То и ремонт грм – Техническое обслуживание грм двигателя. Ремонт и техническое обслуживание газораспределительного механизма двигателя внутреннего сгорания. Процесс ремонта узла
- 03.07.2019
Ремонт газораспределительного механизма (ГРМ)
Ремонт распределительного вала
Основными дефектами распределительного вала являются:
- износ опорных шеек;
- износ винтовой шестерни привода масляного насоса;
- износ кулачков;
- прогиб;
- увеличение осевого зазора.
Опорные шейки при износе ремонтируют двумя способами:
- шлифованием их на меньший диаметр
- хромированием
Первый способ ремонта применяют в тех случаях, когда опорами для шеек вала служат сменные втулки, запрессованные в гнезда блока. Если распределительный вал вращается в гнездах, выполненных непосредственно в блоке, то опорные шейки ремонтируют хромированием.
Шейки шлифуют на круглошлифовальном или токарном станке супортно-шлифовальным приспособлением.
Перед шлифованием вал проверяют в центрах по индикатору и выправляют под прессом, если биение превышает 0,05 мм. При шлифовании шеек необходимо учитывать высоту кулачков, так как иначе может создаться положение, при котором вал нельзя будет установить во втулки уменьшенного ремонтного размера. Высота кулачка должна быть меньше самой малой опорной шейки вала на 1—1,5 мм.
После шлифования шеек из блока выпрессовывают старые опорные втулки и запрессовывают новые полуобработанные, внутреннее отверстие которых необходимо обработать под размер шеек развертыванием.
Втулки двигателя ГАЗ-51 имеют два диаметрально расположенных отверстия, из которых одно — большего диаметра — служит для подвода смазки и должно точно располагаться против смазочного канала, а другое, меньшего размера, служит для закрепления втулки и должно располагаться против лунки в гнезде блока.
Рис. Установка опорной втулки распределительного вала:
1 — опорная втулка; 2 — масляный канал; 3 — бородок.
Втулку закрепляют длинным бородком, устанавливаемым в масляный канал, при помощи которого раскернивают малое отверстие втулки; образующийся при этом выступ входит в лунку гнезда блока.
После закрепления втулок их развертывают длинной раздвижной разверткой, обеспечивающей сохранение параллельности осей коленчатого и распределительного валов. При отсутствии сменных втулок (автомобили ГАЗ-MM, «Москвич») гнездам в блоке придают правильную геометрическую форму развертыванием, а опорные шейки хромируют и прошлифовывают на требуемый размер.
Рис. Раздвижная развертка.
Кулачки с небольшим износом и задирами зачищают вначале крупной, а затем мелкой наждачной бумагой, которая должна облегать не менее половины профиля кулачка.
При большом износе кулачков вал заменяют или наплавляют изношенные места газовой сваркой сплавом сормайт. При этом вал помещают в ванну с водой, оставляя на поверхности только часть кулачка, подлежащую наплавке. При наплавке поверхность кулачка достаточно нагреть до состояния «потения», и расплавленный сормайт будет хорошо растекаться по поверхности. При отсутствии сормайта наплавлять можно проволокой от старых клапанных пружин при помощи газовой или электродуговой сварки.
После наплавки сормайтом последующая обработка заключается только в зачистке, а при наплавке сталью необходима закалка. При значительном износе приводной шестерни масляного насоса распределительный вал следует заменить.
Рис. Крепление распределительного вала:
1 — распределительный вал; 2 — шестерня; 3 — упорная шайба; 4 и 6 — болты крепления упорной шайбы; 5 — распорное кольцо.
Увеличенный осевой зазор распределительного вала устраняют путем регулировки упорного болта, помещенного в крышке распределительных шестерен (автомобили ЗИС-5 и ЗИС-150). Для этого болт завертывают до упора в торец вала, а затем, отвертывают на 1/6 оборота и закрепляют контргайку. Если распределительный вал от осевого смещения удерживается упорной шайбой (автомобили М-20 «Победа», ГАЗ-51), то уменьшение осевого зазора до нормальной величины 0,10—0,20 мм достигается заменой изношенной упорной шайбы. Если же это окажется недостаточным, то следует уменьшить толщину распорного кольца, установленного между задним торцом ступицы распределительной шестерни и торцом первой опорной шейки распределительного вала.
Ремонт клапанов
Дефектами клапана могут быть:
- износ и обгорание рабочей фаски;
- коробление головки;
- износ поверхности и торца стержня;
- погнутость стержня.
Небольшой износ рабочей фаски клапана устраняется притиркой клапана к седлу.
Рис. Приборы для притирки клапанов:
а — коловорот; б — притирочная дрель; 1 — ведущая шестерня с шестью зубьями; 2 — ведущая шестерня с девятью зубьями; 3 — ведомая шестерня шпинделя; 4 — шпиндель.
Для притирки клапана проделывают следующие операции:
- Надевают на стержень клапана слабую пружину и устанавливают клапан в направляющую втулку.
- Рабочую фаску клапана смазывают притирочной пастой и при помощи коловорота (рис. а) или специальной притирочной дрели (рис. б) вращают клапан вправо и влево на 1/4 оборота, постепенно поворачивая клапан кругом. При пользовании специальной притирочной дрелью ее рукоятку повертывают все время в одну сторону, причем ведомая шестерня и шпиндель вращаются попеременно то в одну, то в другую сторону. Достигается это тем, что две ведущие шестерни, вращаемые рукояткой, имеют по своей окружности неполное число зубьев (у одной шесть зубьев, у другой — девять), расположенных на противоположных сторонах. При вращении клапан прижимают к седлу, а при изменении направления вращения отпускают, причем клапан приподнимается от седла пружиной. В процессе притирки необходимо добавлять пасту.
- Конец притирки определяют появлением на рабочей фаске ровного матово-серого кольца без пятен.
- Герметичность клапана проверяют специальным прибором (рис. а) под давлением воздуха. При проверке стакан прибора плотно прижимают к поверхности блока и резиновой грушей создают давление 0,6—0,7 ат. Если в течение 1/2 мин. давление по манометру не падает, — герметичность хорошая. Герметичность клапана проверяют и более простым прибором (рис. б), причем поверхность вокруг клапана вытирают и припудривают мелом. Прибор устанавливают на клапан, затем рукояткой плотно прижимают резиновый присос книзу и отпускают его. Если клапан хорошо притерт, то прибор прочно удерживается на поверхности блока (прибор слегка покачивают рукой за головку).При недостаточной герметичности прибор держаться не будет. При наличии глубоких раковин и рисок рабочую фаску клапана сначала прошлифовывают, а затем только притирают. Шлифование фаски клапана выполняют на приборах с ручным или электроприводом.Клапан закрепляют под определенным углом по отношению к шлифовальному камню (45 или 30°) в патроне прибора. При работе прибора шлифовальный камень вращается с числом оборотов 4000—5000 в минуту, а патрон с клапаном — 120—140 в минуту.Подача патрона с клапаном и бабки с камнем осуществляется рукоятками.
