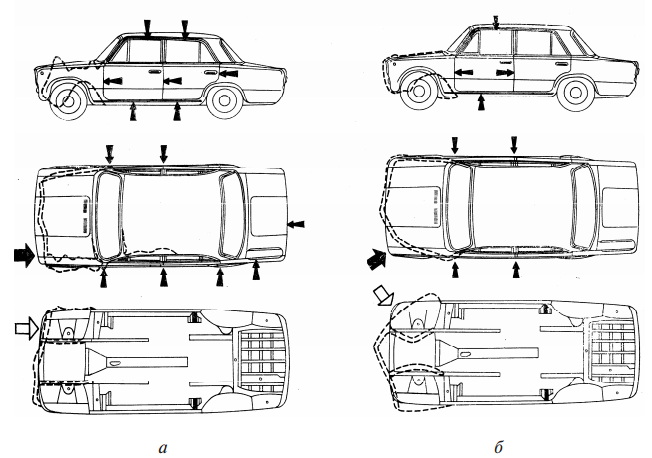
Основы кузовного ремонта – Восстановление геометрии кузова автомобиля, удаление, замена и ремонт кузовных деталей
- 24.01.2020
Как сделать качественный кузовной ремонт автомобиля полностью своими руками?
Кузовной ремонт автомобиля своими руками можно разделить на два этапа. Первый из них – рихтовка или выправление геометрии машины, кроме этого, устранение вмятин и удаление царапин. Второй этап – это перекраска кузова. Вследствие всего сказанного, такой ремонт является серьезным процессом, требующим правильной и точной работы. В данной статье мы расскажем о первом этапе восстановления кузова.
Определение степени повреждений
Для начала авто нужно обследовать, чтобы оценить степень повреждений. После этого необходимо выбрать одну из разновидностей ремонта.
- Когда повреждения не вызывают деформации подрамника и кузова, то производится лишь локальный ремонт обшивки машины.
- Если повреждения очень сильны и привели к искажению размеров меж точками фиксации механических узлов, то необходимо восстановление геометрических параметров всего кузова.
Любое восстановление авто должно в обязательном порядке сопровождаться контролем его геометрии. Для этого можно использовать шаблоны либо проводить компьютерные измерения размеров кузова.
Для локального ремонта поверхностей нужен ручной инструмент и редко – серьезная оснастка. Для восстановления геометрии авто необходимо сложное и дорогостоящее оборудование (стапели, подъемники и пр.), которое имеется, обычно, лишь на СТО.
Выправление формы кузова
Элементы кузова штампуются из листового металла. В материале под действием пресса возникают сжатия и растяжения, что ведет к относительному перемещению его молекул. В металле образуются напряжения, которые и удерживают форму детали.
Наружные элементы кузова, как правило, обладают выпуклой формой. При ударе такая поверхность сжавшись, выравнивается, потом становится вогнутой. Когда удар сильный, то металл вытягивается.
Вокруг деформированного участка образуется пояс, в котором металл наиболее вытянут. Эта граница часто формирует четко выраженную складку, мешающую восстанавливать форму поверхности. Поэтому изменять напряжения в металле можно не по всему поврежденному участку, а только в зоне удара. Зачастую форма кузова восстанавливается, когда разгружаются точки утяжки пояса, ограничивающего зону повреждения.
Перед тем, как сделать кузовной ремонт своими руками, в зоне повреждения снимите шабером краску и грунтовку. Далее, освободите места утяжек. Потом начинайте восстановление детали.
Когда вмятина большая, но неглубокая, она выправляется ударом рихтовочного молотка по ее вершине. Если деформация глубокая, ее надо выправлять постепенно, начиная работу от края. Под ремонтируемую поверхность, на ее границе, подставьте подходящее по форме наковало.
Когда в поврежденной зоне есть жесткие сечения (стойки, подкладки и пр.), в первую очередь исправляют эти элементы. Восстановление металла состоит из двух основных процессов: выколотки и рихтовки. Выколотка, по сути – черновое придание кузову изначальной формы.
Работать лучше всего деревянной киянкой. При обработке рихтовочным молотком рассчитывайте силу удара, иначе вы растянете металл, вместо его усаживания.
Если повреждение в форме пузыря небольшое, то достаточно просто нагреть эту точку. При этом операция завершается только тогда, когда металл полностью остынет. Чтобы ускорить охлаждение, используйте смоченную в воде ветошь или губку.
Когда нужны дополнительные точечные прогревы, делайте их не больше двух-трех и располагайте по кругу от центральной точки. После того, как металл остынет, произведите легкую рихтовку этого участка, чтобы окончательно выровнять поверхность.
Расположение и число точек нагревания зависят от размера и формы пузыря. Если он круглый, то точки прогрева размещаются по его радиусу. Когда пузырь тонкий и длинный, нагрев производят узкими рядами.
Выравнивание электронагревом
Точечная сварка без проблем нагревает металл. Данный факт использует технология кузовного ремонта автомобиля путем нагревания и выправления его поврежденных элементов при помощи аппаратов точечной сварки.
Общие принципы работы всего подобного оборудования заключены в быстром локальном разогреве металла, который находится в контакте с электродом угольного типа, вставленным в держатель. В зависимости от разновидности держателя и различной постановки электрода, сварка может производиться точками, прямыми и криволинейными строчками.
Для того, чтобы выправить дефект данным методом, необходимы подготовительные работы. Сначала деформированный участок выправляется обычными инструментами. Но, когда вмятина небольшая, то можно обойтись и без этого.
С поврежденного места убирается старая краска, которая является изолятором. Сделать это можно шлифмашинкой либо шабером. Точка соединения поверхности с массой хорошо зачищается.
Установите электрод в аппаратный держатель. При этом электрод, имеющий плоский либо выпуклый наконечник, используется для создания точек усадки. Аналог, обладающий острым наконечником необходим для усадочных строчек. Отрегулируйте далее на вторичной обмотке напряжение.
Для тонкого металла достаточна сила тока в 40 А. Если кузов сделан из более толстого материала, увеличьте данный параметр.
Смочите губку, расположите вокруг повреждения. Ее роль – охлаждение и, тем самым, ограничение зоны нагрева. Введите электрод на непродолжительное время в соприкосновение с металлом на участке ремонта.
Если держатель не перемещать, то образуются точки нагревания. При передвижении аппарата можно получить усадочные ряды. Категорически не рекомендуется держать электрод продолжительное время в контакте с металлом, иначе вы прошьете его насквозь.
Холодный пузырь убрать можно лишь тогда, когда он небольшой, а металл вытянут не сильно. С этой целью ручная наковальня заменяется мягким поддерживающим материалом. Например, это может быть твердая древесина, подогнанная рашпилем по контуру повреждения, либо отливка из свинца. Ударами молотка для рихтовки стяните металл, опирающийся на такую поддержку. Начинайте работу от кромок пузыря и продвигайтесь в его центр.
При рихтовке поверхности авто, поддержка подвергается воздействию деформации, она равномерно распределяет молекулы металла. При этом итог зависит от уровня вытянутости металла.
Когда удары вызывают неприемлемые повреждения на труднодоступных участках кузова, возникает нужда в разборке обшивки, а это хлопотно и долго. Этой ситуации можно избежать. С тем, чтобы не мучиться с разборкой лишь ради выправления небольшой деформации, можно ее убрать другим методом.
