающемся цилиндре.
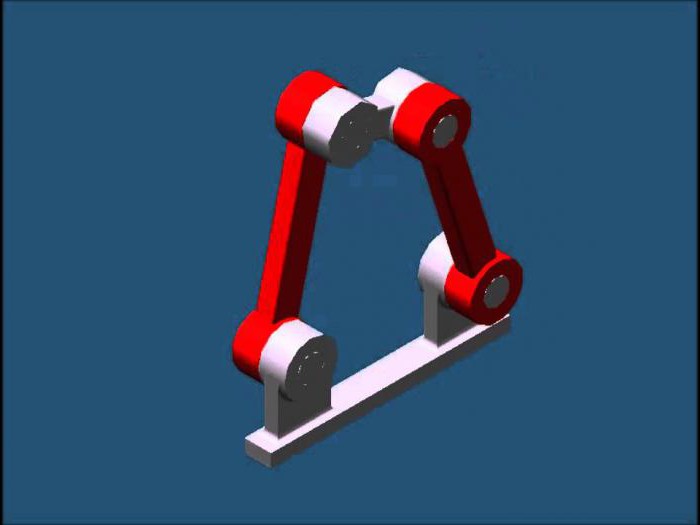
Кулисно-ползунный механизм
Данная модель механизма чаще всего применяется в лабораторных условиях, а также используется для обучения и ознакомления с этим устройством в условиях учебных лабораторий по таким дисциплинам, как прикладная и теоретическая механика.
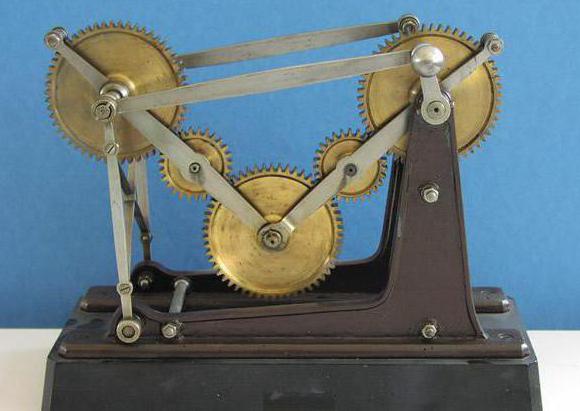
Стоит сказать о том, что распространенный довольно широко многозвенный кулисно-ползунный механизм обладает достаточно большими размерами. Это происходит из-за того, что конструкция второго шатуна с ползуном проходит ниже, чем прямолинейное расположение стержня кулисы. Такая конструктивная особенность говорит о том, что начало шатуна будет проходить ниже, чем непосредственно кулисно-рычажное устройство. Это, в свою очередь, говорит о том, что такой механизм должен обладать высокой основой или станиной, а это значит, что необходимо будет затратить большее количество средств на его создание, так как лишний материал уходит на создание подобной станины. Стоит отметить, что именно этот фактор и считается наибольшей проблемой и главным недостатком всей системы в целом.
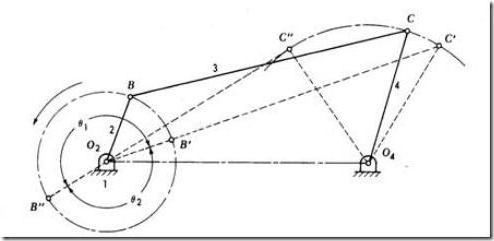
Кулисно-рычажное устройство
Кулисно-рычажный механизм — это изобретение, которое нашло свое применение в области машиностроения. Основной задачей данной системы является преобразование возвратно-поступательного движения в полноприводное вращательное. Цель, с которой изобретался этот механизм, состояла в том, чтобы повысить срок службы системы, а также поднять ее коэффициент полезного действия, или КПД. К тому же преследовались еще и такие цели, как расширение возможностей в области кинематики, за счет того, что система снабжалась второй кулисой, а также звенья системы выполнялись по-другому.
Кривошипно-кулисный механизм
После изобретения данной системы ее стали относить к шарнирно-рычажным механизмам, которые обладают гидроустройствами или пневмоустройствами, а целью их применения стала вентиляция на складах. Конструкция данного механизма довольно проста, и содержит она три основных элемента: это стойка, кривошип и кулиса. Задача, которая ставилась перед изобретателями данного устройства, — это улучшение надежности с одновременным упрощением в плане конструкции механизма. Прототипом для изобретения этой модели стали гидравлические или же пневматические механизмы, которые также использовали кулису с выполнением поступательного движения. Кроме того, в конструкцию входили также стойка, ползун, кривошип.