Рис. Приборы для проверки герметичности клапанов:
а — прибор с манометром; б — прибор с присосом; 1 — резиновая груша; 2 — манометр; 3 — стакан; 4 — головка; 5 — резиновый присос.
Изношенные головки клапанов восстанавливают до нормального размера путем их раздачи, при этом головку клапана нагревают до 900—1000°, устанавливают клапан в матрицу и оправкой под прессом или ударами молотка производят раздачу. Затем головка подвергается механической обработке способами, указанными выше. Клапаны, головки которых имеют коробление, заменяют новыми.
Погнутые стержни клапанов выправляют под прессом, а затем проверяют индикатором на биение в центрах. Биение стержня не должно превышать 0,03 мм.
Рис. Прибор для шлифования клапанов с электроприводом:
1 — рукоятка для подвода клапана к шлифовальному камню; 2 — патрон для закрепления клапана; 3 — клапан; 4 — шлифовальный камень; 5 — подвижная шлифовальная бабка; 6 — электродвигатель; 7 — рукоятка для осевого перемещения бабки.
Рис. Матрица и оправка для раздачи головки клапана.
Изношенные стержни клапанов шлифуют под ремонтный размер или восстанавливают до номинального или ремонтного размеров хромированием.
Изношенный торец стержня при регулируемых клапанах шлифуют до получения гладкой поверхности, а при нерегулируемых клапанах (автомобиль ГАЗ-MM) торец наплавляют сталью от старого клапана и затем обрабатывают до требуемого размера. При наплавке во избежание коробления стержня клапан помещают в ванну с водой, оставляя на поверхности только торец высотой 20—25 мм.
Регулировка зазора между клапаном и толкателем
Для регулировки зазора необходимо:
- повернуть рукояткой коленчатый вал до полного закрытия регулируемого клапана;
- удерживать толкатель ключом в течение всей регулировки;
- отвернуть вторым ключом контргайку болта на 0,5—1 оборот и поворотом регулировочного болта установить зазор, в котором вставленный щуп соответствующей толщины будет проходить с небольшим усилием;
- завернуть контргайку, повернуть коленчатый вал на два оборота и щупом снова проверить правильность зазора.
В такой последовательности надо регулировать и остальные клапаны.
В двигателях автомобилей ГАЗ-MM зазор при эксплуатации не регулируют, а устанавливают при ремонте, удлиняя стержень клапана (для уменьшения зазора) в холодном состоянии на оправке или подпиливая торец стержня (для увеличения зазора).
Ремонт толкателей
К основным дефектам толкателей относится износ стержня и торцевой поверхности тарелки. Стержень толкателя восстанавливают шлифованием его на меньший ремонтный размер. Шлифуют стержни на токарном станке с супортно-шлифовальным приспособлением или на круглошлифовальном станке. При небольшом износе торцевой поверхности тарелки ее шлифуют, а при значительном износе поверхность тарелки наплавляют металлом газовой или электродуговой сваркой. Во избежание отпуска наплавку делают опуская стержень в водяную ванну.
В качестве присадочного материала можно использовать старые клапанные пружины.
После наплавки, не давая остыть металлу, толкатель быстро опускают в ванну с холодной водой и закаливают наплавленную поверхность. После закалки плоскость обрабатывают на наждачном точиле, а затем шлифуют на станке.
Технология и ремонт грм
Основными дефектами распределительного вала являются изгиб, износ опорных шеек и шейки под распределительную шестерню, износ кулачков. Биение промежуточных опорных шеек проверяют при установке вала в призмы на крайние опорные шейки. Допустимое биение определено техническими условиями. Если биение превышает допустимое значение, то вал правят под прессом. Изношенные шейки шлифуют на меньший диаметр до одного из ремонтных размеров. После шлифования на меньший диаметр до одного из ремонтных размеров. После шлифования шейки полируют абразивной лентой или пастой ГОИ. При этом осуществляют замену изношенных опорных втулок на новые. Внутренние диаметры новых запрессованных втулок обрабатывают разверткой или расточкой резцом под размер перешлифованных шеек распределительного вала. Опорные шейки вала, вышедшие из ремонтных размеров, можно восстанавливать хромированием или осталиванием под номинальный или ремонтный размер.
Небольшой износ кулачков устраняют шлифованием на копировально-шлифовальном станке. При значительном износе вершину кулачка можно восстановить наплавкой сормайтом N 1 с последующим предварительным шлифованием на электрошлифовальной установке и окончательной обработкой на копировально-шлифовальном станке.
Наиболее часто встречающимися дефектами к л а п а н о в являются износ и обгорание рабочей фаски, деформации тарелки (головки), износ и изгиб стержня. Клапаны с небольшим износом рабочей фаски восстанавливают притиркой к седлу. При значительных износах или наличии глубоких раковин и рисок осуществляют шлифование и притирку. После шлифования фаски высота цилиндрической части головки клапана должна быть не менее установленной техническими условиями.
Изношенный стержень клапана можно восстановить хромированием или осталиванием с последующим шлифование до номинального размера. Изношенный торец стержня клапана шлифуют до получения гладкой поверхности. У т о л к а т е л е й к л а п а н о визнашиваются сферическая и цилиндрическая поверхности.
При текущем ремонте двигателя притирают клапаны к рабочим фаскам седел, если на рабочих фасках клапанов и седел имеются незначильные повреждения. Точечные раковины, риски и другие повреждения на рабочих фасках клапанов и седел устраняют шлифованием с последующей притиркой. После шлифования рабочей фаски высота цилиндрической части головки клапана должна быть не менее 0,5 мм. Изношенные клапанные гнезда восстанавливаются шлифованием, зенкованием и запрессовкой новых колец
Отремонтированные клапаны притирают к седлам специальными пастами: смеси абразивного микропорошка с маслом двигателя. Каждая паста имеет свой номер. Грубые пасты от 18 до 40 номера имеют светло-зеленый цвет; средние пасты от 8 до 17 номера темиозеленый цвет, тонкие пасты от 1 до 7 номера — черный цвет с зеленоватым оттенком.
Тонкий слой пасты наносят на фаску клапана, стержень клапана смазывают чистым моторным маслом. Процесс притирки считается законченным, если поясок клапана и его седла имеют ширину не менее 1,5 мм по всей окружности матового цвета.
После окончания притирки клапаны промывают в керосине и продувают сжатым воздухом. Головку цилиндров моют в керосине, предварительно закрыв отверстия втулок тампонами.
Качество притирки можно проверить по карандашным полоскам или специальным прибором. В первом случае на рабочую поверхность фаски клапана карандашом наносят полосы, после чего устанавливают клапан в седло, прижимают и поворачивают его на 1/4 оборота. Если карандашные пометки исчезнут, то клапан притерт хорошо.
Сборка газораспределительного механизма.
Перед установкой распределительного вала тщательно проверяют его состояние. Внешним осмотром проверяют, нет ли задиров на поверхности кулачков, шеек и эксцентрика. При наличии задиров на кулачках распределительный вал заменяют. Для проверки прямолинейности вала его устанавливают крайними опорами на призмы и проверяют индикатором биение средней шейки вала. При увеличенном биении шейки валподлежит правке.
