Состав электролита – Электролит Кислотный Для Аккумулятора, Состав и Плотность, Корректирующий Раствор Для Свинцового АКБ, Зарядка Батареи, Изготовление Своими Руками
- 09.03.2020
Приготовление электролита | Аккумуляторные батареи
Страница 14 из 26
4.3. Приготовление электролита для свинцовых аккумуляторов
Электролит для свинцовых аккумуляторов приготовляется путем разбавления чистой серной кислоты чистой водой. Кислота продается обычно концентрированной, удельного веса от 1,835 до 1,840. При разбавлении концентрированной кислоты раствор сильно нагревается. Во избежание опасности для лица, производящего смешивание, всегда необходимо наливать кислоту в воду, но не наоборот.
Хотя количество теплоты, развиваемой в обоих случаях, одно и то же, однако удельные теплоты воды и концентрированной кислоты совершенно различны. Струя воды, попадая в концентрированную кислоту, освобождает большое количество теплоты, которая благодаря низкой удельной теплоте кислоты вызывает сильное местное повышение температуры. Кислота, приливаемая к воде, не может вызвать столь же большого повышения температуры в силу того, что удельная теплота воды очень высока. Необходимо непрерывно перемешивать раствор все время, пока кислота подливается в воду, для того, чтобы помешать более тяжелой кислоте опуститься на дно сосуда, не смешавшись с водой.
Никакие другие металлические сосуды, кроме свинцовых, непригодны.
После разбавления кислоты, до заливки ее в батарею, необходимо подождать, пока она остынет, для того чтобы избежать повреждений пластин и сепараторов.
Охлаждение можно ускорить, пользуясь струей сжатого воздуха, но воздух при этом должен быть чистым.
Чтобы облегчить приготовление электролитов любой требуемой концентрации, на рис. 4.1 приведены необходимые пропорции кислоты и воды. Аккумуляторные заводы обычно сообщают сведения о том, какой крепости кислоту следует применять для каждой данной батареи.

Рис. 4.1. Приготовление электролита любого удельного веса из концентрированной кислоты удельного веса 1,835.
1- содержание серной кислоты, %; 2 – требующаяся добавка воды по объему; 3 – то же по весу.
4.4. Приготовление электролита для кадмиевоникелевых и железоникелевых аккумуляторов
Для кадмиевоникелевых и железоникелевых аккумуляторов в качестве электролита служит раствор в дистиллированной воде едкого калия (КОН) или едкого натрия (NaOH).
В зависимости от температуры окружающего воздуха в аккумуляторах (табл. 4.1) применяется раствор соответствующей плотности (концентрации) основного компонента электролита в чистом виде или с добавкой едкого лития (LiOH).
При температурах – 20…– 40°С при отсутствии чистого едкого калия допускается как исключение применять составной электролит из едкого калия и едкого лития повышенной плотности, при этом емкость аккумулятора снижается на 10 – 15%. При отсутствии составного электролита из едкого калия и едкого лития при температуре – 19…+35°С можно воспользоваться составным электролитом из едкого натрия повышенной плотности 1,17 – 1,19 г/см
Таблица 4.1.
Рекомендуемые состав и плотность электролита для кадмиевоникелевых и железоникелевых аккумуляторов при различной температуре окружающего воздуха
Температура воздуха, °С | Рекомендуемый состав электролита | Плотность, г/см3 |
– 19… +35 | Составной раствор едкого калия с добавкой на 1 л раствора 20 г едкого лития аккумуляторного (моногидрата лития) | 1,19 – 1,21 |
– 20… – 40 | Раствор едкого калия | 1,25 – 1,27 |
+10…+50 | Раствор едкого натрия с добавкой на 1 л раствора 15 – 20 г едкого лития (моногидрата лития) | 1,1 – 1,12 |
Не гарантируется также долговечность аккумуляторов при работе их с электролитом из раствора чистого едкого калия плотностью 1,19 – 1,21 г/см
Железоникелевые аккумуляторы рассчитаны на работу в тех же условиях и с тем же электролитом, что и кадмиевоникелевые, но они более чувствительны к низким температурам, поэтому могут применяться при температурах не ниже –20° С.
В процессе эксплуатации температурные условия в зависимости от времени года резко изменяются, поэтому для более эффективного использования емкости аккумуляторов их следует заливать электролитом, по составу и плотности соответствующим этим условиям.
В аккумуляторах, находящихся в эксплуатации, уровень электролита постепенно снижается вследствие испарения, поэтому его необходимо периодически измерять и при необходимости дополнять до нормы дистиллированной водой. Не реже чем через 10 циклов нужно проверять плотность электролита и также доводить ее до нормы добавлением раствора плотностью 1,41 г/см3 или дистиллированной воды.
Снижение уровня электролита ниже верхнего края пластин или сетки, а также повышение плотности электролита при положительных температурах окружающего воздуха снижают емкость и долговечность последних. Уровень электролита необходимо проверять и доводить до указанной нормы перед каждым зарядом. Он проверяется с помощью стеклянной трубки диаметром 5 – 6 мм с метками на высоте 5 и 12 мм от конца. Для установления уровня электролита в аккумуляторе надо конец трубки с метками ввести через заливное отверстие до упора в пластины или сетку, после чего другой конец трубки закрыть пальцем. Вынув трубку из аккумулятора по высоте столбика электролита в ней, определим уровень электролита над верхним краем пластин или сетки в аккумуляторе. Для снижения уровня электролита в аккумуляторе можно пользоваться пипеткой или резиновой грушей со стеклянным или пластмассовым наконечником длиной около 100 мм. Доливку электролита или дистиллированной воды в аккумуляторы можно производить с помощью пипетки, резиновой груши или кружки через стеклянную воронку, размеры которых подбирают в зависимости от вместимости аккумуляторов. Проверка плотности электролита производится при помощи сифонного ареометра.
Для приготовления электролита поставляются следующие исходные материалы:
а) едкий калий аккумуляторный марки А (твердый) или марки В (жидкий) и едкий литий аккумуляторный;
б) составная щелочь сорта А – готовая смесь едкого калия и едкого лития в отношении едкий литий/едкий калий = 0,04…0,045;
г) составная щелочь сорта Б – готовая смесь едкого натрия и едкого лития в соотношении едкий литий/едкий натрий = 0,028…0,032.
Перед приготовлением электролита необходимо удостовериться, что имеющиеся в наличии химические ‘компоненты соответствуют приведенным выше требованиям и ГОСТам. Хранить эти материалы необходимо в герметически закрытой таре. Данные материалы могут поставляться как в жидком, так и в твердом состоянии в виде гранул, чешуек, кусков или слитка.
Приготовление электролита следует начинать с определения потребности в нем согласно норме расхода на один аккумулятор при первой заливке, указанной в табл. 4.2.
Таблица 4.2
Ориентировочная норма расхода электролита на один аккумулятор при первой заливке
Тип | Норма расхода электролита при первой заливке, л | Тип | Норма расхода электролита при первой заливке, л |
АКН-2,25 | 0,04 | КН-60 | 0,75 |
Примечание. При приготовлении электролита желательно норму увеличить на 10 – 15 % для создания резерва на отход и другие непредвиденные случаи.
В крайнем случае можно использовать любую сырую чистую питьевую воду (кроме минеральной).
Затем, пользуясь данными табл. 5.3, определяем необходимое количество химических компонентов: едкого калия или едкого натрия, а также едкого лития для добавки. Расход дистиллированной воды на 1 кг твердой и на 1 л жидкой щелочи для приготовления электролита необходимой плотности приведен в табл. 4.3.