Ремонт
Как и любой другой механизм, кулисный также имеет свой срок службы. По истечении этого срока службы наступает время ремонта кулисного механизма. Однако случается и так, что устройство выходит из эксплуатации раньше положенного срока. Чаще всего в данном механизме изнашиваются или стираются такие его части, как кулиса, кулисный камень, зубчатое колесо, винты и гайки перемещения ползушки, а также сама ползушка с пальцем. Если поверхности пазов кулисы получили износ более чем на 0,3 мм, а также на них имеются глубокие задиры, то в качестве ремонта используют фрезерование с последующей операцией шабрения. Если износ не слишком сильный, можно обойти лишь шабрением, без фрезеровки.
Если изнашивается кулиса, то в качестве ремонта сначала приводят в порядок стенки паза. При проведении работ чаще всего ориентируются на те участки, которые изношены менее, чем другие.
Кривошипно-ползунный механизм: устройство, принцип работы, применение: принцип действия, анализ, применение
Кривошипно-ползунный механизм (КПМ) представляет собой частный случай рычажного устройства с четырьмя звеньями. Вращающаяся на валу часть — кривошип — шарнирно соединена с совершающей продольные движения частью- шатуном. Он зафиксирован в направляющих, оставляющих одну степень свободы для линейного движения. Устройство служит для преобразования вращения кривошипного звена в линейное перемещение ползуна. Механизм обратим, то есть и линейное движение ползуна может быть превращено во вращение вала кривошипа. Он широко используется в технике — в автомобильных моторах и паровых машинах, технологических установках и измерительных приборах.
Принцип действия кривошипно-ползунного механизма
Для прямой схемы кривошипно-ползунного механизма принцип работы состоит в следующем:
- ползун (как правило, соединенный с поршнем, который движется под давлением расширяющихся продуктов горения или пара) двигается линейно в сторону шатуна;
- поскольку шатун закреплен на некотором расстоянии от оси вращения, приложенная сила создает крутящий момент;
- он проворачивает кривошип.
В случае обратной схемы работы принцип таков:
- вращающийся кривошип создает силу, приложенную по касательной к его окружности, расстояние от центральной оси до шарнира и будет плечом рычага;
- через шарнирное сочленение эта сила вызывает линейное перемещение ползуна;
- ползун толкает поршень в такте сжатия (или другой исполнительный орган).
При построении кривошипно- ползунного механизма, его закона движения, статических и кинематических схем они должны удовлетворять требованиям по ГОСТ 2144-76.
Скачать ГОСТ 2144-76
Кинематический анализ кривошипно-ползунного механизма
Целью кинематического анализа КПМ является проектирование взаимных положений, траекторий передвижения, скоростей и ускорений всех его деталей. Для этого реальные физические тела заменяются моделями- рычагами и поверхностями, имеющими абсолютную жесткость, шарнирами и поверхностями с нулевым трением. Масса детали полагается сконцентрированной в условной точке- центре масс, как правило, совпадающей с геометрическим центром моделируемой детали.
Кинематическое моделирование разбивается на следующие основные этапы:
- выполнение общего плана положений. Строится для основных положений механизма, отражает взаимное расположение его частей в верхней и нижних мертвых точках;
- построение плана скоростей кривошипно-ползунного механизма, применяется графоаналитический способ на основе метода подобия;
- построение плана ускорений кривошипно-ползунного механизма, строятся эпюры как угловых, так и касательных ускорений;
- графическое моделирование моментов инерции;
- формирование графика энергии-массовых зависимостей.
При построении плана скоростей руководствуются следующими рекомендациями:
- Вектора, проходящие через полюс плана, представляют собой абсолютные скорости. Они всегда направлены от точки полюса, конец отрезка обозначается прописной буквой, аналогичной заглавной, обозначающей ту же точку на плане положений.
- Скоростные вектора, не касающиеся полюса, соответствуют относительным скоростям.
- Поскольку скорость является производной от перемещения, векторные изображения скоростей для каждой точки перпендикулярны соответствующим тем же точкам отрезкам, представляющим собой положение, и изображенными на плане положений.