Распределительный вал перед установкой в блок протирают салфеткой и покрывают моторным маслом. При установке особое внимание обращают на совмещение меток, расположенных на торцах шестерен газораспределения.
Снятие и установке головки цилиндров на автомобиле ВАЗ2115-14.
Головку цилиндров снимают с двигателя на автомобиле, если для устранения неисправности не требуется разбирать весь двигатель. Например, если необходимо удалить нагар с поверхности камер сгорания и клапанов или заменть клапаны или направляющие втулки клапанов.
Снимают головку цилиндров в следующем порядке:
— устанавливают автомобиль на подъёмник и убирают давление в системе подачи топлива. Для этого отсоединяют колодку жгута проводов системы зажигания, запускают двигатель, дают ему поработать до остановки, а затем включают стартер на 3 с для выравнивания давления в трубопроводах;
— отсоединяют провод от клеммы «минус» аккумуляторной батареи;
— поднимают автомобиль и сливают охлаждающую жидкость из радиатора и блока цилиндров, для чего открывают кран отопителя т отворачивают сливные пробки на радиаторе и блоке цилиндров;
— отсоединяют приёмную трубу глушителей от выпускного коллектора, снимают кронштейн подводящей трубы насоса охлаждающей жидкости и поддерживающие кронштейны впускной трубы;
— опускают автомобиль, отсоединяют шланги подвода и слива топлива от трубок на двигателе. Закрывают отверстия шлангов и трубок, чтобы в них не попала грязь;
— отсоединяют трос привода акселератора от дроссельного патрубка и от кронштейна на ресивере;
— снимают шланги вытяжной вентиляции картера, отсоединив их от патрубков на крышке головки цилиндров, от шланга впускной трубы и от дроссельного патрубка;
— ослабляют стяжные хомуты и отсоединяют от дроссельного патрубка шланг впускной трубы, шланг продувки адсорбера (если на автомобиле имеется система улавливания паров бензина), шланги подвода и отвода охлаждающей жидкости;
— отсоединяют от ресивера шланг отбора разрежения к вакуумному усилителю тормозов;
— отсоединяют провода от свечей зажигания, от датчиков контрольной лампы давления масла и указателя температуры охлаждающей жидкости, от дроссельного патрубка и от датчика температуры на отводящем патрубке рубашки охлаждения; отсоединяют провода от жгута проводов форсунок;
— отсоединяют шланги от отводящего патрубка рубашки охлаждения двигателя;
— снимают переднюю защитную крышку зубчатого ремня и крышку головки цилиндров;
— устанавливают рычаг переключения передач в нейтральное положение и поворачивают по часовой стрелке коленчатый вал в такое положение, чтобы метка на маховике, видимая в люке картера сцепления, находилась против среднего деления шкалы. При этом метка на шкиве распределительного вала должна находиться против установочной метки на задней крышке зубчатого ремня;
— отворачивают гайку крепления натяжного ролика и снимают его вместе с дистанционной шайбой, снимают ремень со шкива распределительного вала;
— придерживают шкив распределительного вала от проворачивания приспособлением 67.7811.9509, отворачивают болт крепления и снимают шкив со шпонкой;
— отворачивают гайку крепления задней крышки зубчатого ремня к головке цилиндров;
— отворачивают болты крепления и снимают головку цилиндров с прокладкой.
Устанавливают головку цилиндров в порядке, обратном снятию. Прокладку между головкой и блоком цилиндров повторно применять не допускается, поэтому заменяют её новой.
Если болты крепления головки цилиндров вытянулись и их длина превышает 135,5 мм, то заменяют болты новыми. Болты затягивают в четыре приёма.
После установки головки цилиндров регулирую натяжение ремня и привод акселератора. Проверяют и при необходимости регулируют зазоры в клапанном механизме. Проверяют работу системы управления двигателем.
Разборка и сборка головки цилиндров.
Разборка. Если требуется замена только какой-либо одной детали, то можно не разбирать полностью головку цилиндров и снять только то, что необходимо для замены.
Устанавливают головку цилиндров на подставку, снимают ресивер с дроссельным патрубком, а затем жгут проводов форсунок, топливную рампу, впускную трубу и выпускной коллектор.
Снимают отводящий патрубок рубашки охлаждения двигателя с датчиком температуры. Выворачивают датчик указателя температуры охлаждающей жидкости, датчик контрольной лампы давления масла и свечи зажигания.
Снимают корпусы подшипников 3 и 6 (Приложение 6) распределительного вала. Вытаскивают распределительный вал 2 из опор головки цилиндров и снимите с него сальник 7.
Вытаскивают из отверстий головки цилиндров толкатели 11 (Приложение 7) клапанов с регулировочными шайбами 10. Освобождают клапаны от сухарей 9, сжимая пружины клапанов приспособлением 67.7823.9505 (Приложение 8). Снимаю пружины с тарелками. Поворачивают головку цилиндров и вытаскивают с нижней стороны клапаны. Снимают маслоотражательные колпачки с направляющих втулок и опорные шайбы пружин.
Сборка. Устанавливают опорные шайбы пружин. Смазывают моторным маслом клапаны и новые маслоотражательные колпачки. Вставляют клапаны в направляющие втулки, устанавливают пружины и тарелки пружин. Сжимая пружины приспособлением 67.7823.9505, устанавливают сухари клапанов. Вставляют в отверстия головки цилиндров толкатели клапанов с регулировочными шайбами.
Очищают сопрягающиеся поверхности головки цилиндров и корпусов подшипников от остатков старой прокладки, грязи и масла. Ставят установочные втулки корпусов подшипников распределительного вала. Смазывают моторным маслом опорные шейки и кулачки распределительного вала и укладывают его в опоры головки цилиндров в таком положении, чтобы кулачки первого цилиндра были направлены вверх.
На поверхности головки цилиндров, сопрягающиеся с корпусами подшипников, в зоне крайних опор распределительного вала наносят герметик типа КЛТ-755ТМ или аналогичный ему герметик типа ТБ-1215. Устанавливают корпусы подшипников и затягивают гайки их крепления в два приема:
1. Предварительно затягивают гайки в последовательности, указанной в Приложении 9, до прилегания поверхностей корпусов подшипников к головке цилиндров, следя за тем, чтобы установочные втулки корпусов свободно вошли в свои гнёзда.
2. окончательно затягивают гайки в той же последовательности.
Немедленно после затяжки гаек крепления корпусов подшипников тщательно удаляют остатки герметика, выдавленного из зазоров при затяжке, в зонах, сопрягаемых с прокладкой крышки головки цилиндров и с корпусом вспомогательных агрегатов. Не удалённые полимиризовавшиеся остатки герметика в указанных местах приведут к течи масла через уплотнения.