Традиционный способ, используемый для подобных случаев – это пайка при помощи олова. После зачистки поверхности металла, он лудится. Далее, вмятина заполняется оловянным припоем. Он опиливается напильником, имеющим отогнутую ручку, а затем поверхность шлифуется. Следует отметить, что подобное покрытие имеет хорошую адгезию и твердость.
Сейчас все большее распространение приобретают споты. Такая технология предполагает временную приварку электрода к металлу для его вытягивания. Вариаций споттеров много. Вы можете приваривать к металлу электрод либо переходные элементы, имеющие различную конфигурацию.
Наконечник сварочного аппарата при этом снабжается крючком либо цанговым зажимом. Выправляющее усилие можно создавать рычагом либо обратным молотком. Главная ценность способа – возможность обработки лицевой стороны кузова без разборки обшивки.
Чтобы вы могли до конца понять все тонкости процесса, мы публикуем материал, как делать кузовной ремонт своими руками: видео.
Мелкий кузовной ремонт
Повреждения кузова не только портят внешний вид «железного коня», каждое из них становиться потенциальным очагом коррозии и со временем снижает прочность кузова.
По этой причине кузовной ремонт выполняют сразу после выявления повреждений. Если вы планируете заняться восстановлением автомобиля самостоятельно — эта статья для вас. В ней мы рассмотрим основы кузовного ремонта, методику диагностики автомобиля и классификацию повреждений. В условиях гаража невозможно провести сложные работы, поэтому более подробно будет освещен мелкий кузовной ремонт и покраска: используемые материалы и инструменты, в какой последовательности их выполняют работы.
Осмотр повреждений автомобиля
[contents h3 h4]
Коротко о повреждениях
Повреждения кузова автомобиля условно делят на аварийные (не эксплуатационные) и эксплуатационные. Аварийные возникают преимущественно в результате ДТП. Размеры не эксплуатационных повреждений варьируют: от глубокой вмятины или разрыва металла кузова до поверхностной царапины. Чаще всего в ДТП повреждается передняя часть кузова, на втором месте — задняя часть.
Повреждения, возникшие вследствие эксплуатации автомобиля, обусловлены разными факторами. Самая распространенная причина — коррозия металла кузова. Перепады температуры, влажность, химические соединения, которыми обрабатывают дороги от наледи, УФ-излучение, щебень и гравий, нефтепродукты и даже промышленные загрязнения воздуха — все эти факторы вызывают повреждения лакокрасочного покрытия, развитие окислительных процессов и появление ржавчины. Причем коррозия чаще возникает на участках кузова, где ее сложно сразу обнаружить: закрытые пазухи, карманы, сварные швы и т. д. Вследствие коррозии металл окисляется, на поверхности появляется ржавчина, прочность деталей кузова снижается, отслаивается лакокрасочное покрытие.
Часто эксплуатационные повреждения появляются в результате нагрузок на кузов при работе автомобиля: от вибраций двигателя и ходовой, неровностей дороги, перевозимого груза. Усталость металла приводит к деформациям и трещинам.
Деформация корпуса авто в задней частиЕще один фактор появления повреждений — неосторожность водителя. Удар о бордюр при неосторожном открывании дверей, или вмятины из-за неаккуратного выезда из гаража оставляют следы на лакокраске.
Виды ремонта
Ремонт кузовов автомобилей бывает трех видов:
- Сложный кузовной ремонт машины, который проводится при глубоких вмятинах, разрывах металла и деформациях кузова. К таким работам относят правку, сварку, восстановление геометрии, рихтовку вмятин больших и средних размеров. Чтобы выполнить эти работы нужно специальное оборудование и соответствующий опыт работы у исполнителя. Если у вас нет необходимых навыков, доверьте такие кузовные работы мастерам СТО.
- Локальный или мелкий кузовной ремонт заключается в устранении сколов, царапин, неглубоких вмятин и коррозионных участков.
- Покраска и полировка — комплекс работ по восстановлению лакокрасочного покрытия автомобиля. Их выполняют после окончания большинства ремонтных работ.
Мелкий кузовной ремонт и покраска своими руками под силу обычному автовладельцу, их можно сделать самостоятельно.
Диагностика состояния кузова
Прежде чем выполнять мелкий кузовной ремонт своими руками, внимательно осмотрите кузов и оцените его состояние. Диагностика проводится в несколько этапов.
Диагностика состояния и повреждений машиныПервый этап — оценка состояния лакокраски. Внимательно осмотрите машину, есть ли на поверхности сколы или царапины, также обратите внимание на однородность окраски, наличие разводов или пятен. Авто лучше осматривать не в закрытом помещении, а на солнечном свете, так как при таком освещении отчетливо проявляются поверхностные дефекты.
Второй этап — проверка геометрии кузова. Большие перекосы видны даже невооруженным взглядом. Для обнаружения небольших деформаций в автосервисах используют специальное оборудование, которое недоступно рядовому автолюбителю. Но по некоторым признакам нарушение геометрии кузова обнаруживают и в условиях гаража. Сначала промеряйте или визуально оцените симметричные зазоры с каждой стороны кузова — они должны быть одинаковыми. О перекосах свидетельствуют крышки багажника, капота и двери салона. Багажник и капот должны с одинаковым усилием открываться и закрываться с каждой стороны, а щели между кузовом и крышками должны быть одинаковыми справа и слева. То же касается правых и левых салонных дверей.
Проверка геометрии кузова автомобиляТретий этап — проверка сварных швов и крепежных элементов. Эти места испытывают повышенную нагрузку при эксплуатации. Вибрации при движении автомобиля стают причиной появления трещин и коррозии в местах сварочного соединения, поэтому внимательно осмотрите лакокрасочное покрытие на данных участках.
Кузовной ремонт
Если при осмотре обнаружены вмятины, сколы, следы коррозии или небольшие трещины, смело начинайте кузовной ремонт автомобиля своими руками.
Определенного перечня расходных материалов и инструментов при проведении ремонта нет, так как каждое повреждение требует индивидуального подхода. Рассмотрим самые распространенные:
- Есть несколько методик для устранения неровностей, самая популярная — выравнивание с помощью полимерной смолы и стеклоткани.
- Перед тем как приступить к работам, с места повреждения удаляют лакокрасочное покрытие. Для этого используют наждачную бумагу с разной степенью зернистости или «болгарку» со специальными насадками.
- После устранения дефекта отремонтированную поверхность в большинстве случаев окрашивают. Для выполнения покраски приготовьте шпатлевку, грунтовку, краску и лак для автомобиля, а также инструменты для работы с этими материалами: шпатели и краскопульт.
- В процессе мелкого ремонта понадобится обезжириватель (уайт-спирит, ацетон, спирт) и салфетки или ветошь для его нанесения.
Выполнение мелкого ремонта
Кузовной ремонт авто и покраска часто проводятся вместе. Поэтому выполнение работы условно можно разбить на такие этапы:
- Подготовка автомобиля.
- Устранение неровностей или коррозии.
- Покраска и полировка.
Подготовка
Кузовной ремонт своими руками начинается с очищения поверхности автомобиля. Для этого машину моют специальным средством и высушивают. Эта процедура защитит участок работы от попадания пыли и позволит точно оценить степень и характер повреждений.
