Сайлентблок википедия: HTTP status 402 — payment required, требуется оплата – Сайлентблок Википедия
- 01.10.2020
Сайлентблок Википедия
Возможные деформации резинометаллического шарнира Резинометаллические шарниры на легковом автомобиле Nissan Avenir:1 — задний резинометаллический шарнир
2 — передний резинометаллический шарнир
3 — поперечный рычаг передней подвески
4 — крепление шаровой опоры
5 — коробка передач
6 — вал привода левого переднего колеса (с ШРУСами) Резинометаллические шарниры: слева — неразборные, т. н. «сайлентблоки» (на верхнем фото — передний 2), справа — резиновые втулки разборных (на верхнем фото — задний 1).
Резинометаллический шарнир (РМШ) , так же иногда называется «сайлентблок» (en: silent block) — деталь машин и механизмов, разновидность шарнира, в котором подвижность обеспечивается за счёт эластичности резины, без трения, что позволяет устранить операции обслуживания и смазывания, увеличить срок службы узла, а также снизить уровень передаваемых через шарнир вибраций, что позволяет использовать РМШ в качестве виброизоляторов. В некоторых случаях резинометаллические шарниры компенсируют допуски изготовления и монтажа других конструкционных элементов, позволяя снизить их себестоимость и упростив сборку и/или ремонт узла.
Резинометаллические шарниры гасят или изолируют радиальные, осевые, торсионные и карданные колебания. Применяются при радиальных усилиях до 300 кН.
Различают резинометаллические шарниры, работающие преимущественно на кручение (с наружной обоймой, с внутренней обоймой, двухобойменные, эксцентричные), и работающие на сжатие с изгибом (опоры, подушки).
Примером РМШ первого типа являются шарниры подвески автомобиля, обеспечивающие подвижность рычагов и рессор, или гусениц, обеспечивающие подвижность траков. Примером РМШ второго типа являются подушки подвески двигателя, обеспечивающие его подвижность в заданных пределах и при этом гасящие возникающие при его работе вибрации, не давая им передаваться на раму или кузов автомобиля.
С технологической точки зрения различают также разборные резинометаллические шарниры, у которых металлическая обойма и сменная резиновая втулка (иногда с металлической внутренней распорной втулкой) представляют собой отдельные детали, взаимное прокручивание которых исключается за счёт радиального сжатия посаженной внатяг резиновой втулки, и неразборные резинометаллические шарниры (так называемые сайлентблоки — от англ. silent block), у которых металлические внутренняя и наружная втулки неразборно соединены друг с другом при помощи завулканизированного между ними слоя эластомера, как правило резины. Каждый из типов имеет свои преимущества и недостатки. Так, разборные резинометаллические шарниры более дёшевы, а также обходятся дешевле в ремонте, в процессе которого заменяется только резиновая втулка, а не весь шарнир в сборе. При этом они способны передавать меньшие усилия, чем неразборные шарниры, причём их характеристики сильно варьируют в зависимости от качества запрессовки резиновой втулки. Неразборные шарниры более технологичны в замене (при наличии специального оборудования), а заводская сборка обеспечивает им высокое постоянство характеристик.
Главным свойством резинометаллического шарнира является отсутствие взаимного проскальзывания между резиновыми и металлическими деталями, благодаря чему между ними при нагрузке не возникает силы трения, которая может являться причиной ускоренного износа слоя эластомера. При этом слой эластомера поглощает и рассеивает воспринимаемые колебания (удары, знакопеременные деформации) за счёт свойства эластичной деформации внутренних связей эластомера. Способность к гашению вибраций определяется типом и твёрдостью эластомера.
Наилучшими физическими свойствами для изоляции и гашения вибраций обладают эластомеры на основе натурального (природного) каучука (NR). В последнее время некоторое распространение получили также альтернативные гибридные эластомеры — полиуретаны и смеси каучука и полиуретана, однако их недостатком является сложность обеспечения отсутствия проскальзывания при работе из-за неподходящих характеристик большинства сортов полиуретана и его плохой адгезии к металлическим втулкам. Если при работе шарнира возникает характерный скрип или писк — это является признаком либо неправильной сборки, при которой эластичная часть шарнира не получила достаточного обжатия, либо отрыва слоя эластометра от втулки из-за недостаточной адгезии к металлу и/или превышения допустимых нагрузок, либо использования производителем неподходящего сорта эластомера.