Таблица 4.3
Расход дистиллированной воды, необходимой для приготовления электролита для кадмиевоникелевых и железоникелевых аккумуляторов
Щелочь | Плотность, г/смз3 | Количество воды, л | |
на 1 кг твердой щелочи | на 1 кг жидкой щелочи плотностью 1,41 г/см3 | ||
Калиевая или готовая составная, т. е. с добавкой едкого лития Калиево-литиевая Натриевая или готовая составная натриево-литиевая |
1,19 – 1,21 1,25 – 1,27
1,17– 1,19 |
3 2
5 |
1 0,55
1,5 |
Для определения массы твердых щелочей, необходимой по норме, приведенной в табл. 19, достаточно разделить:
на три требуемое количество воды, если необходимо приготовить калиевый или составной калиево-литиевый раствор плотностью 1,19 – 1,21 г/см3;
на два, если необходимо приготовить калиевый электролит для работы при температуре
– 20…– 40° С или составной калиево-литиевый плотностью 1,25 –1,27 г/см3;
на пять, если необходимо приготовить натриевый или составной натриево-литиевый электролит плотностью 1,17 – 1,19 г/см3.
Если составная калиево-литиевая или натриево-литиевая щелочь отсутствуют, а имеется едкий калий, едкий натрий и едкий литий, то расчет потребности в твердых щелочах производится по тому же принципу, как указано выше. Следует иметь в виду, что в частном, полученном в результате деления, учитывается и масса едкого лития.
Щелочные аккумуляторы — особенности, плюсы и минусы
Щелочные батареи представляют собой портативный источник постоянного тока, заправленный электролитом на основе водного раствора едкого натрия или калия. Изделия отличаются повышенным сроком эксплуатации, достигающим 25 лет (устройства ламельного типа). Оборудование поддерживает алгоритмы ускоренной зарядки, при разрядке обеспечивается повышенная мощность.
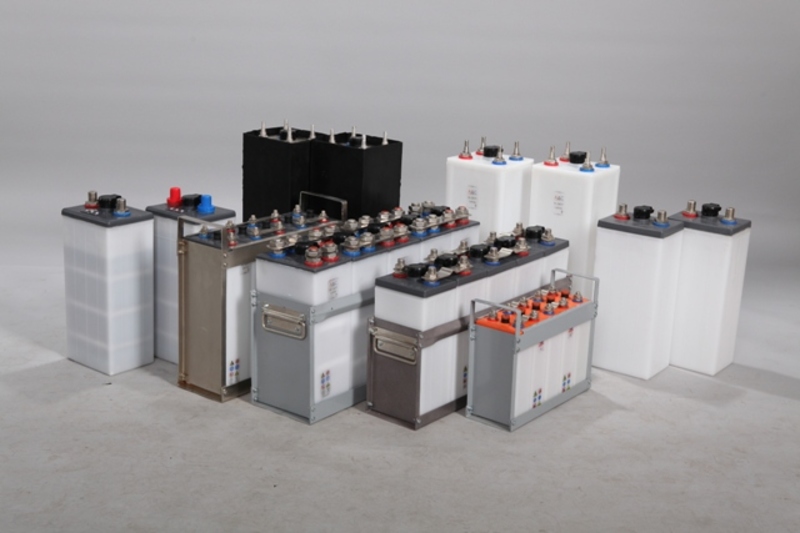
Отличие от других АКБ
Наибольшее распространение получили щелочные аккумуляторы на основе никель-кадмиевых или никель-железных композиций. Положительные электроды кадмиевых батарей изготовлены из соединения гидрата закиси никеля и графитового порошка с добавлением окиси бария.
Отрицательные пластины выполнены из чистого кадмия/железа или гидрата закиси кадмия/железа. В состав щелочного электролита (на основе гидроксида калия) введен гидроксид лития, способствующий повышению емкости и улучшению разрядных характеристик.
Активная масса на катоде и аноде нанесена на стальную сетку, что позволяет увеличить площадь вещества, принимающего участие в электрохимической реакции. В полость банок залит жидкий электролит.
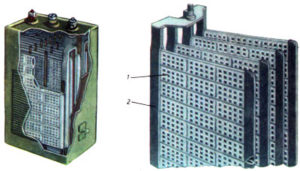
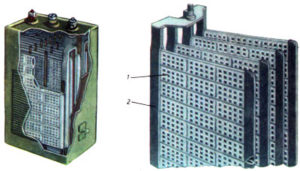
Устройство щелочного аккумулятора
В устройство щелочного аккумулятора дискового типа входят анодная и катодная пластины, разделенные пластиковым сепаратором. В состав электролита введены специальные загустители, способствующие удержанию раствора в полостях сепаратора.
В отличие от кислотных батарей, щелочные элементы допускают перезарядку. Стандартный алгоритм восстановления емкости занимает 6 часов. После длительного хранения в разряженном состоянии или эксплуатации в цепях с пониженным энергопотреблением производится интенсивная зарядка, длящаяся до 12 часов.
При падении силы тока в цепи зарядки ниже нормативного значения рабочие характеристики щелочных элементов питания ухудшаются.
Зарядка никель-железных батарей при температуре воздуха ниже 0°С не рекомендуется.
Химические процессы
Во время работы батареи протекает обратимая химическая реакция взаимодействия материалов катода и анода с ионами электролита. В результате положительные пластины покрываются слоем нестехиометрического гидрата закиси никеля, а на отрицательных электродах формируется гидрат окиси кадмия. Во внешней цепи образуется разница потенциалов, составляющая 1,45 В (рабочее напряжение 1,2 В).
При подаче напряжения от зарядного блока реакция происходит в обратном направлении — гидрат закиси никеля преобразуется в гидроокись никеля, а на отрицательной пластине восстанавливается кадмий. Вещества, используемые в батарее, не вступают в реакции между собой.
Также отсутствует растворение материалов в электролите, что способствует поддержанию химического состава и плотности рабочей жидкости. Стабильность плотности электролита повышает устойчивость оборудования к воздействию низких температур.
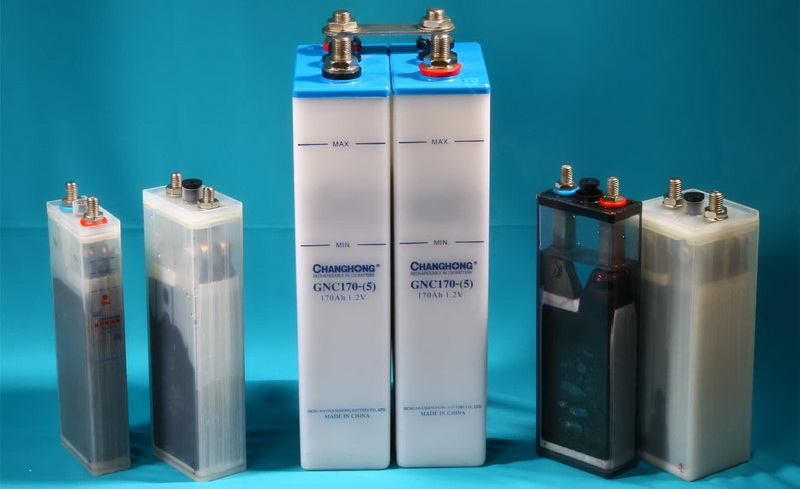
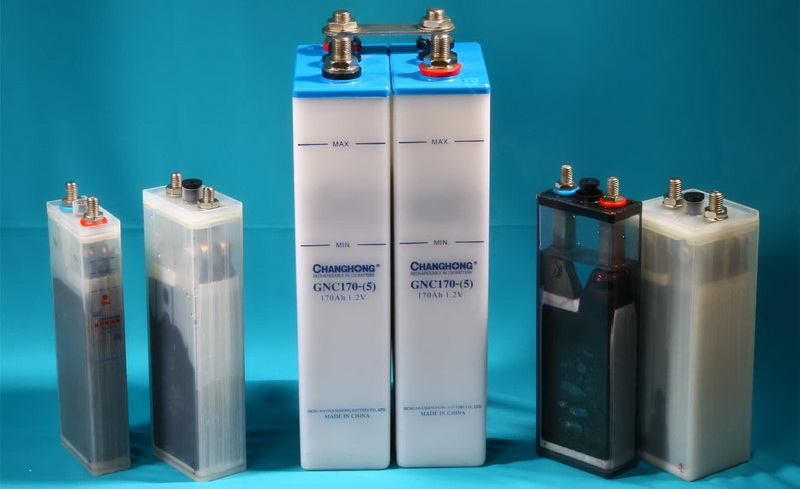
Аккумулятор никель-кадмиевый KL-55
В процессе работы батареи происходит разложение воды, входящей в состав электролита. Для восстановления используются циклы рекомбинации, дополненные периодической доливкой воды (по мере снижения уровня жидкости в банках).