- Неподвижным на плане положений точкам КПМ соответствуют вектора нулевой длины, расположенные в полюсе плана скоростей.
При построении плана скоростей возникает возможность стоить перпендикуляры и касательные к линии перемещения какой-либо точки кривошипно-ползунного механизма без изображения самой траектории.
Поскольку ускорение является производной от скорости, то векторные изображения ускорений для каждой точки перпендикулярны соответствующим тем же точкам векторам, изображенными на плане скоростей.
В ходе кинематического моделирования проводится также анализ на наличие избыточных связей в кривошипно-ползунном механизме. Под ними понимают связи, которые не добавляют степеней свободы и могут быть исключены из схемы без потери функциональности. Однако к удалению таких связей следует подходить осторожно. Например, дополнительные подшипники или опоры направляющих могут быть необходимы в реальном механизме исходя их больших величин перемещения во время рабочего хода. без них будет невозможно удовлетворить проектные требования по жесткости, прочности, температурной стойкости и т. д.
Статическое уравновешивание кривошипно-ползунного механизма
Во время перемещения звеньев механизма с изменяющимися скоростями (ускоренного движения) в них возникают инерционные силы и моменты. Их называют динамическими нагрузками. Такие нагрузки приводят к появлению вибраций, колеблющиеся детали излучают свои колебания в воздух, вызывая воздушный шум.
Динамические нагрузки приводят также к многократным деформациям деталей, их повышенному износу, накоплению усталости материала и преждевременному разрушению.
Шум и вибрация оказывают также негативное влияние на людей и точные механизмы, находящиеся рядом с источником. И, наконец, на возбуждение колебаний и излучение шума тратится энергия, это снижает КПД кривошипно-ползунного механизма.
Причины возникновения вибрации делятся на:
- силовые, колебания возмущаются периодическим приложением сил к объекту;
- кинематические, возмущение возникает за счет движения деталей;
- параметрические, возбуждение происходит за счет сил и моментов инерции.
Виброактивность делится на
- Внутреннюю, возникающую и распространяющуюся в пределах физических границ кривошипно-ползунного механизма. Она действует только на его детали и мало распространяется вовне.
- Внешнюю. Она действует на опоры механизма, его связи с другими частями общей конструкции, трансмиссию и далее. Основная причина, вызывающая такую виброактивность — неуравновешенность рычагов и звеньев.
Для устранения причин возникновения вибрации проводят статическое уравновешивание кривошипно-ползунного механизма. Механизм должен находиться в равновесии в состоянии покоя, при этом силы трения полагаются нулевыми.
Для этого вычисляют массы всех звеньев и строят график сил, действующих на них в состоянии покоя, прежде всего сил тяжести. Массы звеньев должны быть уравновешены с учетом длины рычагов (расстояния от центра вращения).
В ходе статического уравновешивания массы звеньев полагаются сосредоточенными в геометрическом центре звена.
Если общий центр масс системы совершает ускоренное движение, механизм считают неуравновешенным. Цель процедуры — достижение нулевого значения ускорения центра масс. Для этого к движущимся частям добавляют уравновешивающие массы, сводящие ускорение к нулю.
После статического уравновешивания наступает этап динамического уравновешивания кривошипно-ползунного механизма. При этом расчеты ведутся уже с учетом реальной пространственной конфигурации деталей.
В ходе производства реального изделия из-за дефектов материала, погрешностей отливки, механообработки и сборки возникают дополнительные разбалансировки звеньев. Для их устранения применяется балансировка кривошипно-ползунного механизма. Она заключается в:
- определении места дисбаланса с помощью средств вибродиагностики;
- передвижения и закрепления балансировочных грузов, предусмотренных конструкцией изделия;
- высверливание, выборка или наплавка необходимых масс материала в рассчитанных местах;
- повторной вибродиагностике.
Цикл операций повторяется до тех пор, пока подвижные части не будут удовлетворительно уравновешены.
Построение КПМ
Построение эффективно работающих кривошипно- ползунных устройств, несмотря кажущуюся простоту их конструкции, требует большой расчетной и конструкторской работы.
В ее ходе учитывают такие моменты, как:
- эффективность и коэффициент полезного действия;
- рациональное использование материалов, оптимальные весогабаритные характеристики;
- финансовые параметры производства и использования устройства;
- надежность и периодичность технического обслуживания;
- точность работы и виброактивность;
- безопасность и охрана труда.