Виброизоляция — Википедия
Виброизоляция (англ. vibration-isolation, vibration control) — это способность препятствия (виброизолятора, виброопоры) изолировать конструкцию (оборудование, механизм и т. п.) от распространяющейся по ней вибрации
Оборудование и механизмы имеют связь с окружающими объектами (опора — опорная связь; трубопровод, кабель — неопорная связь). Виброизоляция является результатом действия двух процессов внутри препятствия — гашения и изоляции колебаний, которые обусловлены физическими свойствами материала препятствий, а также конструктивными особенностями самого препятствия.
Различают пассивную виброизоляцию, когда такой источник дополнительной энергии не применяют и активную виброизоляцию, когда используют энергию дополнительного источника[2].
Гашение и изоляция колебаний[править | править код]
Демонстрация поведения эластомерных материалов с различным соотношением свойств изоляции и гашения колебанийВ системе, состоящей из массы и пружины, и в которой происходит равномерное или с ускорением движение массы, возникают колебания. Функцию пружины могут выполнять корпус, опора или рама транспортного средства. Колебания массы могут создавать шум и вибрацию, распространяемые по воздуху или через жесткие связи. Шум и вибрация, как правило, являются источниками дискомфорта и ускоряют процессы износа деталей машин и механизмов. Поэтому в технике принято бороться с шумом и вибрацией.
Любой материал, помимо основных характеристик, обладает свойствами гашения (демпфирования) или изоляции (снижения амплитуды, отражения) колебаний. К примеру, камень обладает 100 % демпфирующими свойствами и 0 % свойствами изоляции колебаний.
Изоляция колебаний в колеблющейся системе обеспечивает плавное и комфортное снижение амплитуды колебаний, а гашение колебаний обеспечивает поглощение энергии колебаний. К примеру, стойка подвески легкового автомобиля состоит из пружины и амортизатора. В данном случае пружина выполняет функцию изолятора, а амортизатор — гасителя колебаний.
Виброизоляция опорной связи[править | править код]
Виброизоляция опорной связи реализована в устройстве, называемом виброизолятор (виброопора). На иллюстрации представлена зависимость перепада уровней вибрации (передаточная функция), которая измеряется до и после виброизолятора в широком диапазоне частот.
Виброизолятор[править | править код]
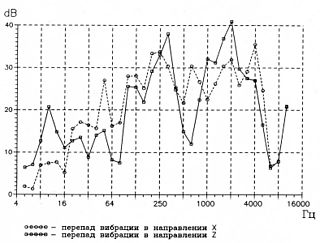
Виброизолятор (англ. vibration-isolator, antivibration part) — виброизолирующее устройство для отражения и поглощения волн колебательной энергии, распространяющихся от работающего механизма или электрооборудования, за счет использования эффекта виброизоляции. Устанавливается между телом, передающим колебания, и телом защищаемым (например, между механизмом и фундаментом). На иллюстрации представлено изображение виброизоляторов серии «ВИ», которые применяются в судостроении России, например, на подводной лодке «Санкт-Петербург». Показаны «ВИ» с допускаемыми нагрузками 5, 40 и 300 кг. Они отличаются размерами, но имеют подобную конструкцию. В конструкции использована резиновая оболочка, которая армирована пружиной. Резина и пружина прочно соединены в процессе превращения сырого каучука в резину методом вулканизации. Под действием весовой нагрузки механизма оболочка деформируется, причем витки пружины сжимаются или раздвигаются. При этом в поперечном сечении пруток пружины, скручиваясь, взаимодействует с материалом оболочки, вызывая в ней деформации сдвига. Известно, что виброизоляция в принципе не может осуществляться без наличия вибропоглощения. А величина деформации сдвига в упругом материале виброизолятора является определяющей для оценки эффективности вибропоглощения. При действии вибрации или ударных нагрузок деформации увеличиваются, являясь при этом циклическими, что значительно усиливает эффективность данного устройства. В верхней части конструкции предусмотрена втулка, а в нижней фланец, с помощью которых виброизолятор крепится к механизму и фундаменту.