Едкий калий или натрий активно поглощает углекислый газ, находящийся в атмосферном воздухе. В результате происходит карбонизация и снижение электропроводных характеристик раствора. Для восстановления параметров выполняется периодическая замена жидкости, химических способов регенерации не существует.
Замена электролита
Для продления ресурса щелочной АКБ электролит меняется через 100-125 циклов зарядки и разрядки. Перед сливом рабочей жидкости производится разрядка источника постоянного тока до напряжения 1 Вольт (для каждого элемента).
После слива отработавшего раствора полости промываются дистиллированной водой или раствором щелочи. Для удаления остатков загрязнений корпус аккумулятора встряхивается. Использовать механические приспособления для удаления грязи запрещается.
Свежий раствор с необходимой плотностью заливается непосредственно после промывки. Батарея выдерживается на протяжении 2-3 часов, рабочая жидкость заполняет пустоты между положительными и отрицательными пластинами.
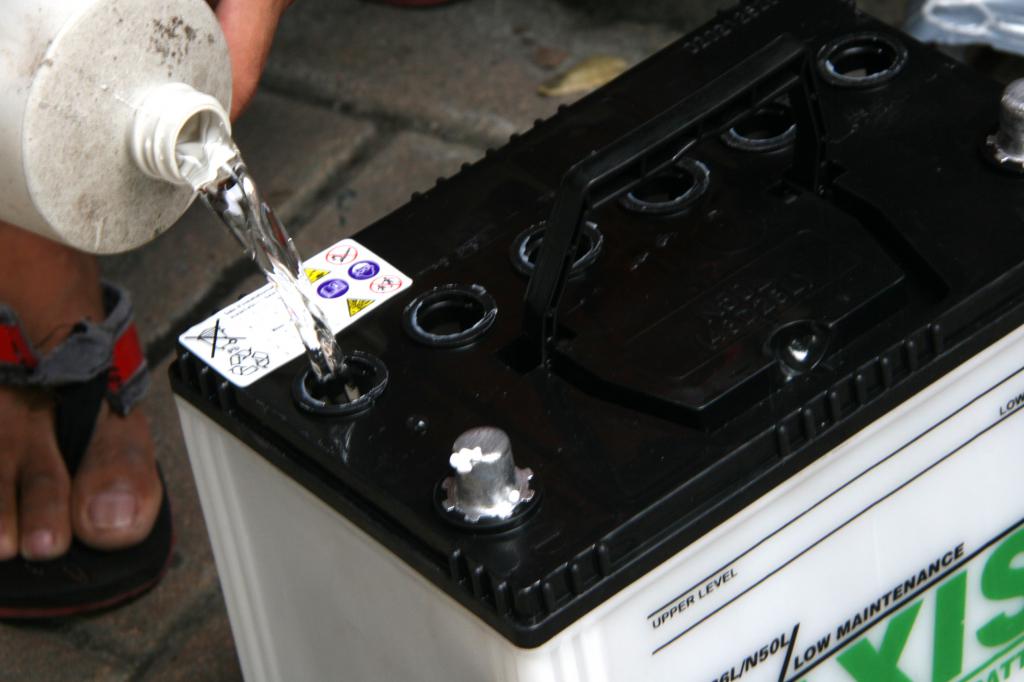
Затем проверяется плотность раствора и осуществляется зарядка, для корректировки состава электролита используется дистиллированная вода. Не допускается хранение или эксплуатация щелочной аккумуляторной батареи с оголенными торцами пластин и вывернутыми пробками.
Преимущества и недостатки
Как и любой источник питания, щелочные АКБ обладают преимуществами и недостатками, определяющими сферы применения изделий. Материалы анода и катода обладают повышенной электрической проводимостью, что позволяет повышать ток в цепи разрядки/зарядки выше номинального значения без риска разрушения активной массы.
Щелочные аккумуляторные батареи обладают ресурсом до 3 тыс. циклов (в 2 раза выше, чем у свинцово-кислотных АКБ).
Конструкция допускает кратковременное короткое замыкание, губительное для кислотных батарей.
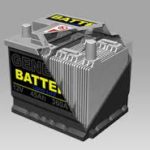
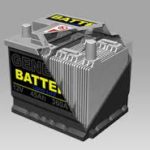
Схема аккумулятора
Дополнительным плюсом щелочных элементов является повышенная механическая прочность элементов конструкции, лишенных пластичного свинца. Пластины установлены в специальных стальных рамках.
Для изготовления корпусов используется лист из углеродистой стали, дополнительно защищающий детали от повреждений.
Меньший вес элементов конструкции обеспечивает повышение удельных энергетических характеристик.
Недостатки щелочных источников тока:
- При подключении к зарядному блоку частично разряженного аккумулятора наблюдается снижение емкости («эффект памяти»). Процесс является обратимым, при проведении тренировочных циклов емкость восстанавливается до исходных параметров. В основе процесса лежит способность гидроксида никеля образовывать разные модификации вещества.
- Обратимость процесса снижения емкости имеет одновременно и плюсы, и минусы. После восстановления гидроксид никеля обладает повышенной активностью, что приводит к ускорению процессов саморазряда. Восстановленный кадмиевый аккумулятор теряет за 1 час до 10% емкости. Но в процессе нормальной эксплуатации эффект исчезает.
- Разброс напряжения элементов, установленных в банке. Для обеспечения равномерной емкости необходимо использовать специальные зарядные устройства.
- Повышенный расход электроэнергии при зарядке, КПД составляет не более 55%.
- Необходимость периодического обслуживания с заменой электролита, для выполнения работ требуется квалифицированный персонал. Увеличенный объем работ ограничивает использование щелочных батарей для автомобиля.
Сфера применения
Щелочные источники постоянного тока используются в электронных приборах вместо базовых гальванических элементов. Из-за сниженного внутреннего сопротивления обеспечиваются стабильные рабочие характеристики и уменьшается вероятность перегрева источника питания.
Батареи применяются для обеспечения электроэнергией тяговых электродвигателей, установленных на складской технике.