Оправкой 67.7853.9580 запрессовывают новый сальник распределительного вала, предварительно смазав его моторным маслом. С задней стороны головки цилиндров устанавливают заглушку с прокладкой. Устанавливают отводящий патрубок рубашки охлаждения с прокладкой и датчиком температуры. Надевают на шпильки головки цилиндров прокладки и устанавливают выпускной коллектор и впускную трубу. Закрепляют их гайками вместе с кронштейном и экраном.
Устанавливают рампу форсунок с форсунками и регулятором давления топлива и прикрепляют её болтами к головке цилиндров. Уплотнительные кольца форсунок перед установкой смазывают моторным маслом. Устанавливают жгут проводов форсунок и подключают провода к форсункам. Устанавливают ресивер с прокладкой и кронштейном топливопроводов и прикрепляют его гайками к впускной трубе и кронштейну. Устанавливают вакуумный шланг, идущий от ресивера к регулятору давления топлива. Устанавливают трубки подвода и слива топлива., прикрепив их к топливной рампе, к регулятору давления топлива и к кронштейну на ресивере.
Прикрепляют к ресиверу дроссельный патрубок с прокладкой. Присоединяют к дроссельному патрубку шланг вытяжной вентиляции картера на холостом ходу. Заворачивают в головку цилиндров свечи зажигания и датчики указателя температуры охлаждающей жидкости и контрольной лампы давления масла. Зазоры в клапанном механизме регулируют после установки головки цилиндров на двигатель.
Замена ремня привода распределительного вала.
Затормозить автомобиль рычагом привода стояночной системы и включить 4 или 5 передачу в коробке передач. Снять переднюю крышку зубчатого ремня. Ослабить ремень привода генератора и снять его со шкивов. Снять шкив привода генератора с коленчатого вала и завернуть на место болт крепления шкива.
Установить рычаг коробки передач в нейтральное положение и повернуть коленчатый вал по часовой стрелке в такое положение, чтобы метка на маховике, видимая в люке кожуха сцепления, находилась против среднего деления шкалы. При этом метка В(Приложение 2) на шкиве распределительного вала должна находиться против установочной метки А на задней защитной крышке. Ослабить гайку крепления натяжного ролика 3 и повернуть его в такое положение, при котором ремень будет максимально ослаблен. Снять ремень привода распределительного вала со шкивов.
Надеть зубчатый ремень на шкив 5 распределительного вала и, натягивая обе ветви ремня, завести левую ветвь за натяжной ролик и надеть её шкив 2 насоса охлаждающей жидкости. Надеть ремень на шкив коленчатого вала и слегка натянуть его натяжным ремнём, поворачивая ролик против часовой стрелки. При установке ремня надо избегать его резких перегибов. Провернуть коленчатый вал на два оборота по часовой стрелке и проверить, совпадают ли установочные метки А и В (Приложение 2), а также находится ли метка на маховике против среднего деления шкалы.
Если мети не совпадают, то повторить операцию по установке ремня. Если метки совпадают, то вывернуть болт из коленчатого вала, установить шкив привода генератора и закрепить его болтом с шайбой. Отрегулировать натяжение ремня и установить переднюю защитную крышку зубчатого ремня. Надеть ремень привода генератора и отрегулировать его натяжение.
Ремонт ГРМ
Газораспределительный механизм (ГРМ) является наиболее важным механизмом в двигателе вашего автомобиля. Как и все узлы авто, ГРМ требует периодического обслуживания. Несвоевременная регулировка или замена деталей, могут привести к капитальному ремонту всего двигателя.
Основными неисправностями газораспределительного механизма являются:
-нарушения тепловых зазоров клапанов;
-вытягивание зубчатого ремня, износ зубчатых шкивов;
-износ цепи и звездочек привода;
-ослабление креплений крышек подшипников распределительного вала, неплотное закрытие клапанов из-за изнашивания их головок и седел;
-снижение упругости клапанных пружин, износ подшипников, шеек и кулачков распределительного вала, толкателей, поршней и их осей, втулок и седел клапанов.
В результате нарушения регулировок и износа деталей газораспределительного механизма появляется шум при работе двигателя, он теряет мощность, идет повышенный расход масла и топлива. После комплексной диагностики ГРМ мы определим необходимость ремонта или регулировки механизма газораспределения.
Распределительный вал и его привод.
Основными неисправностями являются износ опорных шеек вала, износ и задиры кулачков и изгиб вала. Эти повреждения вызывают стуки в клапанном механизме, а увеличение зазоров в подшипниках приводит к падению давления масла в системе смазывания.
Для восстановления зазоров в подшипниках распределительного вала восстанавливают, шлифуют его опорные шейки, прочищают канавки для нормальной подачи масла к деталям двигателя. Шейки вала шлифуют под ближайший ремонтный размер. После шлифования их полируют пастой.
При небольшом износе кулачков распределительного вала их зачищают шлифовальной шкуркой, сначала крупнозернистой, затем мелкозернистой. Если кулачки распределительного вала изношены по высоте, их шлифуют на специальном копировально-шлифовальном станке для распределительных валов. Кулачки вала, имеющие значительный износ, можно восстановить наплавкой с последующим шлифованием.
При износе кулачков по высоте более чем на 0,5 мм по сравнению с номинальной высотой вал заменяют, так как при таком износе ухудшается наполнение цилиндров, в результате чего мощность двигателя падает.
Изгиб распределительного вала измеряют специальным индикатором и проверяют по средней шейке. Допустимый изгиб может быть не более 0,10 мм. Если он больше, нужно вал править.
Регулировка цепи привода распределительного вала, возможна при растяжении не более 4 мм. Цепь не должна иметь сколов и трещин. Чрезмерно растянутая цепь может привести к перескоку, и вследствие встречи клапанов с поршнями.
Периодически требуется регулировка тепловых зазоров в приводе клапанов. Это обеспечит эффективную работу и долговечность двигателя. Тепловой зазор в клапанном механизме обеспечивает плотную посадку клапана на седло и компенсирует при работе двигателя тепловое расширение деталей механизма. При увеличенном тепловом зазоре появляется частый металлический стук клапанов, который хорошо прослушивается при малой частоте вращения на холостом ходу. При этом быстро изнашиваются торцы стержней клапанов, наконечников стержней или регулировочных шайб, происходит падение мощности двигателя. Причиной является сокращение времени нахождения клапанов в открытом положении, и как следствие – ухудшение наполнения топливом и очистка цилиндров от отработанных газов.
Чтобы избежать этих неисправностей, необходимо проверять и своевременно регулировать тепловые зазоры, а при износах клапанов и седел притирать их к седлам или заменять. Регулировку тепловых зазоров можно выполнять только на холодном двигателе при температуре охлаждающей жидкости в системе охлаждения двигателя 15–25 °C. При достижении нормального теплового режима на работающем двигателе при температуре охлаждающей жидкости в рубашке головки блока цилиндров 80 °C зазоры станут нормальными.
В связи с сложностью работ и необходимостью наличия навыков по ремонту ГРМ, будет лучше обратится к нам в сервис. Наши сертифицированные специалисты, сделают все работы качественно и недорого. На все работы предоставляются гарантии.