Технические задачи для виброизоляторов[править | править код]
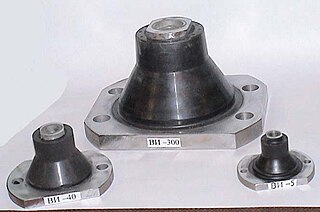
- Снижение структурных шумов и вибраций, то есть распространяемых от источника по жестким связям (например, по раме транспортного средства).
- Компенсация перекосов и деформаций при монтаже и эксплуатации.
- Замена трения скольжения в шарнире на эластичную деформацию внутренних связей резинового слоя виброизолятора.
- Демпфирование колебаний, ударов.
- Предотвращение резонанса.
- Являться частью кинематической схемы механизма, совершающего периодические колебания.
Некоторые виды виброизоляторов[править | править код]
- Резинометаллические опоры (коническая, круглая, плоская, клиновидная, сферическая, приборная, бочкообразная, и др).
- Резинометаллические пружины (коническая, плоская, многослойная, шевронная и др).
- Гидроопоры, гидровтулки, гидроопоры HALL с переменной жесткостью.
- Сайлентблоки, обрезиненные втулки.
- Вспомогательные опоры (прорезиненные упорные шайбы).
- Резинометаллические упоры и буферы.
- Резинометаллические опоры трубопроводов.
- Детали машин и механизмов с функцией виброизоляции (например, звездочка или зубчатое колесо с промежуточным слоем резины между венцом и втулкой, рычаги и др).
Причины разнообразия конструктивных схем виброизоляторов[править | править код]
- Требования по компоновке виброизоляторов в составе машины или механизма.
- Действующие нагрузки на виброопору.
- Требуемая степень виброизоляции в системе координат.
- Требования по жесткости, а также соотношение жесткостей виброопоры в системе координат.
- Значения допустимых деформаций в системе координат, если виброизолятор является элементом кинематической схемы механизма.
- Требования по допустимой эластичной деформации для обеспечения компенсаторной способности виброизолятора.
- Условия эксплуатации и окружающей среды.
Примеры использования виброизоляторов[править | править код]
- — крепление двигателя внутреннего сгорания и кабины к раме транспортного средства;
- — крепление деталей подвески автомобиля (амортизатор, рычаг и др).
- — соединение моста трактора с рамой;
- — крепление узлов и агрегатов ветроэнергетической установки к гондоле;
- — установка машин и механизмов на основание посредством виброизоляторов;
- — крепление чувствительных к тряске и вибрации приборов к основанию;
- — торсионные шарниры;
- — крепление буксового узла к раме железнодорожной тележки;
- — крепление железнодорожного вагона к раме тележки;
- — шарниры в сложных пространственных механизмах и др.
Физические принципы, позволяющие виброизолятору максимально эффективно выполнять свою функцию[править | править код]
- Отсутствие трения скольжения в соединении эластомера с металлом. В данном случае необходима связь эластомера с металлом посредством вулканизации.
- Применяемый эластомер должен обладать свойством поглощать энергию вибрации не разрушаясь при этом.
Виброизоляция неопорной связи[править | править код]
Виброизоляция неопорной связи (трубопровод) реализована в устройстве, называемом виброизолирующий патрубок .
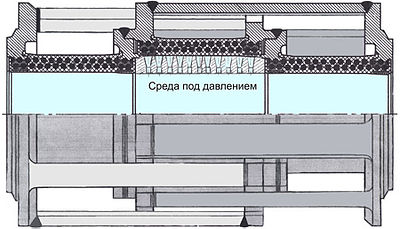
Виброизолирующий патрубок[править | править код]
Виброизолирующий патрубок — часть трубы с упругими стенками для отражения и поглощения волн колебательной энергии, распространяющихся от работающего насоса по стенке трубопровода. Устанавливается между насосом и трубопроводом. На иллюстрации представлено изображение виброизолирующего патрубка серии «ВИПБ». В конструкции патрубка использована резиновая оболочка, которая армирована пружиной. Свойства оболочки подобны оболочке виброизолятора. Имеет устройство, которое обеспечивает безраспорность от сил внутреннего давления среды в трубопроводе.