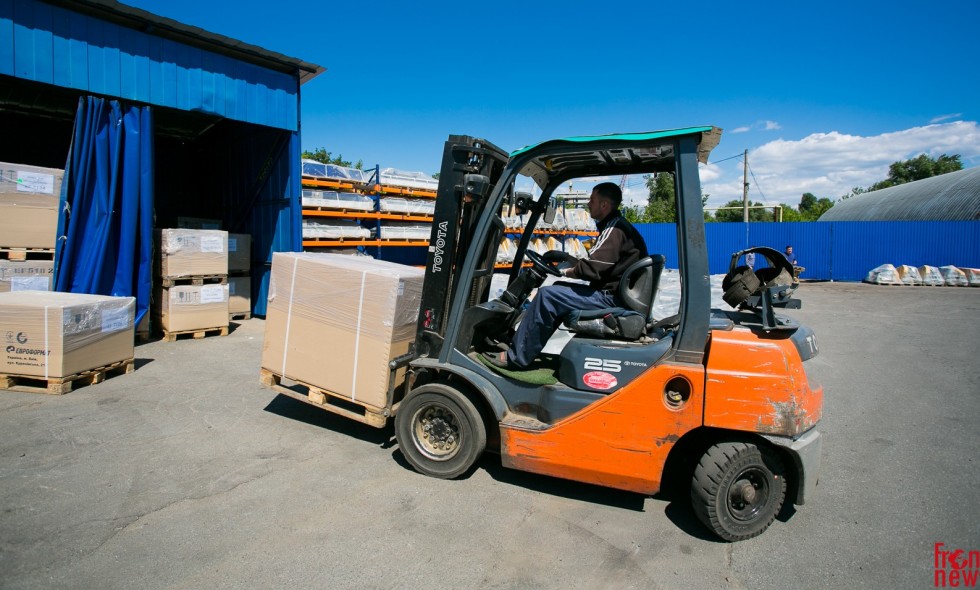
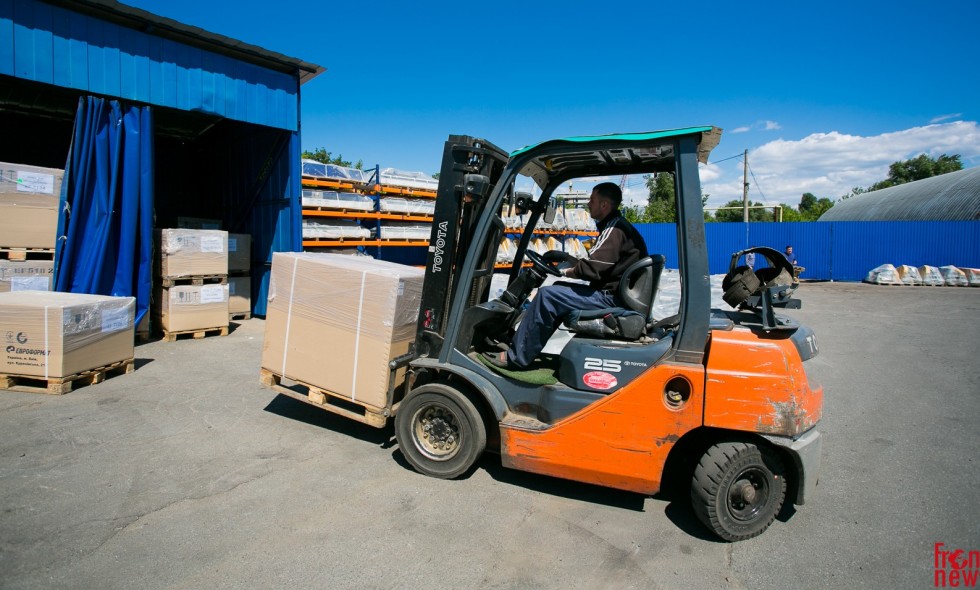
Щелочные аккумуляторы применяются на складской технике
Аналогичные устройства встречаются в конструкции вспомогательных приводов, установленных на электрическом городском транспорте (трамваи или троллейбусы).
Источники питания щелочного типа применяются для привода электрических двигателей строительного инструмента (малогабаритные дрели, шуруповерты).
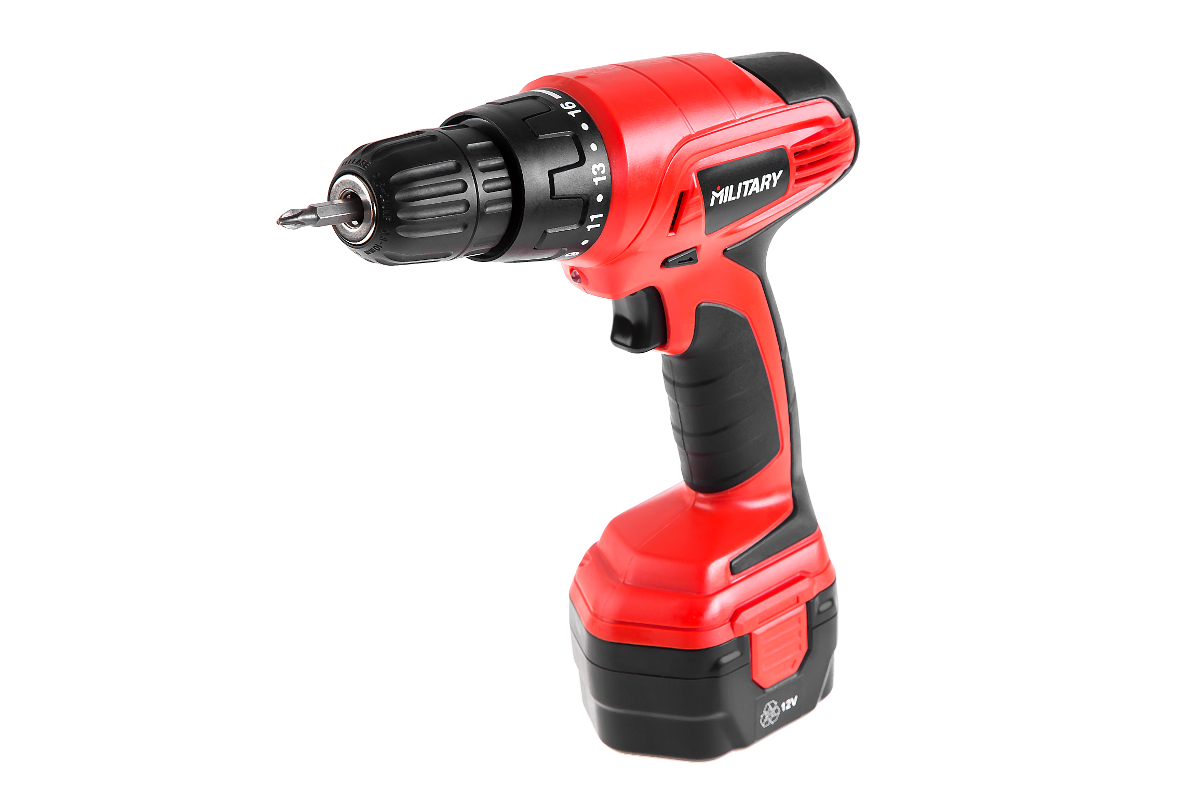
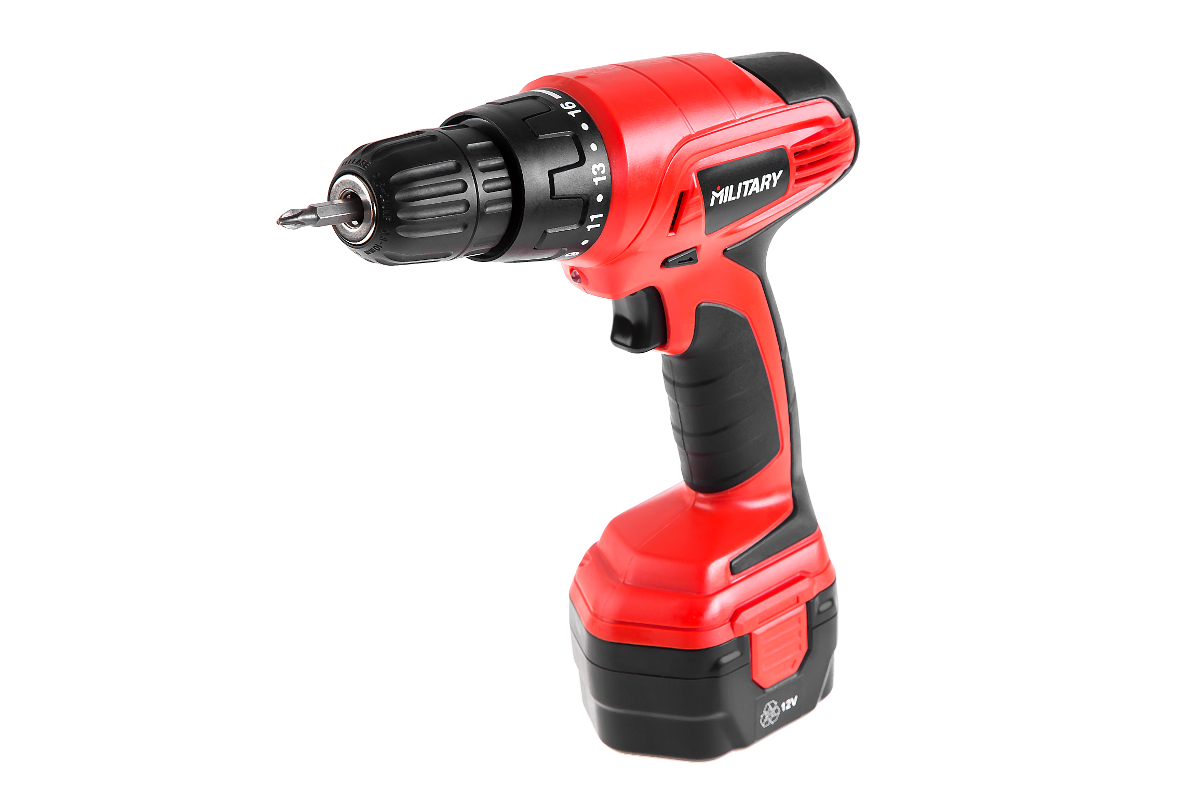
Аккумуляторная дрель
Из-за постоянного ужесточения экологических требований происходит вытеснение никель-кадмиевых аккумуляторов устройствами на основе лития.