Чтобы самому сделать кузовной ремонт, с области повреждения снимают лакокрасочное покрытие до металла. Это можно сделать с помощью наждачной бумаги или шлифовальной машины со специальными насадками. Перед началом ремонтных работ поверхность еще раз очищают от пыли и обезжиривают.
Ремонтные работы
Ремонт кузова авто своими руками обусловлен неровностями поверхности или коррозией. Технология ремонта кузова отличается в зависимости от причин его проведения.
Быстрый ремонт мелких повреждений кузова позволяет устранить неглубокие вмятины и сколы. Если лакокрасочное покрытие автомобиля не повреждено, при устранении мелких неровностей используют специальные инструменты: зажимы, стапели и другие. Эти инструменты многофункциональны, например, зажим для кузовных работ своими руками позволит выполнить ряд работ: вытягивание, правку и рихтовку.
Устранение проблем кузова транспортного средстваДля устранения вмятин среднего размера или сквозных отверстий понадобятся стеклоткань и полиуретановая или эпоксидная смола. Из стеклоткани вырезают латку нужного размера, накладывают ее на место повреждения и наносят сверху смолу. Полимер быстро застывает, поэтому его готовят небольшими порциями и сразу же используют. Поверх каждого слоя смолы накладывают следующую латку. Процедуру повторяют до тех пор, пока поверхность не выровняется. После того как слой полимера полностью скроет дефект, поверхность зашкуривают наждачной бумагой и готовят к покраске.
Совет! Для устранения повреждений кузова используется также алюминиевая сетка для ремонта кузова. Ее применяют так же, как и стеклоткань: вырезают заплатки соответствующего размера и промазывают каждый слой шпатлевочным раствором.
Ремонт кузова своими руками, причиной для которого стала коррозия, включает обязательную зачистку ржавчины и обработку поверхности антикоррозионным составом. Слой ржавчины удаляют металлической щеткой, наждачной бумагой, шлифовальной машиной или специальными химическими составами.
Кузова, изготовленные из алюминия, обладают массой преимуществ: они стойкие к коррозии, легкие и отличаются длительным сроком эксплуатации. Но ремонт алюминиевого кузова часто создает проблемы для автолюбителей. Для ремонта используют те же инструменты, что и для стальных деталей, но технология работы с этим мягким металлом имеет свои особенности. Кроме того, алюминиевые детали поддаются только аргонной сварке, поэтому в некоторых случаях их дешевле заменить, чем отремонтировать.
Покраска и полировка
Работники СТО используют новые технологии кузовного ремонта, при которых лакокрасочное покрытие не повреждается. А кузовные работы своими руками часто сопровождаются покраской и полировкой места повреждения. Покраска, завершающая мелкий ремонт автомобиля, обычно выполняется методом перехода или «пятном». При таком способе окрашивания граница между старым и новым лакокрасочным покрытием размывается и не бросается в глаза.
ПОСМОТРЕТЬ ВИДЕОИНСТРУКЦИЮ
Если после окрашивания на месте повреждения нет поверхностных дефектов, косметический ремонт автомобиля своими руками заканчивают защитной полировкой: на салфетку наносят полироль для кузова автомобиля и втирают средство круговыми движениями.
Кузовной ремонт автомобиля и 3 совета по самостоятельному ремонту кузова
Кузов каждого транспортного средства защищает его от разных повреждений, обеспечивает оптимальный уровень безопасности и комфорта для пассажиров и для водителя. В процессе длительной эксплуатации данная часть автомобиля нуждается в проведении периодических ремонтных или восстановительных процессов. При ДТП ремонт кузова автомобиля крайне необходим, так как придётся не только устранять разные дефекты, но проводить восстановление отдельных частей транспортного средства.
Провести ремонтные работы можно в дилерских центрах по гарантии, в специализированных СТО. Чтобы значительно сократить часть материальных трат на проведение кузовного ремонта, можно произвести его самостоятельно. Главное позаботиться о наличии специального помещения, инструментов, оборудования, и без определённых навыков не обойтись. В данной статье описаны основные виды ремонтных работ. Также даны полезные рекомендации, как правильно выполнить ремонт кузова автомобиля своими руками.

Содержание статьи
Виды кузовного ремонта
В профессиональной среде различают три основных вида кузовного ремонта – небольшой локальный, внешний, сложный и капитальный. Каждая категория работ характеризуется своими индивидуальными особенностями и заслуживает отдельного рассмотрения.
Сложный ремонт
Сложный ремонт ещё называют полным или капитальным. Подобные работы невозможно выполнить самостоятельно, так как они требуют достаточно серьёзного подхода и наличия современных профессиональных инструментов. Проводится сложный ремонт при таких обстоятельствах, как:
- устранение последствий разного рода ДТП;
- замена элементов обшивки и важных деталей;
- удаление значительных нарушений кузовной геометрии;
- устранение сложных деформаций.
Чтобы провести капитальный или сложный ремонт, потребуется наличие серьёзного оснащения – стапели, подъёмники. С их помощью можно эффективно контролировать общие параметры автомобильного кузова, устанавливать контрольные точки геометрии кузова. Справиться с этим могут только высококвалифицированные специалисты. Своими руками можно выполнить только такой ремонт, который характеризуется относительно несерьёзными повреждениями.
Локальный ремонт
Данная форма ремонтных работ применяется при незначительных внешних повреждениях кузова транспортного средства. Это идеальное решение при таких проблемах, как:
- неглубокие и мелкие сколы и царапины;
- несерьёзные вмятины;
- коррозия металла на начальной стадии.
Локальный ремонт не требует серьёзных материальных трат и применения дорогостоящего современного оборудования. Всё, что может потребоваться от мастера – краска, полироль и набор специальных инструментов.
Покраска
Если для восстановления внешнего вида транспортного средства требуется полная покраска авто, придётся так же, как и при сложном ремонте, обратиться за помощью к профессионалам. Самостоятельно можно провести только мелкие локальные покрасочные работы.
Мероприятия такого плана проводятся только в особых косметических целях. Это может быть не только устранение царапин, но также нанесение аэрографии. Чтобы провести подобные восстановительные процессы, потребуется подготовить не только лакокрасочные материалы, но также аэрографические и покрасочные инструменты.
Ремонт в дилерском центре
Если водитель попал в ДТП или транспортное средство находится на гарантийном обслуживании, кузовной ремонт и покраска кузова автомобиля могут быть проведены в специализированном дилерском центре.
В подобных организациях профессионалы готовы провести весь комплекс ремонтных работ. Кузовной ремонт осуществляется строго с учётом модели авто, годом его выпуска и особенностях уже нанесённого лакокрасочного покрытия. Необходимые запасные части всегда есть в наличии, а также время от времени проводятся выгодные акции. Обратиться в дилерский центр можно при наличии таких проблем и недочётов, как:
- удаление сколов, трещин и вмятин;
- диагностика геометрии кузова;
- сварочные и жестяные работы;
- восстановление антигравийного и антикоррозийного покрытия;
- покраска кузова с одновременным выбором автоэмали;
- ремонт пластиковых элементов кузова;
- полная или частичная полировка кузова;
- ремонт и замена стёкол и оптики;
- локальный ремонт кузова автомобиля.
Одним из самых важных преимуществ обращения в подобные центры является сотрудничество с компаниями, которые поставляют лакокрасочные покрытия. Это позволяет значительно увеличить гарантию на уже проведённые малярно-кузовные работы.