Поскольку перечисленные аспекты взаимосвязаны и влияют друг на друга, проектирование ползунного четырехзвенного механизма представляет собой многоэтапный итеративный процесс. Зачатую конструктору приходится возвращаться на более ранний этап проектирования рычажного механизма и уточнять параметры схемы по результатам расчетов на более поздних стадиях процесса.
Иногда даже приходится менять вид кривошипно- ползунного механизма. В высокооборотных дизелях требуется снизить скорость движения поршня на некоторых фазах рабочего цикла. Как правило, это требуется при прохождении верхней части цилиндра, чтобы обеспечить более полное сгорание топливной смеси. Для этого применяют дезаксиальную схему кривошипно-ползунного устройства. В ней оси цилиндров расположены со смещением смещена относительно оси коленвала на некоторое расстояние по ходу вращения.
Для лучшего уравновешивания многоцилиндровых V-образных двигателей используют схему двигателя с прицепным шатуном.
В ней прицепного шатун бокового цилиндра сопряжен с шатуном главного цилиндра. Это позволяет снизить вес, размеры и момент инерции части подвижных звеньев.
Построение включает в себя такие расчетно- модельные процедуры, как:
- кинематический расчет, оптимизация числа кинематических пар;
- силовое моделирование;
- статический расчет, включая уравновешивание.
Обязательным этапом является проверка на соответствие нормам безопасности и охраны труда.
Традиционный расчет и построение такого сложного механизма, как кривошипный, представляет собой трудоемкий процесс, требующий от конструктора внимательности и достаточного опыта. Современные элементы программных продуктов семейства CAD — CAE позволяют избавиться от большей части рутинных и однообразных ручных операций, графических построений и расчетов. Конструктору достаточно выбрать из библиотеки трехмерную модель того или иного типа кривошипно- ползунной пары и провести параметрическое моделирование, задав необходимые размеры. Модуль графической симуляции проведет и статическое уравновешивание, и кинематический расчет, и выдаст рекомендации по оптимизации звеньев.
Область применения
Кривошипно-ползунные механизмы впервые стали применять в античности, на римских пильных мельницах. Там вращение колеса, приводимого в действие силой падающей воды, преобразовывалась в возвратно-поступательное движение полотна пилы.
В средние века конструкция была незначительно улучшена. Настоящий расцвет кривошипно-ползунные пары пережили в эпоху паровых машин. Детали стали производить из чугуна и стали, возросла их прочность и надежность. Учены стали разрабатывать методы расчета таких устройств.
В наши дни самым широким полем применения являются поршневые бензиновые и дизельные двигатели. Они используются в каждом автомобиле, тепловозе, большинстве судов, винтовых самолетах и вертолетах. В крупных судовых дизелях применяют как обычную, так и дезаксиальную схему.
Еще одна область использования-поршневые компрессоры для производства сжатого воздуха и других газов. В них используется обратная схема действия кривошипно-шатунной пары.
Такая же схема применяется и в конструкции горизонтально-ковочных установок.
Используются кривошипно-шатунные пары и в разнообразных гидравлических и пневматических инструментах и станках.
Если вы нашли ошибку, пожалуйста, выделите фрагмент текста и нажмите Ctrl+Enter.
Тема 1.3. Кривошипно-шатунный и газораспределительный механизмы
Кривошипно-шатунный механизм предназначен для восприятия давления газов и преобразования прямолинейного возвратно-поступательного движения поршня во вращательное движение коленчатого вала.
Механизм состоит из неподвижных и подвижных деталей. К подвижным деталям относятся: блок цилиндров, гильзы цилиндров, головка блока цилиндров, к неподвижным – поршень в сборе, шатун, коленчатый вал и маховик.
Блок цилиндров составляет одно целое с верхней частью картера и служит основанием для крепления всех основных деталей и агрегатов, обслуживающих двигатель. Он отлит из чугуна (может быть и силуминовый). Когда блок выполнен с верхней частью картера, эту конструкцию называют блок-картером.
Блок цилиндров имеет обработанные посадочные отверстия для гильз цилиндров, а на поверхностях, сопрягаемых с головкой блока, имеются отверстия для подачи охлаждающей жидкости из водяной рубашки в головки блока цилиндров.