Небольшие габариты кадмиевых аккумуляторов, способность работать при понижении температуры до -40°С и высокая энергоемкость предопределили распространение изделий в авиации (в качестве бортовых источников питания).
Щелочные автомобильные аккумуляторы ограниченно используются в качестве устройств для пуска и обеспечения работы силового агрегата. Традиционные свинцово-кислотные обладают пониженным внутренним сопротивлением, обеспечивая увеличенный ток холодной прокрутки. Никелевые элементы обладают «эффектом памяти», негативно влияющим на емкость устройства при нарушении условий разряда и заряда.
Дополнительными минусами щелочных аккумуляторов 12В является сниженная емкость и увеличенная цена.
Малогабаритные батареи щелочного типа, имеющие корпуса цилиндрической конфигурации, используются в наручных часах и бытовой технике.
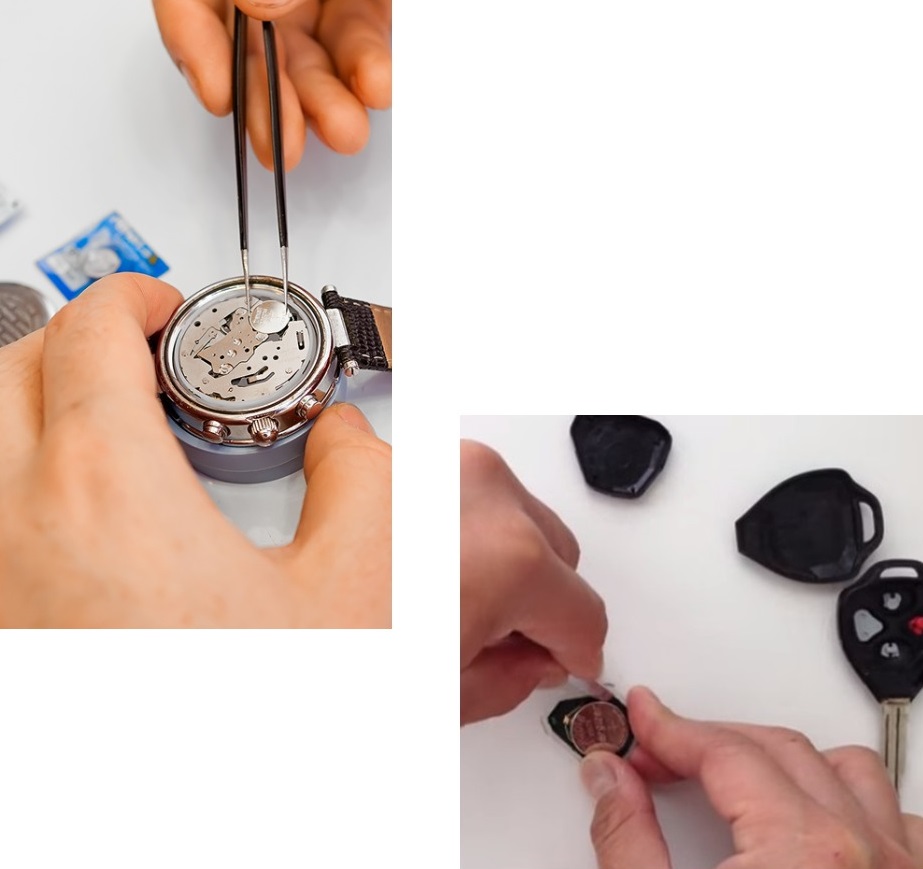
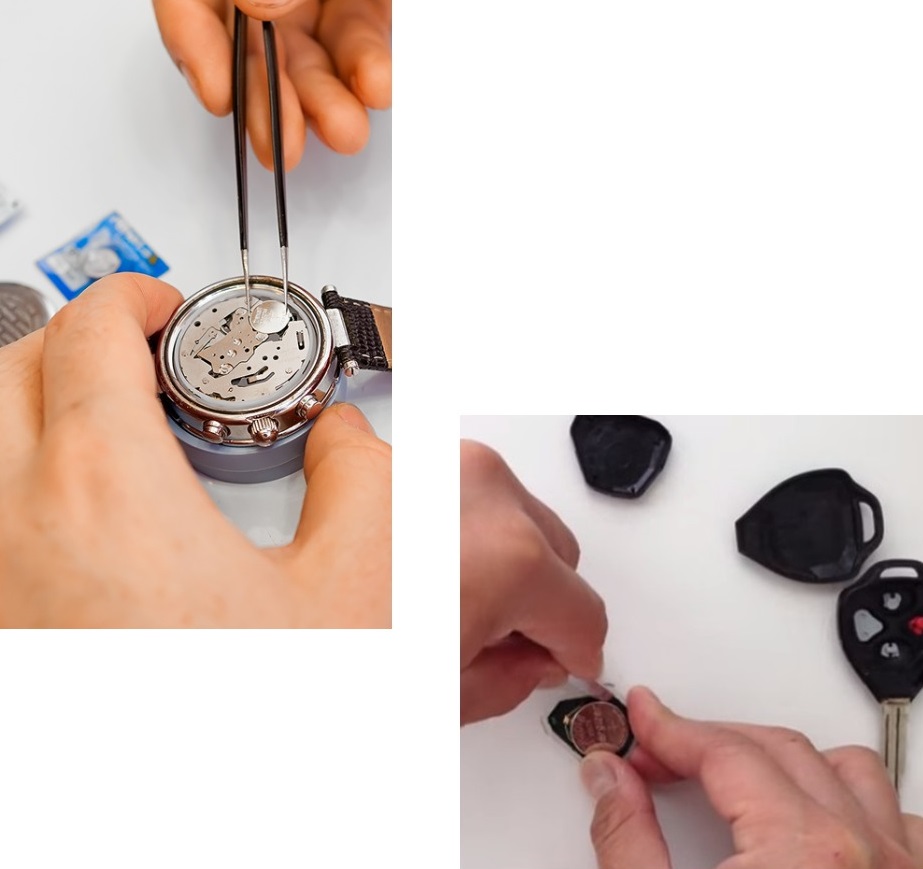
Щелочные аккумуляторы широко используются в быту
Дисковые батареи отличаются применением герметичного металлического кожуха, рабочий ток не превышает 10% емкости (для снижения газообразования).
Правила эксплуатации
Основные требования к эксплуатации перезаряжаемых источников постоянного тока щелочного типа:
- При эксплуатации устройств учитывается характеристика кривой падения напряжения. После подачи нагрузки происходит постепенное снижение напряжения до 1,1 В. Дальнейшая разрядка батареи приводит к снижению ресурса и разрушению активной массы на электродных пластинах.
- Зарядка аккумуляторов выполняется с выкрученными пробками, при повышении температуры и давления происходит разрушение корпуса и металлических сеток электродных пластин.
- Через каждые 10 дней эксплуатации производится визуальный осмотр корпуса изделия, затем проверяется и доводится до нормативного значения уровень электролита. В конструкции пробок предусмотрены дренажные каналы, предназначенные для сброса давления газов. Каналы прочищаются, одновременно проверяется состояние резиновых уплотнителей, потрескавшиеся элементы подлежат замене.