Восстановление в организации, выполняющей кузовной ремонт
Если проблемы осложнены сильными вмятинами или выходом из строя функциональных элементов, если восстановление не связано со страховым случаем и вышел гарантийный период ремонтных работ автомобиля, то для проведения таких мероприятий, как удаление царапин на кузове автомобиля без покраски, стоит обратиться в СТО.
Это оптимальная возможность устранить проблему посредством применения специализированного оборудования. Процесс восстановления в подобных организациях осуществляется в два основных этапа:
- Восстановление геометрии и установленных производителем размеров кузова. На данном этапе мастера используют зажимы, стапели, специальные растяжки, а также проводят полную диагностику авто при помощи современного оборудования.
- Нанесение качественных антикоррозийных защитных составов на кузов. Здесь используются специальные восковые составы, разного рода абразивы и жидкое стекло.
При грамотно проведённой диагностике и применении самого современного инструментария удаётся предотвратить образование и последующие ремонт достаточно серьёзных проблем.
При восстановлении кузовной части авто в СТО трудятся такие специалисты, как жестянщик, автомеханик, колорист, а также специалист по малярным работам. С таким процессом, как рихтовка без покраски и полное окрашивание авто, в состоянии справиться только очень опытный сотрудник. Если осуществляется покраска авто после серьёзной деформации ЛКП, выбор правильного уникального оттенка имеет чрезвычайное значение. Эти занимается профессиональный колеровщик.
Высокого качества услуги по ремонту кузова и полный спектр сервисных процедур в состоянии вернуть транспортному средству идеальный внешний вид и лоск новизны.
Правильная приёмка и проверка качества выполненной работы
После проведённых работ в организации сервисного обслуживания стоит внимательно подойти к оценке качества процессов восстановления. Проверка должна осуществляться по нескольким направлениям:
- восстановление общего положения контрольных точек, которые определяют геометрию силовых кузовных элементов;
- обеспечение защиты и прочности кузова, рамы, а также большого количества силовых элементов;
- восстановление скрытых кузовных элементов, которые получили сильное повреждение;
- восстановление формы у наружных поверхностей и их стыковки с расположенными рядом элементами;
- грамотный подбор цветового решения лакокрасочного покрытия;
- общее качество окрашивания кузова;
- восстановление антикоррозийного покрытия;
- функционирование и регулировка шарниров капота и дверных конструкций, герметичность их прилегания;
- отсутствие протечек в остеклении и багажном отделении;
- отсутствие следов проведённого ремонта.
Желательно завершить проверку контрольной поездкой, чтобы оценить сохранение общей курсовой устойчивости и проверить шумы, которые могут возникнуть при нарушении герметичности многочисленных проёмов в транспортном средстве.
Кузовной ремонт своими руками
Перед тем, как провести кузовной ремонт авто своими руками, стоит изучить видео на тематических сайтах . Это поможет понять, какие инструменты и материалы потребуется подготовить, а также ознакомиться с пошаговым процессом устранения той или иной проблемы.
Необходимый инструмент и приспособления
Ремонт кузова транспортного средства – это не только серьёзное, но и достаточно затратное в финансовом и временном плане мероприятие. Результат проведённых работ прямо зависит не только от квалификации мастера, но также от грамотности подготовительных мероприятий. Вот примерный перечень материалов, которые потребуется подготовить:
- Растворитель – необходим для разведения грунтовок, лакокрасочных основ и шпатлёвок. Также растворитель используется для тщательного обезжиривания поверхности.
- Шпатлёвка – применяется для устранения незначительных дефектов, таких, как вмятины, сколы, царапины, трещины.
- Грунтовка – необходима для обработки поверхности непосредственно перед окрашиванием. Данный состав значительно улучшает общие адгезивные характеристики поверхности деталей авто.
- Краска. Данные составы могут быть разными – акриловые, целлюлозные, алкидные и порошковые, выполненные на водной основе. В зависимости от размеров участка, требующего восстановления, краски приобретаются в жидком виде или в качестве аэрозолей.
- Лаки и полироли. Лаки необходимы для защиты покрасочного слоя от износа в процессе эксплуатации авто. Что касается полиролей, то при правильном их применении данные составы придают поверхности кузова глянец и лоск.
Наряду с перечисленными выше материалами и основами в обязательном порядке нужно подготовить специальные инструменты. Потребуется наждачная бумага для шлифовки поверхностей. Если требуется шпатлевать разного плана поверхности, инструмент из резины в состоянии обеспечить максимально бережное отношение к неповреждённому покрытию.Если восстанавливается достаточно большая поверхность кузова, для её выравнивания можно использовать специальную шлифовальную машинку.Для нанесения краски на такую же большую поверхность используется компрессор и краскопульт. Чтобы максимально упростить и ускорить процесс полировки, стоит приобрести или взять в аренду полировальную машинку.
Советы по выполнению отдельных операций
При проведении локальных ремонтных кузовных работ стоит опираться на определённые практические советы. Следуя им, можно провести такие работы, как ремонт вмятин на кузове автомобиля без покраски максимально быстро, без необходимости проводить коррекцию и обращаться за исправлением ошибок к профессионалам. Среди самых полезных и действенных рекомендаций можно отметить следующие:
- если царапины повредили только верхнее лаковое покрытие, восстановить его можно при помощи приобретённого в автомагазине маркера-замазки;
- если немного повреждена краска, стоит приобрести специальный комплект для восстановления с замазкой, соответствующей цвету авто;
- при наличии вмятин необходимо использовать специальные инструменты – рычаги и крюки. Их нужно заводить под металл, выравнивая поверхность.
Необходимо помнить, что все покрасочные работы, связанные с таким процессом, как удаление царапин на кузове автомобиля, проводятся только на тщательно вычищенную поверхность детали, иначе есть риск столкнуться с проблемой неровного и соответственно некачественного покрытия.
Выводы
Кузовные работы могут быть разного уровня сложности и включать в себя множество процессов. Здесь всё зависит от общей степени повреждения. Если авто восстанавливается после ДТП, желательно обратиться к профессионалам, если же требуется провести более простые ремонтные процессы, можно будет вполне справиться своими силами.Самое главное — подготовить все необходимые инструменты и оборудование, а также ознакомиться с пошаговыми инструкциями по устранению тех или иных проблем.
Рихтовка своими руками

Приветствую Вас на блоге kuzov.info!
В этой статье рассмотрим как осуществляется рихтовка своими руками. Подробно разберём структуру повреждений, этапы, принципы и приёмы рихтовки, а также классические рихтовочные инструменты и их применение. Основные принципы рихтовки могут пригодиться и при применении споттера с вытягивающими устройствами. В конце статьи рассмотрим примеры правильного и неправильного устранения деформации кузовной панели.
Можете также прочитать статьи о выравнивании и вытягивании кузова автомобиля, где также рассматриваются методы устранения аварийных повреждений.
Содержание статьи:
Итак, начнём с теории.
Можно выделить три характеристики листового металла:
- Пластичность
- Эластичность (упругость)
- Жёсткость (наклёп)
Пластичность позволяет металлу менять свою форму при приложении достаточной силы. Это то же самое свойство, которое позволяет отштамповать металл в любую кузовную панель.