Системы активной виброизоляции содержат, кроме пружины, цепь обратной связи, которая состоит из датчика, например — пьезоэлектрического акселерометра или геофона, контроллера и привода. Показания акселерометра (вибрации) обрабатываются схемой управления и усиливаются. Затем сигнал подается на электромагнитный привод. В результате такое подавление вибраций дает лучший результат, чем обычное демпирование.
Датчики[править | править код]
- Пьезоэлектрические акселерометры и датчики силы
- МЭМС акселерометры
- Геофоны
- Датчики расстояния
- Интерферометры
Приводы для активной изоляции[править | править код]
- Линейные двигатели
- Пневматические приводы
- Пьезоэлектрические двигатели
- ↑ А.Колесников «Шум и вибрация». Ленинград. «Судостроение». 1988
- ↑ 1 2 Гусев Ю. И., Карасев И. Н., Кольман-Иванов Э. Э. Конструирование и расчет машин химических производств. — М., Машиностроение, 1985. — С. 92 — 95
Сайлентблок: виды, диагностика и замена
Содержание
1. Назначение и виды сайлентблоков2. Конструктивные особенности подвески разных авто3. Диагностика неисправности4. Выбор нового изделия5. Порядок проведения заменыРегламент проведения технического обслуживания, как правило, содержит только общую информацию по осуществлению отдельных сервисных операций. В частности, для ходовой части предписана лишь контрольная проверка некоторых узлов. На практике нарушение функций подвески редко происходит внезапно. Более характерен постепенный нарастающий износ.
Назначение и виды сайлентблоков
В конструкции подвески автомобиля выделяется несколько ключевых элементов, соединенных друг с другом:
- Продольные и поперечные рычаги. Позволяют обеспечить подвижное крепление колеса к несущему кузову авто.
- Пружины и амортизаторы. Поглощают большую часть энергии и гасят передаваемые колебания на кузов автомобиля.
- Стабилизаторы. Предотвращают раскачку авто в поперечной плоскости.
Для соединения отдельных деталей между собой, а также к кузову используют составной элемент, известный как сайлентблок. Помимо соединения деталей подвески, шарнир служит для гашения колебаний между запчастями, предотвращая передачу вибрации на кузов. Именно поэтому многорычажная конструкция, или подвеска, которая расположена на подрамнике, отличается низкой вибрационной нагруженностью для пассажиров. Высокая плавность хода обеспечивает достойный комфорт в дальней дороге.
По конструктивному исполнению шарнир представляет собой составное резинометаллическое изделие, включающее:
- Металлические элементы. Внешнюю деталь называют обоймой, а внутренний элемент относится к втулке.
- Упругий элемент. Является проставкой между двумя металлическими частями и изготавливается из специальной упругой резины или может быть полиуретановым.
Среди разновидностей сайлентблоков выделяются образцы, где отсутствует внешняя обойма, роль которой выполняет посадочное место на детали или кузове машины. Упругие элементы также находятся в конструкции рулевого управления, но имеют слегка измененные задачи.
Конструктивные особенности подвески разных авто
В зависимости от конструктивного исполнения подвески, меняется и число шарнирных соединений на передней и задней оси. Даже в ходовой части бюджетного автомобиля удастся отыскать несколько сайлентблоков:
- на поперечных рычагах крепления колес;
- в местах крепления поперечного стабилизатора;
- в точке крепления амортизационной стойки внизу;
- в районах крепления продольных реактивных тяг и подрамника (при наличии).
Общее количество превышает десять единиц. Если в автомобиле аналогичные шарниры задействуют и для крепления силового агрегата, то показатель будет еще выше.
Не составит труда установить количество резиновых элементов и в кормовой части. Для не самой сложной подвески торсионного типа сайлентблок задней балки применяется четыре раза. В более серьезных многорычажных подвесках число упругих элементов колеблется от 8–10 штук на одной стороне и выше.