- Через 100-125 рабочих циклов или через год эксплуатации производится замена электролита (с промывкой банок). Внешние поверхности корпуса очищаются от загрязнений, производится проверка затяжки креплений соединительных пластин. Для удаления следов коррозии на неокрашенных поверхностях используется ветошь, смоченная керосином.
- Отработавшие аккумуляторные батареи с щелочным электролитом запрещено выбрасывать на свалки бытового мусора. Поскольку устройства имеют ограниченное распространение, их прием на утилизацию осуществляется специализированными организациями.
Правила хранения
Сухой щелочной аккумулятор хранится с закрученными пробками, срок складирования устройств не превышает 2 месяцев. Если устройство находилось в эксплуатации до 1 года, то перед длительным хранением необходимо снизить напряжение до 1 В и произвести слив электролита.
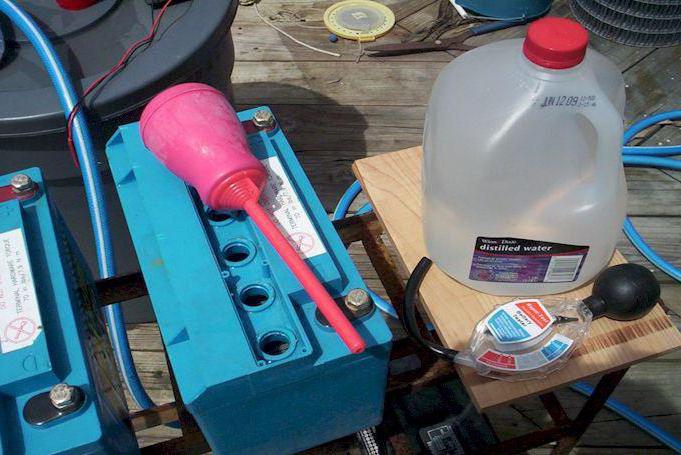
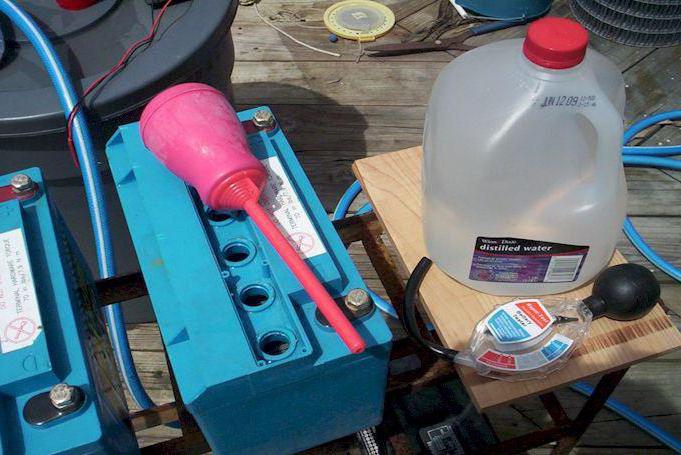
Слив электролита должен производиться путем откачивания
Затем проводятся дополнительные мероприятия по консервации и очистке корпуса от отложений солей, пробки плотно заворачиваются в отверстия банок, предотвращая циркуляцию воздуха. Аналогичные действия выполняются при длительной транспортировке изделий.
При хранении щелочных источников питания требуется соблюдать условия:
- периодически проверять затяжку пробок и состояние резиновых уплотнительных колец;
- удалять следы соли с поверхности корпуса;
- металлический корпус источника питания очищается от следов коррозии и покрывается слоем защитной краски или лака.
Для защиты стального кожуха используется специальный лак черного цвета на битумной основе. Для предохранения защитного покрытия от повреждений щелочным раствором используются специальные реагенты.
В процессе хранения проводится периодический осмотр изделий с восстановлением защитных покрытий и удалением потеков электролита.
Категорически запрещается складирование в одном помещении свинцово-кислотных и щелочных аккумуляторов.
Срок хранения изделий зависит от температурных условий в помещениях. Никель-кадмиевые источники со слитым электролитом допускается хранить в полевых условиях в течение полугода, при размещении изделий в закрытых помещениях срок увеличивается до 5 лет.
Никель-железные элементы допускается хранить на протяжении 3,5 года (только в помещении). Необходимо предусмотреть защиту складских мест от воздействия прямого солнечного излучения и атмосферных осадков.
Электролит состав — Справочник химика 21
Электролит Состав, % (масс.) Темпе- ратура начала Плотность Удельная электро- [c.236]Кроме того, применяют электролит, состав которого следующий (г/л) [c.115]
Гликолевый электролит. Состав электролита (в г/л) [c.178]
Электролит Состав электролита Dk, а дм Температура, [c.76]
В. Ф. Молчанов [626] провел испытания на усталостную прочность образцов из стали 45 диаметром 9,48 мм на машине МУИ-6000 после хромирования в саморегулирующемся электролите (состав см. в табл. 6.1). Сталь имела состав (%) 0 46 С 0,28 51 0,65 Мп 0,023 5 0,21 Р 0,14 Сг 0,15 N1. Механические свойства стали 0т=465 МН/м (47,4 кГ/мм ), 0в=723 МН/м (73,8 кГ/мм ), 05 = 22%, а1) = 40,6%. Заготовки образцов подвергались нормализации при 850°С в течение 20 мин. Всего было испытано 10 серий образцов (табл. 6.6), каждая по 6—7 образцов. Толщина покрытия во всех сериях составляла 0,05 мм, кроме серии № 5 (0,3 мм). Кривые усталости приведены на рис. 6.1. [c.260]
Фнг. 30. Содержание цинка в латуни. (/) и олова в бронзе (2) в зависимости от концентрации свободного цианида в электролите. Состав электролита латунирования 16 Г/л Си и 16 Г/л 2п плотность тока 0,5 а/дм , температура 20°. [c.59]
Рецептура и режим работы ванн.. Для цинкования электродов серебряно-цинковых источников тока применяется цианистый электролит. Состав электролита и режим работы ванны следующие [c.45]
Золочение в цианистом электролите. Состав цианистого электролита и режим работы следующие [c.162]
Электрохимическое полирование. Электрохимическое полирование —- процесс выравнивания поверхности металла путем анодного растворения и применяется для повышения качества поверхности металлических изделий в дополнение к механическому шлифованию и полированию. Обрабатываемые детали завешиваются в ванну с электролитом в качестве анодов, катодами служат электроды из таких металлов, которые не растворяются в данном электролите. Состав электролита и режим процесса должны обеспечивать преимущественное растворение микроскопических выступов поверхности, в результате чего поверхность становится гладкой и приобретает блеск. При электрополировании решающую роль играет плотность тока, которая значительно выше, чем применяемая при осаждении металла. [c.138]
Закон Фарадея может быть использован для точного определения количества электричества, проходящего в цепи постоянного тока. Для этого нужно заставить ток проходить через электролит, состав которого обеспечивает протекание одной единственной реакции хотя бы на одном из электродов. Тогда, определив количество образовавшегося продукта реакции, мы можем, пользуясь величиной электрохимического эквивалента, точно рассчитать количество прошедшего электричества. Приборы, применяемые для этой цели, называются кулонометрами. [c.52]
Для стабилизации электролита по содержанию серной кислоты предложено вводить ее в виде соли трудно растворимого сернокислого стронция [1]. Избыток сернокислого стронция, находящийся в осадке, длительное время поддерживает требуемую концентрацию сернокислотного аниона в электролите. Состав электролита (г/л) хромовый ангидрид — 140—170 сернокислый стронций— 5—6. По данным работы [1], на рис. 9 приводятся сведения об интервале блестящих осадков, твердости, износостойкости и пористости покрытий, полученных из этого малоконцентрированного электролита. В табл. 1 приведены рекомендуемые режимы в зависимости от назначения покрытия. [c.12]
Применение анодно-струйного способа позволяет автоматизировать процесс хромирования и значительно повысить его производительность за счет более высокого выхода по току и применения высоких плотностей тока. При этом повышается равномерность отложения хромового покрытия по толщине слоя, создаются условия для получения осадков хрома заданной толщины. Установки для анодно-струйного хромирования могут быть созданы на несколько одновременно работающих ячеек. Вариантом анодно-струйной установки является анод, который не только подает электролит к хромируемой поверхности, но и равномерно отводит его из рабочего объема через ряд сливных отверстий на поверхности анода. Этим достигается большая равномерность омывания электролитом хромируемой поверхности, способствующая более равномерному осаждению покрытия, особенно при значительных плотностях тока. Этот вариант получил название возвратно-струйного хромирования [21]. Схема такого анода для хромирования коленчатого вала приведена на рис. 39. Ячейка состоит из двух половин, охватывающих шейку коленчатого вала. В корпусе установлен анод. Электролит подается через трубу в кольцевую канавку через осевые каналы — отверстия и поступает в рабочую зону. Удаляется электролит через систему отверстий и трубу отвода. Весь агрегат для возвратно струйного хромирования, использующего холодный электролит, состо нт из следующих узлов (рис. 40) электролитическая ячейка с анодом монтируемая на хромируемой детали, емкостей для электролита анодного травления и улавливания электролита, холодильный агрегат с теплообменным аппаратом, выпрямитель и система трубопрово дов с регулирующими клапанами. Ввиду особой важности под держания постоянного уровня электролита и температуры электроли та в заданных узких пределах рекомендуется оснастить ванну хроми рования устройством для автоматического регулирования уровня электролита и температуры [12]. [c.70]