Наименование работ | Цены |
Ремень ГРМ замена (снятие установка) | 1000 р. |
Сальник распредвала замена | 300 р. |
Датчик распредвала, замена | 300 р. |
Регулировка клапанов | 600 р. |
Ремонт деталей газораспределительного механизма — Техническое Обслуживание и Ремонт Автомобилей
§ 55. Ремонт деталей газораспределительного механизма
Ремонт распределительного вала.
Основными дефектами распределительного вала являются: изгиб, износ опорных шеек и шейки под распределительную шестерню, износ кулачков.
Биение промежуточных опорных шеек проверяют при установке вала в призмы на крайние опорные шейки. Допустимая величина биения устанавливается техническими условиями. Если биение превышает допустимую величину, то вал правят под прессом. Изношенные шейки шлифуют на меньший диаметр до одного из ремонтных размеров. После шлифования шейки полируют абразивной лентой или пастой’ ГОИ. При этом осуществляют замену изношенных опорных втулок на новые. Внутренние диаметры новых запрессованных втулок обрабатывают разверткой или расточкой резцом под размер перешлифованных шеек распределительного вала. Опорные шейки вала, вышедшие из ремонтных размеров, можно вос-
станавливать хромированием или осталиванием под номинальный или ремонтный размеры. Небольшой износ кулачков устраняют шлифованием на копировально-шлифовальном станке. При значительном износе вершину кулачка можно восстановить наплавкой сормайтом № 1 с последующим предварительным шлифованием на электрошлифовальной установке и окончательной обработкой на копировально-шлифовальном станке.
Ремонт клапанов, толкателей, коромысел.
Наиболее часто встречающимися дефектами клапанов являются: износ и обгорание рабочей фаски, деформации тарелки (головки), износ и изгиб стержня. Клапаны с небольшим износом рабочей фаски восстанавливают притиркой к седлу. При значительных износах или наличии глубоких раковин и рисок осуществляют шлифование и притирку. После шлифования фаски высота цилиндрической части головки клапана должна быть не менее величины, установленной техническими условиями.
Все клапаны притирают одновременно на специальном станке. Герметичность пары клапан— седло контролируют прибором, при помощи которого нагнетается под избыточным давлением (0,6—0,7 кгс/см2) воздух. Давление в течение 1 мин не должно резко уменьшаться.
Изгиб стержня и биение рабочей фаски головки относительно стержня проверяют на специальном приспособлении (рис. 82). Контроль осуществляют индикаторами 10 и 11. Допускаемое биение стержня клапана — 0,015 мм на длине 100 мм, а биение рабочей фаски — 0,03. При большем биении стержень клапана правят.
Изношенный стержень клапана можно восстановить хромированием или осталиванием с последующим шлифованием до номинального размера. Изношенный торец стержня клапана шлифуют до получения гладкой поверхности.
У толкателей клапанов изнашиваются сферическая и цилиндрическая поверхности. Стержень восстанавливают шлифованием до ремонтного размера или хромированием. При этом отверстие у направляющих толкателей обрабатывают разверткой под размер устанавливаемых стержней или для запрессовки втулки. Втулки изготавливают из серого чугуна и запрессовывают с натягом 0,02—0,03 мм. После запрессовки внутренний . диаметр втулок обрабатывают разверткой, обеспечивая необходимый зазор в соединении. Износ сферической поверхности стержня устраняют шлифованием по шаблону, выдерживая установленную техническими условиями высоту.
В коромысле клапанов изнашиваются втулки, которые заменяют на новые и растачивают отверстие в них до номинального или ремонтного размера. В новой втулке сверлят масляные отверстия. Изношенную сферическую поверхность носка коромысла обрабатывают шлифованием.
Ремонт ГРМ: технологический процесс обслуживания автомобиля
Основным условием работы двигателя внутреннего сгорания является наличие системы газораспределения. В народе механизм называют ГРМ. Этот узел должен регулярно обслуживаться, что строго регламентировано заводом-изготовителем. Несоблюдение сроков по замене основных компонентов может повлечь за собой не только ремонт ГРМ, но и двигателя в целом.
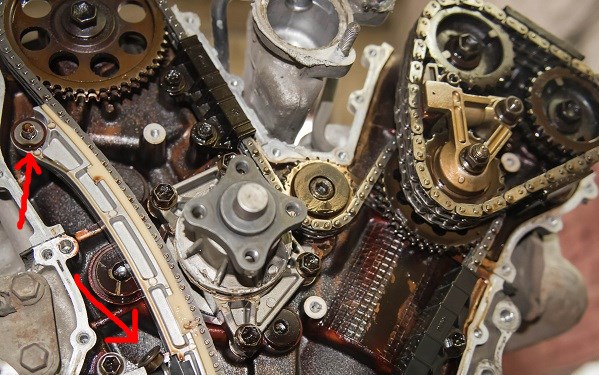
Ременной привод газораспределительного механизма
В настоящее время существует два варианта реализации привода ГРМ: ременной и цепной. Первый считается более распространенным и простым в обслуживании. Система насчитывает несколько шкивов, установленных на распределительных и коленчатом валах, а также водяной насос. Механизм также включает в себя систему натяжения и обводной (паразитный) ролик. Дополнительные натяжители нужны для того, чтобы ремень работал строго на своем месте без перекоса. Ролики – это, по сути, подшипники качения, которые периодически тоже необходимо менять.
Стоит понимать, что ремонт ремня ГРМ как таковой не выполняется. Последний подлежит только замене. Что касается регламентных сроков замены механизма, то все зависит от завода изготовителя. В большинстве случаев ремень ГРМ меняют каждые 150 тысяч километров, но в тяжелых условиях эксплуатации, к которым можно смело отнести пробег машины по территории РФ, необходимо проводить замену каждые 90-100 тысяч километров. Ремонт ремня ГРМ и других составляющих не рекомендуется делать еще по той причине, что обслуживание газораспределительного механизма довольно дорогое, особенно это касается двигателей V6 и V8. Так как ремонтные работы не дают никаких гарантий по сроку службы, то можно попасть на внеплановую замену. Комплект замены: ремень, обводной и ведущий ролик, водяной насос и сальники.
Вкратце о цепном приводе
Основная цель инженеров заключается в том, чтобы обеспечить максимальный ресурс силового агрегата автомобиля. А так как обрыв ремня ГРМ в большинстве случаев приводит к фатальным последствиям, то много внимания было уделено надежности узла. В этом плане цепной привод оказался впереди ременного. Практически всегда применяется двухрядный цепной привод, который входит в зацепление с соответствующими звездочками, установленными на валах (распределительном и коленчатом).