Диагностика неисправности
Разрушение подвижного шарнира не происходит внезапно. Усталостный износ упругой части начинается с появления микротрещин с последующим растрескиванием или отслоением упругого материала. В качестве разрушителей выступают:
- температурные перепады;
- неровности дороги;
- агрессивное воздействие внешних веществ и влаги;
- временной фактор.
Не стоит ежедневно заглядывать под авто. Качественные изделия имеют ресурс не менее 100 тыс. км пробега. Контрольный осмотр проводят обычно при каждом втором визите на станцию – через 30000 км – или с периодичностью раз в 2 года. В любом случае внепланово следует проверить подвеску при очевидных симптомах повреждения элемента:
- появлении скрипов и нехарактерных колебаний авто;
- дребезжащего или ударного стука при проезде неровностей;
- заметной поломке шарнира при визуальном осмотре автомобиля на подъемнике;
- неравномерности износа шин при отсутствии других отклонений – давление в колесе, соблюдение развала-схождения.
Если удалось распознать неисправность вовремя, не следует откладывать несложный ремонт. Предстоящая замена задних сайлентблоков илидеталей в передней частине является чрезвычайно сложной операцией. При определенных навыках такую работу проведет любой опытный автомобилист. Даже при обращении в сервис текущий ремонт не принесет больших финансовых затрат.
В то же время при нежелании поменять шарниры и дальнейшей их эксплуатации повышенная нагрузка ляжет на смежные элементы ходовой части. Особенно страдают шины, подшипники и амортизационные стойки. Расходы на обслуживание подвесной части автомобиля в комплексе окажутся несопоставимыми.
Выбор нового изделия
При выборе новых деталей владелец авто зачастую оказывается перед непростой задачей. Во-первых, определяющим фактором является вопрос стоимости. Во-вторых, выбрать предстоит среди образцов с различным материалом упругой части.
В ценовом сегменте разбежка достигает кратного размера. Конечно, оригинальный комплект установить в фирменном сервисе – надежное решение. Однако не каждому по карману заводские запасные части. Возможная экономия в последующем возникнет только за счет длительности эксплуатации качественных изделий в конструкции подвески. Стоит учитывать, что в некоторых случаях сайлентблоки отдельно не меняются. Это утверждение верно для дорогих автомобилей, к примеру, где в подвеске применяются легкосплавные рычаги и тяги.
При подборе аналога не стоит доверять сомнительным изделиям неизвестного производителя. Качественный аналог известного бренда имеет гарантию и хороший ресурс эксплуатации. В некоторых случаях замена оригинала на изделие другого производителя становится просто необходимой. Необычными конструкциями, где в составе сайлентблока удается встретить даже клапаны и гелевые наполнители, выделяются японские производители, например, Субару.
Среди возможных конкурентов по упругому материалу выделяют:
- шарнир с резиновой вставкой;
- изделие с полиуретановым элементом.
Частные компании чаще всего изготавливают аналоги с доступным и современным синтетическим материалом. Полиуретан обладает некоторыми преимуществами:
- Широкий рабочий температурный диапазон.
- Стабильность геометрических размеров.
- Устойчивость к механическим и химическим воздействиям.
Главная задача при выборе аналога — определение правильных размеров и идентификация запасной части. До приобретения обязательно следует уточнить каталожный номер детали и место установки. При самостоятельном поиске через каталог интернет-магазина не стоит отказываться от проверки выбора менеджером торговой точки. Если все параметры отвечают требованиям, то можно оплачивать заказ. При невозможности определить принадлежность изделия, допустимо использовать и способ обычного инструментального замера. В этом случае имеют значение отдельные габариты: наружный и внутренний диаметр, длина детали или втулки.
При покупке не стоит подвергать автомобиль дополнительному испытанию, заменяя только изношенную часть. Для подвески всегда требуется синхронная замена элементов с левой и правой стороны. К примеру, замена сайлентблоков передних рычагов в составе комплекта не потребует скорого повторного возврата в ремонтную мастерскую.