Нижняя внутренняя часть блока цилиндров разделена поперечными перегородками на отсеки, в каждом из которых расположено по цилиндру. В нижней части блока с наружной стороны имеются водораспределительные каналы, а с внутренней стороны – камеры штанг толкателей. В блоке просверлены каналы для прохода масла.
Поперечные вертикальные перегородки внутри блока цилиндров совместно с передней и задней стенками картера двигателя обеспечивают необходимые прочность и жёсткость блока цилиндров. В этих перегородках, а также в передней и задней стенках картера, растачивают гнёзда под верхние половины коренных подшипников коленчатого вала, нижние половины которых помещаются в специальных крышках, крепящихся к блоку цилиндров болтами.
Гильзы цилиндров обычно мокрого типа, они отлиты из специального модифицированного чугуна, обладающего повышенной прочностью и износостойкостью или из сталей марок 35ХМЮ, 35ХМЮА и др. С целью повышения износостойкости втулок используют азотированные стальные втулки. Мокрые – снаружи омываются охлаждающей жидкостью, в отличие от сухих, которые устанавливаются в специальные отверстия в блоке и с охлаждающейся жидкостью не соприкасаются.
Головка блока цилиндров вместе с днищем поршня и стенками цилиндров образует камеру сгорания. Конструкция головки блока цилиндра зависит от формы камеры сгорания, числа и расположения клапанов, форсунок или свечей зажигания, впускных и выпускных каналов, системы охлаждения.
Головка отливается из чугуна или алюминия. В верхнюю часть запрессованы направляющие втулки клапанов. Головка крепится шпильками. В нижней части головки имеются отверстия для запрессовки сёдел клапанов. На верхней плоскости головки размещены клапаны с пружинами, коромысла клапанов со стойками, а также латунные стаканы под форсунки для дизельных двигателей. Сверху головка закрыта стальной штампованной крышкой. Уплотнение обеспечивается прокладками.
Поршень представляет собой металлический стакан, установленный в цилиндре с некоторым зазором. Верхняя, усиленная часть поршня, воспринимающая давление газов, называется головкой, а нижняя, направляющая часть, – тронком или юбкой. Приливы в стенках тронка, служащие для установки поршневого пальца, называются бобышками.
Поршни бензиновых двигателей изготавливают из алюминиевых сплавов, а дизельных – из чугуна или стали. Поршни бывают сплошные и составные.
В бензиновых двигателях головка поршня имеет плоское днище и толстые стенки с внутренними рёбрами, повышающими её прочность и обеспечивающими хороший отвод тепла. В дизелях конструкции головок поршней весьма разнообразны и зависят от типа дизеля и системы смесеобразования. В головке на боковой наружной поверхности имеются канавки для установки поршневых колец.
Для улучшения приработки поршней в цилиндрах и для уменьшения износа на тронк поршня наносят специальные покрытия. Обычно трущуюся поверхность тронка лудят – покрывают очень тонким слоем олова (толщиной 0,004…0,006 мм). В средней части тронка делают приливы-бобышки с отверстиями для установки поршневого пальца.
Для того чтобы при нагревании поршень мог бы расширяться без заедания в цилиндре, поршень устанавливают с зазором между стенкой цилиндра и тронком. Чтобы в холодном двигателе зазор между поршнем и цилиндром не был чрезмерно большим, что может вызвать стуки поршня и прорыв газов из цилиндра, в алюминиевых поршнях применяют пружинящие разрезные тронки. При боковом разрезе по всей длине тронк несколько пружинит, и поршень вставляется в цилиндр холодного двигателя плотно, с малым зазором. При нагревании поршня разрез даёт возможность тронку расширяться без заедания поршня в цилиндре. Применяют также поршни с частичным, несквозным разрезом Т – или П — образной формы, что повышает жёсткость тронка.
Для уменьшения бокового зазора сечение тронка делают не круглой, а овальной формы. Величина овальности равна примерно 0,15…0,29 мм. Поршень устанавливают в цилиндре холодного двигателя с минимальным зазором по большой оси овала тронка, располагаемой в плоскости качания шатуна, где действуют боковые силы, прижимающие поршень к стенкам цилиндра.
Поршневые кольца устанавливаемые в поршне, разделяются на компрессионные и маслосъёмные (рис. 3).