Растворенная кислота НС1 переносится здесь из раствора раствор» не непосредственно, а в результате протекания двух противоположно направленных электрохимических реакций. Благодаря отсутствию диффузионных потенциалов такие цепи дают возможность точно определить коэффициент активности определенного компонента (в данном случае НС1 в электролите, состав которого можно усложнять). [c.547]
Кремнефтористоводородный электролит. Состав электролита и режим работы с ним следующие [c.27]
Растворимость анодных продуктов в электролите, скорость диффузии их в электролит, состав и физико-химические свойства анодной пленки имеют сушественное значение для процесса полирования. Поэтому этот процесс у различных материалов происходит неодинаково. У многих металлов и сплавов (медь, никель, алюминий, нержавеющие хромистые и хромоникелевые стали) сглаживание сопровождается появлением блеска на обработа
Состав электролитов цинкования и их режимы

Защитные свойства цинкового покрытия определяются не его средней толщиной на всей поверхности изделий, а фактической толщиной на том или ином участке и степенью его равномерности и целостности. Поэтому основная характеристика электролита при цинковании — рассеивающая способность.
Виды электролитов
Для осаждения цинка разработано большое количество электролитов как кислых, так и щелочных. Из кислых электролитов следует отметить:
- сернокислые и борфтористоводородные.
А из щелочных электролитов:
- цианистые и нецианистые. К ним относятся цинкатные, пирофосфатные и аммиакатные. Последние могут иметь и слабокислую реакцию.
Основное различие между ними — это низкая рассеивающая способность кислых и высокая рассеивающая способность щелочных электролитов. Промышленное применение из кислых электролитов нашли сернокислые электролиты, из щелочных -цианистые, а также их заменители — аммиакатные.
Для цинкования используют аноды из металлического цинка в форме вальцованных пластин толщиной 5-12 мм различных размеров или сферические аноды диаметром 50 мм. Во избежание загрязнения электролита аноды необходимо помещать в чехлы из кислотостойкой ткани (стеклоткань, шерсть). Аноды следует периодически очищать травлением или щетками. Сферические аноды более целесообразны, так как имеют равномерный износ и позволяют легко регулировать глубину погружения.
Кислые электролиты имеют плохую рассеивающую способность. Кроме того, покрытия, полученные в кислых электролитах, обладают более грубой структурой и меньшей коррозионной стойкостью, чем покрытия, полученные в щелочных электролитах. В то же время кислые электролиты устойчивы, допускают применение высокой плотности тока, особенно при перемешивании и высоком (близком к 100 %) выходе цинка по току. Покрытия имеют светлый цвет, характеризуются повышенной пластичностью, прочным сцеплением с основным металлом и могут выдержать различную механическую обработку. Поэтому кислые электролиты широко используют для нанесения покрытий на малорельефные изделия, а также полуфабрикаты — листы, проволоки, полосы.
Сернокислые электролиты отличаются простотой состава, низкой стоимостью компонентов и хорошим качеством покрытий даже при больших изменениях состава электролита и режима его работы. Так, температурный режим электролита колеблется в пределах 15-30 °С, а практически сернокислые электролиты позволяют вести осаждение цинка даже при температурах около 0 °С и ниже.
Для составления сернокислого электролита требуются следующие материалы:
- Сернокислый цинк ZnSО4*7Н2О — белый кристаллический порошок, растворимость в воде при 20 °С — свыше 900 г/л;
- Сернокислый натрий Na2SО4*10Н2О — бесцветные кристаллы, растворимость в воде при 20 °С — более 400 г/л. Вводится для повышения электропроводности электролитов;
- Сернокислый алюминий Аl2(SО4)3*18Н2О — бесцветная кристаллическая масса, растворимость в воде при 20 °С около — 50 г/л. Применяется как буферное соединение для поддержания рН на заданном уровне;
- Пекстрин — желтый порошок, растворимый в воде с образованием клейкого мутного раствора. Применяется для создания мелкокристалличности покрытия. Качество и эффективность добавки следует проверять, растворением отдельной пробы в опытной ванночке;
При составлении сернокислого электролита желательно каждый из компонентов растворять в отдельности в теплой воде. После отстаивания и фильтрации растворы сливают вместе в рабочую ванну цинкования. Затем электролит доливают водой до заданного уровня и проверяют величину рН, корректируя ее 2-3%-ным раствором серной кислоты или едкого натра. После этого прорабатывают электролит на случайных катодах до получения светлых и гладких покрытий и приступают к его эксплуатации.
Некоторые составы кислых электролитов представлены в табл. 5.7.
Сернокислый электролит номер 1 предназначен для деталей простой конфигурации, позволяющий получать светлые матовые покрытия. Электролит номер 2 пригоден для непрерывного цинкования проволоки или ленты, с повышением плотности тока до 8-10 А/дм2. Следует иметь ввиду, что при плотности тока более 2 А/дм2 обработку производят при перемешивании и фильтрации электролита. При введении в электролит блескообразователей типа дисульфонафталиновой кислоты покрытия (электролит номер 3) получаются очень светлые, блестящие или полублестящие.
Из кислых электролитов следует для отдельных работ рекомендовать борфтористоводородный. По стоимости компонентов он дороже сернокислого, но позволяет применять плотности тока от 10 и выше А/дм2, а насыщение водородом и, следовательно, водородная хрупкость в несколько раз ниже, чем при цинковании в других электролитах. Для электролита характерен следующий состав (г/л) и режимы:
- цинк борфтористоводородный — 280-300;
- аммоний борфтористоводородный — 28-30;
- аммоний хлористый — 28 30;
- солодковый корень — 0,5-1,0;
- кислота борфтористоводородная (свободная) вводится для достижения кислотности на уровне рН — 1,4-2;
- температура, °С — 15-25;
- плотность тока доходит, А/дм2 — до 10;
- температура, °С — 50-55;
- плотность тока, А/дм2 — до 50.
Таблица 5.7. Составы и режимы работы электролитов.
Компоненты |
Содержание компонентов (г/л) в электролите |
||
1 |
2 |
3 |
|
Сернокислый цинк |
200-250 |
400-500 |
200-250 |
Сернокислый натрий |
50-100 |
50-100 |
— |
Сернокислый алюминий |
20-30 |
20-30 |
25-30 |
Декстрин |
8-10 |
8-10 |
8-10 |
Борная кислота |
— |
— |
25-30 |
Блескообразователь ДЦУ и У2 |
— |
— |
1,5-2,5 |
Температура, °С |
15-30 |
15-30 |
15-30 |
Величина рН |
3,6-4,4 |
— |
4,0-4,2 |
Плотность тока, А/дм2 |
1-4 |
8-10 |
1-3 |
Выход по току |
96-98 |
96-98 |
— |
При указанных режимах выход по току составляет около 90 %.