Порядок проведения замены
До начала ремонтных работ подготавливают комплект ключей и специальный съемник для сайлентблоков. Процесс самостоятельной замены для большинства автомобилей в общем виде выглядит следующим образом:
- Ослабляются крепежные болты колес одной оси.
- Автомобиль удобно расположить на подъемнике.
- Освобождается крепление соответствующего рычага или тяги. При необходимости их снимают с автомобиля.
- Проводится выпрессовка поврежденного элемента.
В случае затруднений при извлечении непригодной детали прибегают к примитивным способам. Старый материал попросту выжигают, после чего удаляют металлические части.
Для последующего монтажа тщательно очищается установочное гнездо. Поверхность нового изделия обрабатывают жирным раствором, избегая масел или других продуктов нефтепереработки. После запрессовки новых деталей проводят сборку в обратной последовательности по отношению к демонтажу.
Втулка — Вікіпедія
Матеріал з Вікіпедії — вільної енциклопедії.
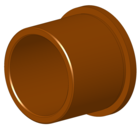
![]() |
Вту́лка[1], утулок (-лка)[2] — деталь машини, механізму, приладу циліндричної або конічної форми (з осьовою симетрією), що має осьовий отвір, у який входить сполучна деталь[1].
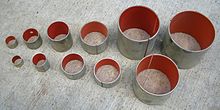
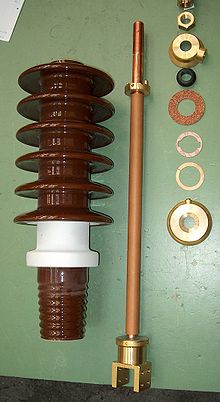
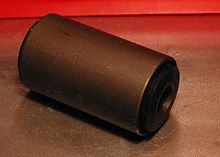
Залежно від призначення застосовують втулки підшипникові, перехідні, кріпильні, віброізоляційні, електроізоляційні, різьбові та ін.
За конструкцією втулки бувають суцільні і розрізні.
Втулки підшипникові[ред. | ред. код]
Втулка підшипникова (підшипник ковзання) — втулка, яка не містить проміжних рухомих елементів. Опора валу або інший елемент, що обертається розміщується в циліндричній втулці по посадці із зазором.
Підшипники ковзання поділяються на:
- сухі — періодично змащуються мастилом або не змащуються взагалі. Самі втулки або лише їх поверхні ковзання виконані з підшипникових металевих сплавів або з синтетичних матеріалів (наприклад: чавун, бронза, тефлон). Використовуються такі втулки у малонавантажених і менш відповідальних вузлах;
- повітряні — в яких зазор між валом і втулкою утримується через повітряну подушку, утворену стиснутим повітрям, що подається у втулку. Втулки цього типу застосовуються в прецизійному обладнанні, при малих радіальних навантаженнях валів;
- масляні — частина корпусу втулки наповнена маслом. Під час руху валу, між площею валу і втулкою утворюється тонкий шар масла (масляна плівка), якої достатньо для підтримання вала. Конструкції втулок залежать від типу підшипника ковзання, де вона застосовується. Розрізняють втулки гідродинамічних підшипників ковзання, де масляна плівка формується самостійно у результаті гідродинамічних ефектів, що виникають у щілині між втулкою і валом і гідростатичних підшипників, куди масло подається під тиском.
Втулки перехідні[ред. | ред. код]
Втулка перехідна — інструмент, який використовується на металообробному устаткуванні для встановлення інструменту з різними конусами Морзе.
Втулки кріпильні[ред. | ред. код]
Кріпильна втулка служить для закріплення внутрішніх кілець підшипників кочення та інших деталей на циліндричних ділянках валів і осей. Така втулка забезпечує точне розміщення деталей на валах і фіксує їх при затягуванні гайкою.
Втулки електроізоляційні[ред. | ред. код]
Електроізоляційна втулка використовується як компонент електричних пристроїв, що призначений для ізоляції провідників високої напруги, котрі проходять через металеві стінки корпусів. Такі втулки виготовляють з електроізоляційних матеріалів, таких як, полімери чи кераміка. Втулки встановлюються на електророзподільчих пристроях, трансформаторах, вимикачах та іншому обладнанні, що працює під високою напругою.