Рис.3. Поршневые кольца и эпюра давления
Компрессионные кольца уплотняют поршень в цилиндре и служат для предотвращения прорыва газов через зазор между тронком поршня и стенкой цилиндра. Маслосъёмные снимают излишки масла со стенок цилиндров, препятствуя проникновению его в камеру сгорания.
Компрессионные кольца устанавливают в верхние канавки на головке поршня (два-три кольца). Верхнее уплотнительное кольцо работает в очень тяжёлых условиях (нагрев от стенок головки, трения и соприкосновения с горячими газами), поэтому сложно обеспечить надлежащую смазку. Уплотняющее действие достигается благодаря прижатию к зеркалу цилиндра и лабиринтному действию уплотнения, которое обеспечивается путем перетекания газа через зазоры под кольцами в заколечные полости поршневых колец. Маслосъёмные кольца (одно или два) располагают под компрессионными кольцами на головке или одно кольцо размещают внизу на тронке.
Компрессионные кольца изготавливают из чугуна путём их индивидуальной отливки и последующей обработки. На кольце делают вырез, называемый замок, и позволяющий кольцу пружинить. Замки бывают прямые, косые и составные.
Для увеличения плотности прилегания кольца к стенке цилиндра его изготовляют таким образом, что в свободном состоянии форма кольца отклоняется от окружности, вследствие чего при сжатии его и установке в цилиндр обеспечивается правильное распределение давления кольца на стенку цилиндра по всей окружности.
Для улучшения условий работы компрессионные кольца, работающие в наиболее тяжёлых условиях, обычно покрывают пористым хромом (общая толщина покрытия 0,10…0,15 мм, толщина слоя пористого хрома
0,04…0,06 мм). Хромированная поверхность износоустойчива, а пористый слой хрома хорошо удерживает в себе смазку.
Маслосъёмные кольца для улучшения прилегания к зеркалу цилиндра имеют расширитель (осевой 4 и радиальный 5). Оба расширителя представляют собой стальные гофрированные пружинящие кольца. Рабочая поверхность покрыта хромом. Для удаления масла, скапливающегося под кольцами, предусмотрены прорези или сверления в самих кольцах, а также радиальные отверстия в стенке направляющей поршня.
Маслосъёмные кольца изготавливаются из чугуна. Кроме чугунных применяют стальные составные кольца.
Поршневой палец предназначен для шарнирного соединения поршня с шатуном. Палец, представляющий собой короткую стальную трубку, которая проходит через верхнюю головку шатуна и концами лежит в бобышках поршня. При работе двигателя на палец действуют силы, стремящиеся его изогнуть; поверхность пальца подвергается износу в верхней головке шатуна и в бобышках поршня. Палец изготавливается из мягкой углеродистой стали и подвергается термической обработке (цементации или закаливанию).
Шатун служит для передачи действующего на поршень усилия от давления газов на шейку кривошипа коленчатого вала.
Шатун
состоит из стержня, верхней и нижней
головок, вкладышей и шатунных болтов.
Требования к шатуну: обеспечение
необходимой прочности и надёжности
конструкции в целом, а также работоспособность
верхней и нижней головок. Основной
конструктивной характеристикой является
отношение ,
где
— радиус кривошипа,
— длина шатуна. Снижение
уменьшает нормальное давление поршня
на стенку цилиндра, однако приводит к
увеличению длины шатуна.
Шатун изготавливают из высококачественной стали 35, 45, 40ХН, 40Х и др. Стержень шатуна имеет двутавровое сечение. В случае принудительной смазки поршневого пальца в стержне шатуна высверливают отверстие. Верхняя головка шатуна предназначена для установки поршневого пальца. При плавающем пальце головку изготавливают цельной и в неё запрессовывают одну или две втулки из оловянистой бронзы. Для смазки трущейся поверхности в головке и втулках сделаны отверстия.
Нижняя головка шатуна служит для соединения его с шатунной шейкой коленчатого вала. Для возможности сборки с валом нижнюю головку шатуна делают разъёмной. В нижнюю головку шатуна устанавливают шатунный подшипник, выполненный в виде двух тонкостенных вкладышей, залитых антифрикционным сплавом: оловянисто-алюминиевым, баббитом, свинцовистой бронзой. От проворачивания и сдвига вкладыши фиксируются в головке шатуна отогнутыми усиками, входящими в соответствующие пазы головки.