Щелочные электролиты обладают хорошей рассеивающей способностью, а покрытия, полученные в этих электролитах, — более высокой коррозионной стойкостью. Однако щелочные электролиты менее устойчивы, допустимая плотность тока в них ниже, и с повышением ее заметно снижается выход цинка по току. Такие электролиты применяют для цинкования изделий сложной формы. По составу щелочные электролиты подразделяются на цианистые, аммиакатные и цинкатные.
Цианистые электролиты
Цианистые электролиты обладают высокой рассеивающей способностью и служат для цинкования изделий сложной формы в стационарных, колокольных и барабанных ваннах. Сами покрытия получаются светлыми, гладкими и отличаются мелкокристаллической структурой. В настоящее время существует несколько вариантов их составов, но все они состоят из трех обязательных компонентов: окиси цинка, цианистого натрия и едкого натра, которые сочетаются между собой в различных соотношениях, образуя сложные комплексные соединения. Кроме того, они могут отличаться различными добавками, способствующими получению светлых, блестящих или полублестящих покрытий.
Однако следует иметь в виду, что цианистые электролиты очень ядовиты, и обращаться с ними необходимо очень осторожно. Токсичность их повышается, если в электролите мало едкого натра, в результате чего образуется синильная кислота — сильнейший яд.
Для составления цианистых электролитов требуются следующие химикаты:
- Окись цинка ZnO;
- Цианистый натрий NaСN — белый порошок, растворимость в воде до 600 г/л. Весьма ядовит. При составлении электролитов применяется только в предварительно растворенном состоянии. Служит для получения комплексной соли Na2Zn(СN)4;
- Едкий натр NaОН;
- Глицерин технический — вязкая прозрачная жидкость, применяется для повышения мелкокристалличности осадков цинка;
- Сернистый натрий Na2S — белая кристаллическая масса, легко растворимая в воде, имеет характерный запах. Вводится в электролит для осаждения тяжелых металлов — меди, свинца и железа.
При составлении электролита сухую окись цинка замешивают водой до сметанообразного состояния и затем вводят в раствор цианистого натрия. После этого приливают крепкий раствор едкого натра, доводят электролит водой до рабочего уровня и вводят добавку глицерина. Сернистый натрий добавляют в последнюю очередь и дают осесть возможному осадку тяжелых металлов, затем приступают к эксплуатации.
Составы и режимы работы наиболее применяемых электролитов приведены в табл. 5.8.
Покрытия, полученные в электролите номер 1 после осветления в 3%-ном растворе азотной кислоты и пассивирования в 5%-ном растворе хромового ангидрида, становятся блестящими и не оставляют следов от захвата руками. Электролит 2 предназначен для получения светлых матовых покрытий, создающих после пассивирования на поверхности яркую радужную пленку. Электролит 3 характеризуется высокой рассеивающей способностью и особо пригоден для колокольных и барабанных ванн.
Для замены токсичных цианистых электролитов разработаны и используются аммиакатные, аммиакатно-уротропиновые, цин-катные, пирофосфатные и другие электролиты. Они не ядовиты, просты по составу и дешевы, обладают высокой электропроводностью и хорошей рассеивающей способностью цианистых электролитов. Выход цинка по току в них значительно выше, чем в цианистых.
Наиболее высокой рассеивающей способностью, приближающейся к цианистым электролитам, отличаются аммиакатные, в частности аммиакатно-уротропиновые электролиты. Для приготовления таких электролитов необходимы следующие основные химикаты:
- хлористый аммоний NH4Cl технический — белый кристаллический порошок, растворимость в воде — до 300 г/л. Горячий крепкий раствор хлористого аммония переводит окись цинка в растворимые комплексы;
- окись цинка ZnO — может быть заменена сухими цилковыми белилами. Белый порошок, нерастворимый в воде, но растворимый в концентрированных растворах цианистого натрия, едкого натра, а также в горячих концентрированных растворах хлористого аммония и сернокислого аммония;
- уксуснокислый аммоний — белый кристаллический порошок.
Таблица 5.8. Составы и режимы цианистых электролитов.
Компоненты |
Содержание компонентов (г/л) в электролите |
||
1 |
2 |
3 |
|
Окись цинка |
10-20 |
40-45 |
8-10 |
Цианистый натрий |
20-30 |
75-85 |
15-25 |
Едкий натр |
50-70 |
40-60 |
10-25 |
Сернистый натрий |
0,5-5,0 |
— |
— |
Глицерин |
0,5-1,0 |
— |
— |
Температура, °С |
15-40 |
15-25 |
15-25 |
Плотность тока, А/дм2 |
1-2 |
1,5-7 |
0,5-2 |
Выход по току, % |
80-83 |
75-80 |
70-80 |
Для приготовления электролита необходимо подогреть концентрированный раствор хлористого аммония до 60-70 °С и прибавить к нему при непрерывном помешивании окись цинка или гидрат окиси цинка. После растворения соединений цинка в растворе хлористого аммония и образования комплексных солей цинка в полученный раствор вводят остальные компоненты, доводят водой до рабочего уровня и устанавливают правильную величину рН. При этом если величина рН получилась менее 7, то корректировку рН производят водным раствором аммиака, а при рН = 8,5 и выше эту величину доводят до заданной раствором уксусной кислоты. После этого электролит следует проработать на случайных катодах.
Один из таких электролитов имеет следующий состав (г/л) и режим работы:
- окись цинка — 25-40;
- хлористый аммоний — 200-220;
- уксуснокислый аммоний — 80-100;
- уротропин — 20-25, диспергатор НФ, мл/л — 6-8;
- препарат ОС-20 — 4-5;
- температура, °С — 20-35;
- величина рН — 7,5-8,2;
- плотность тока, А/дм2 — 1-3.
Следует отметить, что электролиты на основе хлористого аммония содержат агрессивный ион хлора. Поэтому промывка деталей в воде (после цинкования) должна быть тщательной, особенно для деталей со сложным профилем, глухими отверстиями и щелевыми зазорами. Пренебрежительное отношение к операции промывки может привести к ускоренной коррозии.
Основной недостаток аммиакатных электролитов — наличие в сточных водах солей аммония, которые недопустимы по требованиям санитарии (допускается не более 2,5 мг/л). В связи с этим применение аммиакатных электролитов в отличие от цинкатных сокращается.
Основу цинкатных электролитов составляют окись цинка и едкий натр. Ориентировочный состав такого электролита (г/л) и режим работы следующие:
- окись цинка — 15-16;
- едкий натр — 150-160;
- полиэтиленполиамин — 1,2-1,6;
- температура, °С — 15-25;
- плотность тока, А/дм2 — 2,0-3,0;
- выход по току, % — 90-95.
Электролит допускает колебания температуры с перегреванием его до 40-50 °С. Для сложнопрофилированных деталей в электролит вводится добавка фенолформальдегидной смолы. Приготовление электролита не имеет специфических особенностей.
Пирофосфатный электролит получил наименьшее распространение, но рассеивающая способность его достаточно высока. Его основу составляет пирофосфорнокислый натрий Na4Р2О7*10Н2О и фосфорнокислый аммоний двузамещенный (NН4)2НРО4. Состав электролита (г/л) и его режим работы следующие:
- пирофосфорнокислый натрий — 180-200;
- сернокислый цинк — 50-60;
- фосфорнокислый аммоний двузамещенный — 16-20;
- декстрин — 3,0-5,0;
- температура, °С — 50-55;
- величина рН — 8,0-8,5;
- катодная плотность тока, А/дм2 — 1,0-3,0;
Электролит пригоден для деталей средней конфигурации.
Возможно Вас так же заинтересуют следующие статьи: comments powered by HyperComments