Упругость – это свойство металла, которое позволяет ему восстанавливаться до оригинальной формы, после устранения напряжения.
Жёсткость лист металла получает при штамповке на заводе. Это можно назвать «памятью». Происходит наклёп отдельных зон, которые и придают форму кузовной панели. Металл получает внутренние напряжения.

Металл кузовной панели, который не был растянут или смещён, имеет тенденцию возвращаться в своё изначальное положение. В этом случае он не гнётся дальше, чем ему позволяет его упругость. Однако, если металл погнулся дальше своей упругости, то молекулы в месте сгиба деформируются и уплотняются, и из такой позиции металл не возвращается сам. Металл в этой зоне становится жестче и сопротивляется выравниванию. Происходит деформационное упрочнение детали (наклёп).
Металл с упругой деформацией восстанавливается после прекращения воздействия. Пластическая же деформация остаётся неизменной после исчезновения воздействия. Нужно выправлять зоны с пластической, а упругая деформация возвратится сама, так как она удерживается только за счёт пластической деформации.
Кузовные панели состоят из трёх базовых форм: сильно выпуклые, средне выпуклые и слабо выпуклые. Также могут иметь комбинацию изгибов (выпуклостей) и рёбра жёсткости. Выпуклость панели влияет на то, как металл отреагирует на удар. Удар по слабо выпуклой панели сдвигает металл внутрь, сокращая его (становится короче). Сильно выпуклая панель при ударе формирует изгибы (возвышенности) по краям вмятины. Более подробно об этом можете прочитать здесь.
Прямое и второстепенное повреждение
Можно разделить прямое и непрямое (второстепенное) повреждение. Прямым повреждением является область кузовной панели, которая была в непосредственном контакте с объектом, который вызвал повреждение. Это место может иметь нарушение целостности лакокрасочного покрытия или разрыв металла.
Непрямое повреждение имеет погнутый и искажённый металл, расположенный в области, прилегающей к прямому повреждению. Иногда второстепенная деформация может располагаться в нескольких десятков сантиметров от зоны прямого повреждения. Его сложно полностью определить и проанализировать.
При восстановлении повреждения, метод ремонта определяется возможностью доступа к повреждению с обратной стороны кузовной панели. Если есть доступ с обеих сторон повреждения, то используется метод рихтовки при помощи молотка и поддержки. Если есть доступ только с одной стороны, то применяются другие техники ремонта, такие как вытягивание при помощи споттера, при помощи клеевой системы или вакуумной присоски.
При ремонте повреждений нужно стараться выбирать наиболее лёгкий путь. Даже если Вы имеете специальное оборудование, то это не значит, что его нужно везде и всегда применять. По возможности, применяйте простые инструменты, а при необходимости, включайте в работу более сложные. Иногда вмятину можно выдавить с обратной стороны рукой, без какого-либо инструмента. Нужно помнить, что сейчас автопроизводители используют достаточно тонкий металл при производстве кузовных панелей, поэтому не требуется больших усилий, чтобы восстановить деформацию.
Инструменты для рихтовки
Рассмотрим классические инструменты для рихтовки повреждённого металла кузова, которые по-прежнему применяются в кузовном ремонте. Молоток/гладилка и поддержка являются базовыми инструментами для работы с повреждёнными кузовными панелями.
Рихтовочные молотки
Молотки могут быть разных размеров, форм и иметь разный вес. Ударные головки обычно круглой или квадратной формы. Также есть молотки, с другой стороны бойка которых острая ударная головка. Он используется на финишной стадии без поддержки. Острой частью можно убрать небольшую возвышенность или выправить небольшую ямку, после чего уже применить плоскую часть бойка с поддержкой для окончательного выравнивания.
Также есть молотки с ударными головками, имеющими зубцы, предназначенные для усадки растянутого металла. Ручки молотков изготавливают из дерева или стеклопластика.
Молоток обычно применяется для выправления небольших вмятин и возвышенностей. Нужно уметь простукивать нужные области, в нужное время и с нужным усилием. Рихтовочные молотки имеют немного выпуклый боёк (почти плоский). Это нужно, чтобы его края не касались и не повреждали металл панели при рихтовке.
Удары, используемые при рихтовании молотком с поддержкой, не должны делаться с усилием, как при забивании гвоздей. Они должны быть лёгкими, скользящими, ритмичными. Молоток нужно держать свободно и при ударе двигать запястьем. Опытный рихтовщик делает примерно 120 лёгких ударов молотком в минуту в одинаковом ритме. Молоток отскакивает и запястье поднимает молоток для совершения следующего удара. Пальцы контролируют молоток в начале и в конце удара. При движении бойка молотка вниз и вверх, конец его ручки совершает движение по короткой дуге. Рука расслаблена, но готова крепко схватить ручку молотка после его отскока.
Правильные движения молотком требуют определённого навыка. Молоток должен быть сбалансирован. Несбалансированный молоток будет отскакивать, беспорядочно смещаясь в разные стороны от цели удара. Такой молоток придётся держать крепко в течение всего удара и не получиться делать лёгкие удары. К тому же не получиться соблюдать ритм повторяющихся движений.
Кузовные ложки, гладилки
Кузовные ложки, как и любой рихтовочный инструмент, бывают разных форм и размеров. В зависимости от формы, кузовная ложка может применяться как рычаг, для выравливания вмятины с обратной стороны панели, как поддержка (в труднодоступных местах), а также вместе молотка (гладилка) и вместе с молотком, для распределения удара на большую площадь.
Гладилку можно использовать несколькими способами. При использовании с поддержкой, имеющей насечки, гладилка может осаживать металл.
Гладилкой хорошо работать на относительно плоских поверхностях. Она не растягивает металл, поэтому удары можно наносить сильнее, чем молотком. Гладилка ещё хороша тем, что она, благодаря своей площади, может одновременно «поднимать» вмятину и простукивать возвышенности вокруг этой вмятины.
Складки на металле в местах, где невозможно использовать молоток вместе с поддержкой, могут исправляться методом “молотком через гладилку” (см. рисунок). Гладилка рассеивает удары, распределяя их на большую площадь. Она помещается поверх жёстких возвышенностей и простукивается до момента, когда напряжение металла ослабнет.
Поддержки
Хорошие поддержки сделаны из кованного железа. Дешёвые могут быть сделаны из чугуна. Для универсальности, каждая поддержка может состоять из нескольких выпуклостей для соответствия разным контурам кузовных панелей.
При выправлении вмятины поддержка удерживается с обратной стороны панели с давлением, создаваемым рукой рихтовщика. При простукивании возвышенности, поддержка удерживается свободно, без давления.
Поддержка должна иметь форму, соответствующую изгибу ремонтируемой панели. Нужно простукивать возвышенности вокруг вмятины. Каждый последующий удар должен перекрывать предыдущий удар на половину диаметра ударной головки молотка. Так можно выправлять вмятину от периферии к центу.
Слишком сильные удары по поддержке через металл панели могут сделать его тоньше и растянуть.
Поддержка общего назначения может использоваться для грубого первоначального выправления повреждения (так как тяжёлая и имеет соответствующую большую закруглённую часть). Её применяют в разных местах, так как она имеет поверхности с разными изгибами и углами.

Поддержка в виде каблука имеет плоскую часть и слабо выпуклую. Такую поддержку удобно применять при выравнивании фланцев, а также на плоских и слабовыпуклых поверхностях. Её часто применяют при рихтовке дверей.