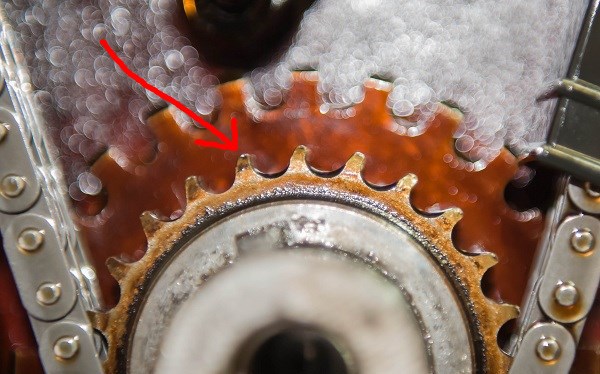
Основная проблема цепи заключается в том, что со временем она растягивается. В результате этого нередко появляются посторонние шумы и сбиваются метки ГРМ. Из-за этого двигатель теряет часть мощности и повышается его износ. Ремонт цепи ГРМ, равно как и ремня, не выполняется. Замене подлежит полностью весь узел, начиная от звездочек и заканчивая цепью и успокоителем с натяжителем. Что касается основных достоинств цепного привода, то это его надежность и интервалы замены. Его необходимо менять несколько реже, примерно каждые 250 тысяч километров. Если этого не делать вовремя, то может случиться обрыв цепи ГРМ. Ремонт мотора после такой поломки будет стоить достаточно дорого.
Принцип действия ГРМ
Независимо от типа привода, газораспределительный механизм работает по одной и той же схеме. Всю работу можно разделить на 4 основных этапа:
- впуск;
- сжатие;
- рабочий ход;
- выпуск.
Чтобы эта система работала исправно и эффективно, необходимо синхронизировать работу распределительных и коленчатого вала. Синхронная работа распредвала и коленвала — основная задача привода ГРМ независимо от его типа и устройства.
Такт впуска начинается с движения коленчатого вала. Он передает усилие на поршень, который, в свою очередь, начинает движение из верхней мертвой точки (ВМТ) в нижнюю мертвую точку (НМТ). В это время происходит открытия впускных клапанов и поступление топливно-воздушной смеси в камеру сгорания. После подачи клапана закрываются. Коленчатый вал за этот такт проворачивается на 180 градусов от своего начального положения.
После того как поршень достиг НМТ, он начинает подниматься в ВМТ. Следовательно, в цилиндре происходит сжатие топливно-воздушной смеси. Фаза заканчивается при подходе поршня к верхней мертвой точке. Коленчатый вал в конце такта провернут на 360 градусов от своего начального положения.
Когда наступает момент максимального сжатия, происходит воспламенения топливной смеси, а поршень в это время под действием образовавшихся газов начинает двигаться к НМТ. Когда он достигает нижней точки, то фазу рабочего хода принято считать завершенной. Удаление отработанных газов происходит при последующем движении поршня в ВМТ и открытии выпускных клапанов. После завершения такта коленчатый вал проворачивается на 720 градусов от своего начального положения.
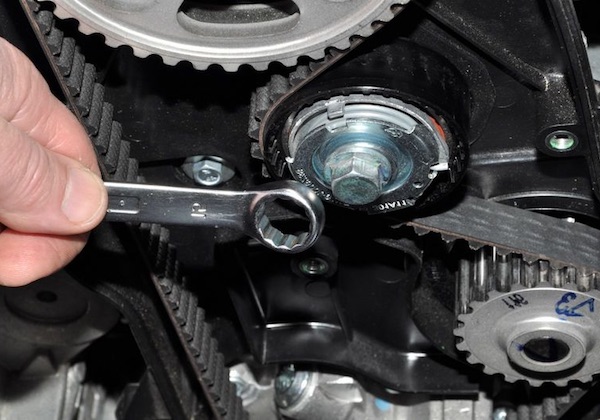
Основные элементы газораспределительного механизма
ГРМ состоит из большого количества деталей, каждая из которых выполняет возложенную на нее задачу. Основной элемент — распределительный вал. В большинстве случаев устанавливается в головке блока цилиндров. Современные моторы оснащаются двумя распредвалами, что повышает эффективность работы системы в целом и ее надежность. В этом случае мотор будет иметь 16 клапанов, а с одним распредвалом — 8. При вращении вала происходит воздействие на клапана через кулачки, установленные на цилиндрических шейках. Промежуточное звено между кулачками и клапанами — толкатели.
Еще одна важная составляющая — впускные и выпускные клапана. Они нужны для подачи топливно-воздушной смеси и удаления отработанных газов. Представляют собой стержень с тарелкой. Стержень всегда цилиндрической формы с выборкой под пружину. Движение клапанов строго ограничено. Для предотвращения попадания масла в камеру сгорания через клапана, последние имеют уплотнительные кольца.
Еще один элемент — привод ГРМ. Через него передается вращение. Стоит понимать, что за 2 полных оборота коленчатого вала, распределительный делает всего один. То есть, вращается со скоростью в два раза меньшей.
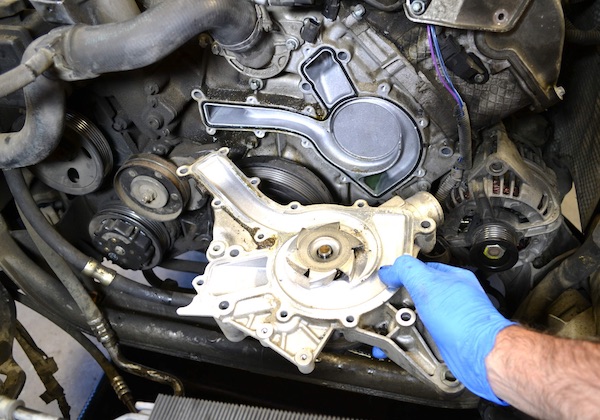
Ремонт и обслуживание ГРМ
Чем плотнее компоновка узлов и агрегатов под капотом, тем сложнее заменить ту или иную деталь газораспределительного механизма. Именно поэтому плановый ремонт необходимо выполнять полностью, а не менять только ремень или помпу. Ведь если выйдет из строя ролик ГРМ, ремонт обойдется в круглую сумму, которую можно приравнять к полному обслуживанию механизма. Как уже было отмечено выше, производителем указаны четкие сроки замены комплекта газораспределительного механизма. Их и нужно стараться придерживать. Безусловно, изначально инженерами заложен небольшой запас прочности узла. К примеру, с ремнем или цепью может ничего и не случится, если ее заменить несколько позже. Но затягивать с этим не стоит, ведь обрыв в большинстве случаев приводит к тому, что клапана встречаются с поршнями и их загибает. Для ремонта понадобится снимать и разбирать мотор, а это уже полноценная капиталка.
Желательно обслуживать ГРМ у хороших специалистов, хотя порой найти таковых довольно сложно. Дело в том, что процесс настройки включает в себя выставление меток. Если не синхронизировать распределительные валы с коленчатым, то машина вообще не заведется. Нужно будет опять разбирать узел, и делать все по новой. Желательно при ремонте не менять сальники валов, которые имеют свойство подтекать.