Основание вкладышей изготовляют из малоуглеродистой стальной ленты толщиной 1…2 мм, на которую наплавляют тонкий слой баббита толщиной 0,2…0,4 мм. Наибольшее применение имеет баббит на свинцовой основе с добавлением примесей, повышающих его качества. Так, широко применяется баббит марки СОС-6-6, содержащий 5,5…6,5% сурьмы, 5,5…6,5% олова, остальное − свинец. Такие вкладыши получили название биметаллических. В целях дальнейшего повышения долговечности подшипников в последние годы стали применять триметаллические тонкостенные вкладыши. В них между стальным основанием и наружным слоем баббита имеется металлокерамический подслой.
Стальные вкладыши у дизелей заливают свинцовистой бронзой, выдерживающей без разрушения большие нагрузки, чем баббит. Применяют также сталеалюминиевые вкладыши, изготовленные из биметаллической ленты.
Коленчатый вал воспринимает усилия от поршней шатунами и преобразует в крутящий момент. Имеет коренные и шатунные шейки, щеки, соединяющие их, противовесы (если они есть), фланец для крепления маховика, носок, на котором установлен храповик для завода рукояткой, распределительная шестерня и шкив привода вентилятора и водяного насоса.
Коленчатые валы являются наиболее ответственными, напряжёнными и трудоёмкими в изготовлении деталей двигателей. Вал воспринимает нагрузки от давления газов, сил инерции поступательно-движущихся и вращательных масс, вызывающие значительные знакопеременные скручивающие и изгибающие моменты. Периодически изменяющийся крутящий момент при определённых условиях может вызвать крутильные и продольные колебания вала, которые приводят к появлению дополнительных напряжений.
Коленчатые валы изготовляют цельными, составными и полусоставными. Коренные и шатунные шейки имеют одинаковый диаметр.
Газораспределительный механизм состоит из следующих деталей: распределительного вала, толкателей, штанги, коромысла, клапанов и распределительных шестерён. Распределительный вал обеспечивает своевременное открытие и закрытие впускных и выпускных клапанов. Материалами служат стали 15, 25, 35, 15ХА и др. или чугун. Втулки опорных шеек изготавливают из стали, покрытой свинцовистым баббитом.
На распределительном валу расположены кулачки, шестерни привода масляного насоса и прерывателя-распределителя, эксцентрик привода топливного насоса. Распределительный вал получает вращение от коленчатого вала.
В четырёхтактных двигателях распределительный вал вращается в два раза медленнее коленчатого вала, а в двухтактном число оборотов одинаковое. Привод может быть либо шестерёнчатым, либо цепным. Для уменьшения шума шестерни привода изготавливают косозубыми.
Толкатели предназначены для передачи усилия от кулачков к штангам. Они изготовляются из стали, торцы для уменьшения изнашиваемости делают сферическим (или ролики) и наплавляют отбелённым чугуном.
Штанга передаёт усилие от толкателей к коромыслам и изготавливается либо из дюралюминиевого прутка, либо стали, имеет трубчатое сечение и на концах стальные наконечники. С одной стороны штанга упирается в толкатель, а с другой – в сферическую поверхность регулировочного винта, ввёрнутого в коромысло.
Коромысло передаёт усилие от штанги клапану. Коромысло изготавливают из стали или чугуна и устанавливают в бронзовую втулку на полую ось. Плечи коромысла неодинаковые – со стороны клапана длиннее. Этим уменьшается высота подъёма толкателя и штанги. В короткое плечо коромысла ввёрнут винт для регулировки теплового зазора.
Клапаны открывают и закрывают впускные и выпускные каналы. Клапан состоит из тарельчатой головки и стержня. Для улучшения наполнения диаметр головки впускного клапана изготовляют больше, чем выпускного.
Изготавливают клапаны из легированных жаропрочных сталей. Переход от тарелки к стержню сделан с большой галтелью, из-за возникающих в этом месте больших температурных напряжений. Форма тарелок клапана определяет его жёсткость и аэродинамичность. Плоская форма, тюльпанообразная − для впускных, выпуклая − для выпускных. Есть клапаны с внутренним охлаждением. При значительных массах целесообразно переходить на две пружины.
Сёдла клапанов для упрощения делают вставными. Материалом может служить жаропрочный чугун. Сёдла запрессовывают в выточки головки цилиндров. С целью повышения износостойкости и коррозионностойкости клапана опорную фаску тарелки, а иногда и фаску клапанного седла, покрывают стеллитом.