Поддержка в виде запятой (или клина) может применяться при рихтовке слабовыпуклых и сильно выпуклых панелей, а также в местах, куда другую поддержку невозможно поместить. Её можно легко просунуть и удерживать между усилителями.
Кузовной напильник
Кузовной напильник может использоваться на начальной стадии ремонта, для определения структуры повреждения, а также на завершающей стадии выравнивания металла. Рабочая часть сделана из очень прочной стали и имеет зазубрины. Держатель напильника имеет две ручки и винтовую стяжку для регулировки изгиба напильника. В зависимости от изгиба, уменьшается или увеличивается рабочая площадь напильника для удобства использования в разных местах панелей. Кузовные напильники бывают разных размеров, форм и могут иметь разное количество и конфигурацию зубцов. Менее грубые напильники могут использоваться на алюминиевых кузовных панелях.
Кузовной напильник может:
- Проявлять структуру повреждения на начальной стадии ремонта.
- Выявлять мелкие углубления и возвышенности при финишной рихтовки кузовной панели.
- Срезать небольшие возвышенности.
- Применяться на завершающей стадии выравнивания, когда используется тонкий слой шпаклёвки.
- Выравнивать сварочные швы.
- Обрабатывать поверхность после лужения и нанесения припоя на кузов (см. статью “лужение и пайка кузова автомобиля”).
Режущая часть зубцов должна быть направлена наружу, от мастера, держащего напильник. Напильник должен проделывать длинные проходы по всей длине панели. Если напильник застревает во время движения, то нужно ослабить нажим. Движения делаются только от себя, после сделанного прохода напильник нужно поднять и возвратить в исходное положение для выполнения нового прохода.
Сменные полотна могут иметь зубцы разного размера и расположенные с разной плотностью. Так, при финишной обработки, хороший напильник может подготавливать поверхность, даже не оставляя царапин. Это связано, как с размером и плотностью расположения зубцов, так и с их формой.
Напильник срезает металл, поэтому обработка не может быть многократной. Напильником нужно обрабатывать поверхность, двигая его от себя и немного боком (наискосок, 15–20 градусов). При движении напильника, его прижимную силу нужно смещать с передней части к задней. Получается, что он как бы качается. Нужно менять направления движения напильника, то есть двигать попеременно крест накрест.
Для выявления неровностей, вместо кузовного напильника можно использовать крупнозернистую шлифовальную бумагу на бруске или на орбитальной шлифовальной машинке. Принцип тот же. Нужно отшлифовать рихтуемую поверхность. Ямки будут не задеты абразивом, а выступы будут отшлифованы сильнее, чем вся поверхность, и будут иметь неотшлифованные области вокруг них. Если возвышенности совсем не высокие, то они отшлифуются и эта область панели примет нужный контур. При применении шлифовальной машинки, она должна двигаться медленно и равномерно, но не слишком медленно, чтобы не нагревать металл. При быстром движении абразив не будет успевать нормально шлифовать.
Шлифование крупным абразивом, как и обработка напильником, истончает металл панели, поэтому не должно применяться много раз на одной и той же детали кузова. Для обнаружения неровностей и шлифования мелких возвышенностей может использоваться шлифовальная машинка с абразивом P36-P80. Машинку нужно двигать медленно, каждый её проход должен перекрывать предыдущий на 50%. На «голом» металле лучше всего использовать шлифовальные круги на основе абразива оксида алюминия, так как он наиболее прочный и износостойкий и обычно применяется для шлифования сплавов металла.
Надувные подушки и вакуумные присоски
Специальные надувные подушки используются с обратной стороны повреждённых панелей, для выдавливания вмятин большого размера. Они могут использоваться внутри дверей, задних крыльев и других панелей.
Вакуумная присоска может использоваться для вытягивания плавных вмятин. Она может иметь ручку или быть в составе молотка обратного действия.
Рихтовка кузова автомобиля. Этапы ремонта
Как было сказано ранее, грамотная процедура ремонта деформированной панели представляет собой выправление только тех мест, которые получили пластическую деформацию. Относительно не повреждённые прилегающие зоны после этого возвратятся в первоначальное состояние самостоятельно. Такой метод требует немного усилий и мало действий.
Можно также воздействовать на обратную сторону повреждения тяжёлым молотком или другим тяжёлым инструментом. Повреждение выдавливается или выстукивается грубо, без каких-либо специальных правил. При использовании такого метода могут возникать дополнительные повреждения и растянутость металла, которые требуется в дальнейшем устранять.
Более предпочтителен именно вдумчивый, грамотный подход к ремонту.
Грамотный ремонт повреждения включает в себя три стадии:
- анализирование повреждения,
- правка на черновую (восстановление формы),
- правка на чистовую (финишная).
Рассмотрим эти этапы подробно:
- Анализ повреждения является первой и наиболее значимой стадией, так как от правильного определения зон деформации, куда нужно приложить усилие, зависит быстрота процесса и конечный результат. Процедура выправления повреждения должна опираться на этот анализ. Нужно понимать в какой последовательности произошла деформация. Нужно определить направление, из которого панель получила деформацию и определить какой залом или складка образовались последними, какие перед этим и так далее вплоть до места, которое получило первый прямой контакт с препятствием. Далее нужно определить план действий по устранению деформации в порядке, противоположном их возникновению. Некоторые повреждения могли образоваться одновременно и нужно это учитывать. Процесс восстановления не должен создавать дополнительных повреждений. Таким образом, потратив некоторое время на анализирование структуры неровностей и обдумывание порядка восстановления, работа выполняется гораздо легче и быстрее, кроме того, становится более интересной.
Приложение линейки ребром поможет понять глубину вмятины.
При анализе, повреждённую панель можно прощупать рукой. Обычно для этого используют левую руку. Нужно двигать всей ладонью вдоль панели. Только пальцы не смогут прочувствовать, какого рода неровность перед вами. Иногда мастера надевают матерчатые перчатки, так как в них легче прочувствовать форму металла. Степень неровности можно определить, прикладывая линейку ребром к панели. Кузовной напильник также может применяться для быстрого определения структуры повреждения. После обработки напильником, срезанная краска на краях вмятины выявит её фору и размер.
- В результате грубой рихтовки выправляются рёбра жёсткости, заломы, большие вмятины и кузовная панель принимает свою оригинальную форму. На этом этапе не нужно зацикливаться на одном единственном месте, необходимо делать несколько проходов по всей панели, постепенно выравнивая её. Нужно ослаблять напряжённые области, полученные при ударе, и препятствующие возвращению металла в его первоначальное состояние. Несколько лёгких ударов в нужное место более эффективны, чем один или два сильных удара. Вмятины выправляются и одновременно простукиваются возвышенности и складки окружающей её области. Здесь часто применяется метод «молоток вне поддержки», который будет рассмотрен ниже. Можно использовать молоток и деревянный брусок или специальную надувную подушку, для воздействия с обратной стороны повреждения. Незначительные неровности на этом этапе по-прежнему остаются, они не должны отвлекать рихтовщика. Главная задача этого этапа – вернуть основную форму деформированной кузовной панели. Усадка растянутого металла (об этом ниже) и, при необходимости, заваривание разрывов также относится к этой стадии ремонта панели.