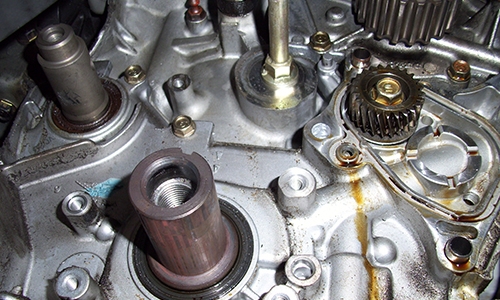
Основные неисправности ГРМ
Даже если привод газораспределительного механизма находится в хорошем состоянии, то это еще не гарант нормальной работы узла. Дело в том, что в процессе эксплуатации на клапанах появляется нагар и раковины. Из-за этого клапана прилегают к седлам неплотно, и могут быть слышны хлопки в выхлопной системе, а также несколько уменьшается компрессия. Нередки случаи деформации головки блока цилиндров, уменьшение зазоров между клапанами и седлами, а также заедание стержня клапана во втулке.
Вторая популярная неисправность — уменьшение мощности силового агрегата. В большинстве случаев причиной является неполное закрытие впускных клапанов. В результате этого часть топливно-воздушной смеси не попадает в камеру сгорания. Увеличивается тепловой зазор, и выходят из строя гидрокомпенсаторы. Обычно мотор начинает троить, и появляются посторонние стуки металлического характера.
Еще одна типичная проблема — механический износ. Нередко бывает так, что просто взял и порвался ремень ГРМ. Ремонт в этом случае понадобится внеплановый. Из-за чего это может произойти? Все предельно просто — критический износ шестеренок или подшипников. Они разбалтываются или вовсе заклинивают. Но даже в этом случае обрыв зачастую происходит не сразу. Да и изменения в работе двигателя сложно не заметить. Поэтому шуршащие или свистящие звуки в районе газораспределительного механизма желательно устранять сразу.
ГРМ: ремонт «Рено» и других автомобилей
В большинстве случаев, процедура замены газораспределительного механизма на всех автомобилях практически идентична. Речь идет о моторах с рядным расположением цилиндров. Если у вас V6 и выше, то выполнить самостоятельную замену будет на порядок сложнее.
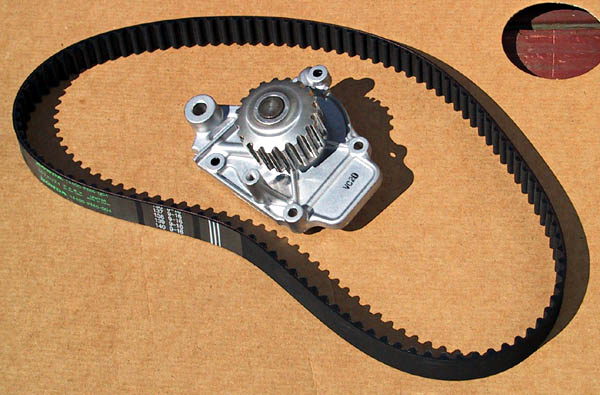
Возьмем в качестве примера автомобиль «Рено Сценик» с силовым агрегатом типа К4М. На нем многие водители рекомендуют менять ГРМ не реже чем каждые 80 тысяч километров. Если с разборкой все более или менее понятно, то при сборке узла очень важно правильно выставить метки. Чтобы это сделать, необходимо продублировать метки со старого ремня и желательно начать установку с распределительного вала. Дальше ремень прокидывается через обводной и натяжной ролик с помпой. Если фазорегулятор снят, то, скинув ремень с помпы, его необходимо установить. Для удобства монтажа многие водители снимают шестерню коленчатого вала и устанавливают ее в последнюю очередь. Ремонт ГРМ 16-клапанного мотора имеет лишь то отличие, что необходимо синхронизировать два распределительных вала. Сделать это просто, ведь на каждом из них имеются соответствующие метки. Аналогично проходит замена и на автомобилях ВАЗ, независимо от мотора. Самостоятельно провести такой ремонт возможно только при наличии специального инструмента и оборудования. Хотя кто-то способен и «на коленке» отремонтировать привод.
Процесс ремонта узла
Многие покупают автомобили с пробегом. Практически все владельцы перед продажей говорят о том, что комплект ГРМ менялся совсем недавно. Хорошо, если это действительно так. Ведь обрыв может привести к капиталке, которая обычно составляет порядка 20% стоимости автомобиля или даже больше. Чтобы в дальнейшем не выполнять ремонт клапанов ГРМ, желательно сделать диагностику узла и принять соответствующее решение. В большинстве случаев не рекомендуется оставлять какую-либо деталь, заменив все остальные. Как уже было сказано выше, выход из строя водяного насоса или ролика, приведет к повторному ремонту. Хорошо еще, если удастся избежать обрыва ремня.
Есть такой вид работ, как «дефектовка ГРМ». Суть мероприятия заключается в выявлении проблем в работе привода газораспределительного механизма. По сути, работа включает в себя осмотр узла и оценку состояния ремней, роликов, водяного насоса и т. п. Также при дефектовке проверяют метки ГРМ и при необходимости их выставляют. Необходимо понимать, что многое зависит от того, насколько квалифицированными сотрудниками был проведен ремонт ГРМ автомобиля. Ведь если механики на СТО недостаточно хорошо знакомы с конструкцией и устройством газораспределительного механизма того или иного автомобиля, то лучше воспользоваться услугами другого сервиса.
Правильный выбор запасных частей
Как показывает практика, наиболее часто вызывает проблему при капитальном ремонте двигателя ГРМ. Причем далеко не всегда она кроется в несвоевременном обслуживании. В некоторых случаях все дело в запчастях. Дело в том, что есть оригинальные ремни, ролики и водяные насосы. Под словом «оригинальные» стоит понимать те запасные части, которые были установлены заводом изготовителем. В большинстве случаев они имеют достаточно длительный ресурс и хороший запас прочности при правильной эксплуатации и обслуживании. К примеру, водяная помпа рассчитана в среднем на 150 тысяч пробега. Такой интервал выдерживают абсолютно все детали, начиная от обводных роликов и заканчивая ремнем или же цепью. Но даже при приближении такого пробега, ГРМ может работать вполне нормально еще 30 или 50 тысяч километров. Но уже нет никакой гарантии, что его не оборвет в самый неподходящий момент. Тем не менее определенный запас производителем все же заложен.
Ну а сейчас следующая ситуация. Оригинальные детали на большую часть автомобилей стоят приличных денег. Исключением являются только некоторые автомобили семейства ВАЗ. Ремонт ГРМ «Жигулей» — не слишком затратное и сложное мероприятие. Ну а если под капотом 5-литровый монстр, то покупка оригиналов ГРМ на него обойдется не в одну сотню долларов. Вполне естественно, что автомобилисты хотят сэкономить, приобретая аналоги не самого лучшего качества. В результате уже через 10-20 тысяч километров появляется люфт в подшипниках, начинает подтекать помпа и т. п. Водитель в этом случае вынужден повторно менять детали ГРМ, что приводит к неоправданным затратам. В худшем случае придется выполнять такие работы, как ремонт клапанов ГРМ, а точнее, их полную замену.