Віброізоляційні втулки[ред. | ред. код]
Віброізоляційна втулка — це гумова втулка, що використовується як ізолятор вібрацій. Вона реалізує сполучення між двома деталями із забезпеченням розсіювання енергії коливань, що передається. Застосовується у системах підвіски транспортних засобів, де втулка з гуми (або, частіше, синтетичного каучуку чи поліуретану) усуває безпосередній контакт двох металевих деталей, забезпечуючи при цьому певну свободу їх руху. Цей рух дозволяє підвісці вільно переміщатися, при русі по нерівностях, зводячи до мінімуму передачу шуму і вібрацій на шасі автомобіля. Такі втулки називають ще сайлентблоками.
Зброя[ред. | ред. код]
Втулка холодної зброї (списа, рогатини) — частина наконечника (зазвичай трубчаста), за допомогою якої його кріплять до держака.
- Анурьев В. И. Справочник конструктора-машиностроителя. В 3-х т.. — М.: Машиностроение., 2001. — ISBN 5-217-02962-5
Что такое сайлентблок и зачем его менять
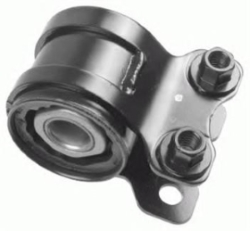
Сайлентблок – это мелкая деталь подвески автомобиля, которая представляет собой две металлические втулки, вставленные одна в другую, промежуток между которыми занимает резиновая вставка. Сайлентблоки служат для соединения деталей автомобильной подвески, они смягчают колебания, передающиеся от одной детали к другой при движении машины. Кроме подвески, резинометаллические шарниры (так часто называют сайлентблоки) устанавливаются и в другие системы автомобиля: двигатель, коробку передач, рычажные крепления, используются в стабилизаторах и амортизаторах и в других элементах.
При эксплуатации авто сайлентблоки испытывают огромные нагрузки, поэтому за их состоянием нужно следить, заменяя по необходимости изношенные сайлентблоки на новые. Желательно проверять состояние сайлентблоков каждые 50 тысяч километров пробега. Для определения состояния резинометаллических шарниров подвески нужно вывесить по очереди переднюю и заднюю части авто, проверить рычаги на предмет люфта и провести визуальный осмотр сайлентблоков. При этом внимательно осмотрите резиновую вкладку сайлентблока: если на ней появились трещины или отслоения, то сайлентблок подлежит обязательной замене.
Такая, казалось бы, незначительная деталь, как сайлентблок, влияет на работоспособность всей ходовой части автомобиля. Износ сайлентблока сказывается на управляемости автомобиля, ухудшая её, особенно при движении на высоких скоростях. Также изношенный сайлентблок может вызывать неприятные скрипы в подвеске, появление люфта и ощутимого крена машины. Если вовремя не заменить изношенный сайлентблок, могут деформироваться крепления рычагов, что впоследствии повлечёт за собой дорогостоящий ремонт.
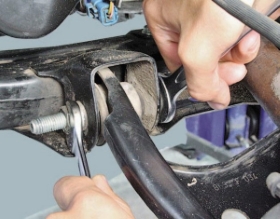
Не рекомендуется самостоятельно производить замену сайлентблоков, за этим надёжней будет обратиться в мастерскую к профессионалам. Для качественной установки требуется специальное оборудование и компетентные мастера, имеющие опыт подобной работы. В результате неграмотной замены сайлентблоков при эксплуатации могут возникнуть проблемы, и новый сайлентблок раньше времени выйдет из строя. Например, если при замене сайлентблоков подвески по незнанию полностью закрутить гайку оси рычага, когда автомобиль находится в подвешенном состоянии, то сайлентблок в скором времени выкрутится и придёт в негодность.
Менять на сервисе или самим – выбор за Вами, главное, чтобы такие важные детали как сайлентблоки были в порядке, и автомобиль держался на дороге уверенно, обеспечивая Вам безопасность в пути.