- Во время финишной рихтовки убираются мелкие неровности, и панель окончательно выравнивается. Повреждённый металл может быть отрихтован очень качественно, так, что будет достаточно только нанести наполняющий грунт, обработать его и красить. Для этого нужно набраться терпения, делать всё последовательно, без спешки и лишних усилий. На этом этапе применяется кузовной напильник, о котором было написано выше. Также здесь применяется метод рихтовки «молоток на поддержке» (см. ниже). На этом этапе можно использовать специальное проявляющее покрытие. Далее нужно сделать несколько проходов бруском с крупнозернистой шлифовальной бумагой. Это выявит неровности, которые сложно заметить. Потом нужно выправить оставшиеся углубления. После выполнения такой процедуры, нужно снова нанести проявочное средство и повторить шлифование. Таким образом, поверхность панели можно полностью выровнять. После этого кузовная панель подготавливается к грунтованию и покраске.
Методы рихтовки
Техника «молоток вне поддержки»
В этой технике молоток должен иметь небольшое расстояние (смещение) от поддержки. Поддержка давит на центр углубления на металле, в то время как Вы продолжаете простукивать возвышенности вокруг вмятины. Таким образом, возвышенности опускаются, а углубления поднимаются при каждом отскакивании поддержки. В большинстве случаев при грубой рихтовке нужно применять метод «молоток вне поддержки». Он используется при устранении большинства вмятин.
По возможности нужно всегда использовать гладилку вместо молотка. Гладилка больше прощает удары с неправильным усилием при рихтовке.
Гладилка и поддержка в этом методе не контактируют друг с другом. Этот метод хорошо подходит в ситуации, когда металл не получив значительного повреждения, может быть немного перенаправлен незначительным усилием для восстановления первоначальной формы. Методика «молоток вне поддержки» используется для поднятия углублений и возвышенностей одновременно. Эта методика применяется в основном на слабовыпуклых или плоских панелях, где металл достаточно податливый, в отличие от сильновыпуклых панелей.
Техника «молоток на поддержке»
Может применяться как для опускания возвышенностей, так и для выправления небольших вмятин. В этой технике нужно расположить поддержку прямо напротив повреждения. Молотком нужно не сильно простукивать металл, расположенный над поддержкой. При сильных ударах есть опасность растянуть рихтуемый металл. Нужно постоянно проверять металл прощупыванием, после чего продолжать рихтование до полного выправления повреждения. По возможности применяйте вместо молотка гладилку. Большое преимущество гладилки над молотком заключается в том, что она воздействует на большую площадь за один раз и удар распределяется более равномерно, чем удар молотком. Как было написано выше, гладилка хороша тем, что, благодаря своей площади, может одновременно поднимать углубления и опускать возвышенности на рихтуемом участке. При простукивании вмятины, нажимайте на металл поддержкой с достаточной силой. Если не надавливать с правильным усилием, то можно только увеличить повреждение. При простукивании возвышенности поддержку нужно держать наоборот свободно, без усилия.

Метод «молоток на поддержке» применяется при чистовой (финишной) правке. Также этот метод очень эффективен при выравнивании краёв панели.
Настоятельно рекомендуется, чтобы обратная сторона повреждённой панели была чистой, иначе это отразиться на качестве рихтовки. Поддержка должна быть правильно выбрана по форме. Слишком выпуклая форма поддержки сделает панель более выпуклой, а плоская – плоской.
При применении молотка с поддержкой должна быть развита координация. Поддержка должна находиться непосредственно под молотком.
Выправление вмятины молотком с острым бойком
Иногда, для выправления вмятины, можно применять молоток с острым бойком без поддержки. Такую технику нужно использовать очень осторожно, так как можно только усугубить повреждение. Идея заключается в том, чтобы поднять вмятину серией хорошо поставленных ударов молотком с острым бойком с обратной стороны панели. Вмятина должна выправляться не до конца. Вместе с поднятием вмятины получаются острые возвышенности от молотка, которые потом убираются дополнительным выравниванием. Неразумное применение такой техники может значительно растянуть металл и не дать удовлетворительного результата.
Усадка растянутого металла
Растянутый металл, после устранения деформации, будет значительно выше остальной поверхности, а также будет ослаблен и нестабилен. Его нельзя простучать молотком и опустить ниже, так как для него нет места. Он либо уйдёт целиком в противоположную сторону, либо снова обратно (хлопун). Если деформация была устранена в правильном порядке, правильными инструментами и с правильным усилием, то растянутый металл может быть только в зоне прямого повреждения. Если же деформация выправлялась без предварительного анализа, грубыми ударами молотка, то растянутый металл будет по всей ремонтной области. Такому металлу нужно вернуть нормальную толщину усадкой. Для возвращения металла в первоначальную форму его нужно «собрать». Усадка металла нагревом является достаточно простым процессом, но требует осторожности. Нужно определить самую высокую точку растянутого металла и нагреть её при помощи инструмента, который Вы используете для усадки. Далее нужно поместить поддержку под нагретую область и ударить молотком несколько раз, пока металл горячий. Так, металл вокруг усаживается в это нагретое пятно и становится толще и меньше по площади. Потом нужно охладить это место мокрой тряпкой или губкой. Таким же способом можно усадить остальные области с растянутым металлом. Нужно быть осторожным и не переборщить. Иначе металл деформируется и деформирует прилегающую область.

Незначительная растянутость металла может устраняться без простукивания. При нагреве растянутый металл сокращается, происходит его усадка. Нагретый металл сначала возвышается над общим уровнем панели. После нагрева и охлаждения, растянутый металл приобретает первоначальный профиль, либо становится немного ниже общего уровня плоскости панели. Также можете прочитать статью “Как убрать хлопун на металле”, где подробно рассматривается тема растянутого металла.
Правила при усадке нагревом:
- Обратная сторона нагреваемой панели должна быть очищена от шумоизоляционного материала.
- при усадке нужно применять поддержку, имеющую меньшую выпуклость, чем растянутая область металла.
- Обычно используется ацетиленовая горелка с насадкой, соответствующей толщине осаживаемого металла, но может также применяться нагрев полуавтоматической сваркой, специальным угольным электродом, а также специальной насадкой и режимом споттера.
- Ацетиленовой горелкой нужно нагревать до ярко красного цвета, держа её перпендикулярно поверхности.
- Никогда не остужайте металл, нагретый до красного цвета. Подождите, когда он немного сам охладится и станет чёрным.
- Никогда не нагревайте область больше, чем можете осадить молотком за один раз. Горелкой нагревается площадь от 10 до 25 мм.
- Во время нагрева нужно делать круговые движения горелкой, по спирали, от периферии к центру.
- Не пытайтесь сделать усадку растянутого металла, пока не выправите его на черновую.
- Не нагревайте для усадки вмятину.
- Если растянутый металл имеет небольшую область, то и нагревайте маленькое пятно для усадки.
- Можно делать усадку растянутого металла и без его последующего охлаждения мокрой тряпкой. Охлаждение лишь ускоряет процесс.
- После усадки, может потребоваться дополнительное выравнивание металла.
Пример ремонта простой деформации кузовной панели
Рассмотрим схематическое изображение простой деформации кузовной панели. Пунктиром показана оригинальная форма панели. Рихтовка производится в последовательности, противоположной возникновению повреждений.