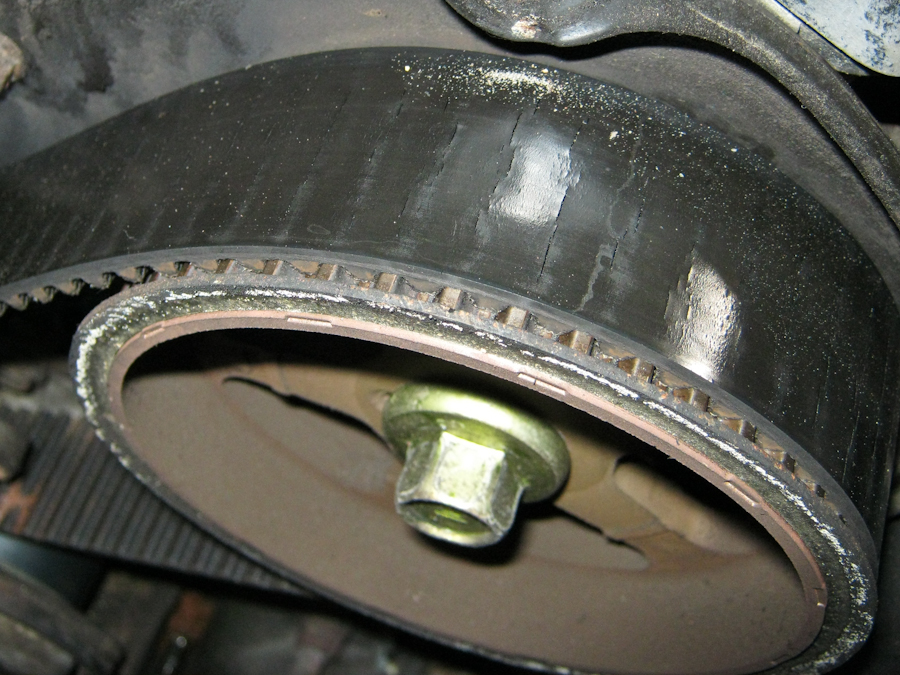
Подведем итоги
Газораспределительный механизм двигателя внутреннего сгорания требует регулярного и качественного технического обслуживания. В этом случае можно быть уверенным в его длительной бесперебойной работе. Некоторые двигатели не боятся обрыва ремня, и клапаны не загибает. Но даже в этом случае приятного мало, ведь найти ремень на трассе довольно проблематично.
Несмотря на все вышесказанное, не нужно относиться к ГРМ как к чему-то особенному. Механизм попросту нуждается в замене по регламентным срокам, которые указаны в сервисной книжке. Также не стоит пытаться экономить на запасных частях, устанавливая китайские дешевые подшипники и помпы непонятного производства. Также желательно следить за состоянием защитного кожуха механизма, ведь нередко его повреждение приводит к попаданию грязи и воды на ролики и ремень, что способствует сокращению ресурса. Если уж поломка и приключилась, то нужно найти специалистов, которые смогут качественно выполнить ремонт цепи ГРМ или же ремня.
Ремонт и техническое обслуживание механизма газораспределения
Проверка технического состояния механизма газораспределения заключается в оценке состояния его деталей. Состояние деталей оценивают по уровню шума и стукам, расходу сжатого воздуха, подаваемого в цилиндры, падению компрессии, по упругости клапанных пружин, а также по измерению изменений разряжения во впускном трубопроводе. По шуму и стуку определяют износ и растяжение цепи и звездочек привода газораспределительного механизма. Кроме того, шумы свидетельствуют об износе подшипников и опорных шеек распределительного вала, об увеличенном зазоре в клапанном механизме, который является следствием нарушения регулировки или износа деталей газораспределительного механизма.
На основании увеличенного расхода сжатого воздуха и падения компрессии устанавливают нарушение герметичности клапанов вследствие износа посадочных поверхностей их седел и головок. Расход сжатого воздуха определяется при помощи прибора К-69М. По причине того, что расход сжатого воздуха свидетельствует не только о неисправностях в газораспределительном механизме, но и о неисправности в кривошипно-шатунном механизме, для уточнения причин повышенного расхода воздуха проводят дополнительное измерение расхода сжатого воздуха после заливки в цилиндр небольшого количества моторного масла. Если при повторном измерении расход сжатого воздуха восстанавливается до требуемой величины, то это свидетельствует о том, что детали клапанного механизма находятся в удовлетворительном состоянии, если расход не восстанавливается, то необходимо произвести ремонт клапанного механизма.
По результатам измерений делается вывод о необходимости разборки и ремонта механизма газораспределения.
Проверку упругости пружин клапанов осуществляют без снятия их с двигателя. Для проверки пружин на двигателе нужно снять клапанную крышку, затем установить поршень цилиндра в ВМТ. После этого при помощи прибора КИ-723 измеряют усилие, которое необходимо для сжатия пружины. Если усилие окажется меньше допустимого, то необходимо произвести замену пружин. Кроме замены пружины в некоторых случаях под нижнюю опорную тарелку подкладывают дополнительную шайбу.
Для обеспечения эффективной работы двигателя необходимо проводить проверку и регулировку тепловых зазоров в приводе клапанов. При увеличенном тепловом зазоре появляется частый металлический стук клапанов, который отчетливо слышится при работе двигателя на холостом ходу. В результате этого происходит интенсивное изнашивание торцов стержней клапанов, наконечников стержней или регулировочных шайб. Кроме этого увеличенный тепловой зазор приводит к уменьшению мощности двигателя, так как уменьшается время нахождения клапанов в открытом положении, в результате этого ухудшается наполнение горючей смесью и очистка цилиндров от отработанных газов. При небольшом зазоре или при его отсутствии у выпускных клапанов появляются хлопки из глушителя, а у впускных клапанов — из карбюратора.
Для предотвращения перечисленных выше неисправностей необходимо периодически проверять и регулировать тепловые зазоры. Проверку и регулировку зазоров в приводе клапанов осуществляются на холодном двигателе, температура которого составляет 15-20 °С.
Кроме вышеперечисленных мероприятий необходимо ежедневно при контрольном осмотре автомобиля после прогрева двигателя обращать внимание на отсутствии стуков при различной частоте вращения коленчатого вала. После первых 2000 км пробега автомобиля, а в дальнейшем через 30 000 км нужно подтягивать гайки крепления крышки подшипников распределительного вала в установленной последовательности. После каждых 15 000 км пробега нужно проверять степень натяжения и состояние ремня привода распределительного вала и при необходимости натягивать его. Если на ремне обнаруживаются различные складки, трещины, расслоения, замасливания, а также разлохмачивания, то такой ремень может разорваться при работе двигателя, и он должен быть заменен до этого срока. При замасливании ремень тщательно протирают ветошью, которую предварительно смачивают бензином.
После каждых 30 000 км пробега необходимо проверять и при необходимости регулировать величину теплового зазора клапанов. При необходимости (при появлении частого металлического стука) проверку и регулировку величины теплового зазора клапана проводят раньше 30 000 км пробега. Кроме этого каждые 60 000 км пробега следует производить замену зубчатого ремня привода распределительного вала и маслоотражательных колпачков.