Так как залом Х создан в повреждении последним, то эта область должна выправляться первой. На эту зону помещается плоская кузовная ложка и простукивается молотком, направляя удары прямо на край залома (рис. №2). Это ослабит возвышенность и сдвинет её в изначальную позицию. Далее простукивается угол фланца Z, ослабив напряжение в этой области. Области металла между 0 и Y и Y и Z теперь ослаблены и готовы к возвращению в оригинальную позицию при помощи небольшого усилия. Это усилие создаётся при помощи средневыпуклой поддержки, выправляя неровности двумя-тремя несильными ударами с обратной стороны с 0 по Y (рис. №3). Это ослабит напряжение металла с обратной стороны (отрезок 0Y). Процедура повторяется от Y до Z, восстанавливая металл до оригинальной формы №4.
Вторая иллюстрация (см. ниже) показывает ошибку черновой правки такого же повреждения. Здесь не было произведено первоначального ослабления напряжённых мест. На рис. №1, опущенный металл был выправлен ударами с обратной стороны до точки Y при помощи поддержки. Это подняло большую площадь вмятины практически до оригинальной позиции. Однако напряжение в точке X не было ослаблено. Напряжённый залом не опустился на своё нормальное место, вместо этого этот залом тянет панель вниз в зоне H. Так происходит, потому что напряжённый край X усиливает металл с обратной стороны. Таким образом, когда усилие прилагается сверху на Y, залом действует как опорный центр, утягивая металл вниз на H, когда прилагается усилие вверх на Y.

Когда черновое выравнивание было начато без ослабления напряжённой области, металл должен быть растянут для того, чтобы возвратиться в свою оригинальную позицию, как показано пунктиром. Теперь требуется значительное усилие, чтобы возвратить его вверх и это вызовет появление дополнительных повреждений на металле во время удара поддержкой, как показано на рис. №2. Выправление этих повреждений добавит работы. На рис. №3, вмятина была выправлена и молоток и поддержка на своём месте, чтобы начать выравнивание. На рис. №4, вмятина восстановлена до нормального состояния. Однако это уже получилась новая форма с растянутым металлом. Таким образом, работа сделана, но было потеряно время на незапланированную рихтовку, и металл был растянут. Пунктиром показан оригинальный контур панели.
Приведённые примеры показывают, что одну и ту же работу можно сделать по-разному, потратив разное количество усилий. При вдумчивом предварительном анализе повреждения можно значительно сократить время ремонта, его качество и уменьшить количество шпаклёвки или вовсе её исключить. Кроме того, правильно выполненная рихтовка принесёт удовлетворение от конечного результата.
[adsp-pro‑4]
Печатать статью
Ещё интересные статьи:
Особенности выбора сервиса, выполняющего кузовные работы: как не ошибиться
Нет водителя, который бы ничего не слышал о кузовном ремонте. Считается, что это сложная и дорогая работа, которая сильно бьет по карману, и не отличается хорошим качеством. Но, на самом деле правильно выполненный кузовной ремонт позволяет получить машину, как только что сошедшую с конвейера.
Для этого стоит правильно подобрать автосервис, ведь именно от этого выбора будет зависеть качество производимых работ. Рассмотрим основные принципы выбора автосервиса для кузовного ремонта.
НА ЧТО СМОТРЯТ ВОДИТЕЛИ
Для начала давайте посмотрим, что наши соотечественники учитывают при выборе сервиса. Это позволит понять, как следует выбирать, мастера кузовного ремонта, а также не ошибиться в выборе.
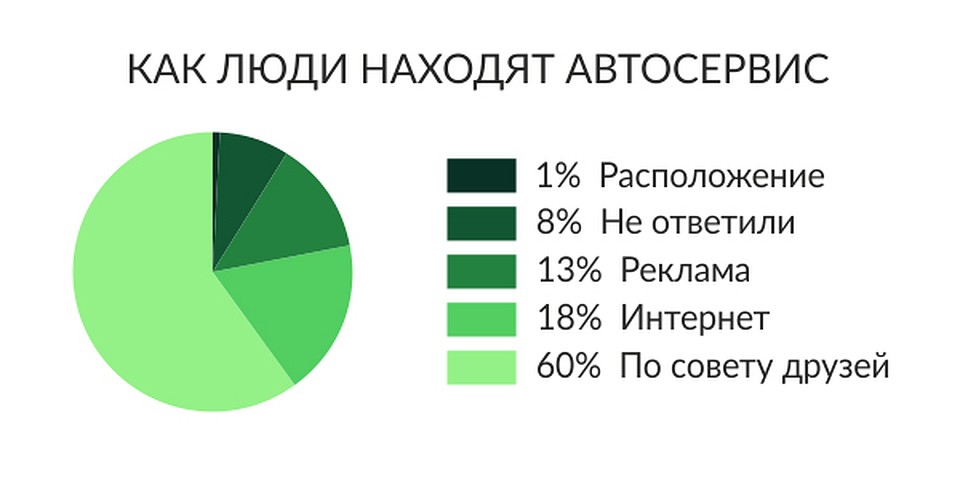
.
Для большей части автолюбителей основным критерием выбора является возможность проведения полного цикла обслуживания.
А теперь посмотрим, как люди находят подходящий сервис.
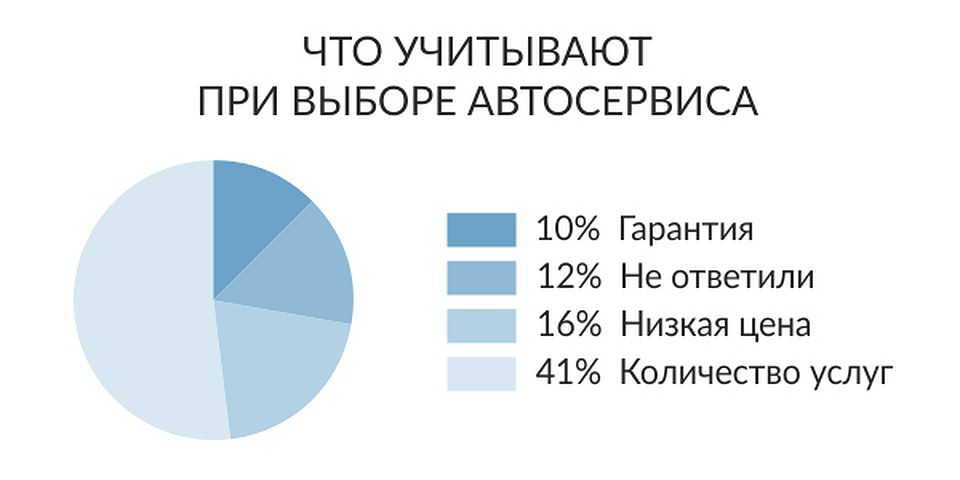
.
Как видите, большая часть автолюбителей предпочитают посещать сервисы, где уже были их знакомые. Срабатывает сарафанное радио, также много людей смотрят рекламу в интернете, остальные способы поиска все больше теряют популярность. Стоит отметить, что в 8%, которые не смогли ответить на вопрос, входят и те, кто ремонтирует кузов автомобиля своими руками, хотя в последнее время таких умельцев все меньше.
КАКИЕ МОМЕНТЫ СЛЕДУЕТ УЧИТЫВАТЬ
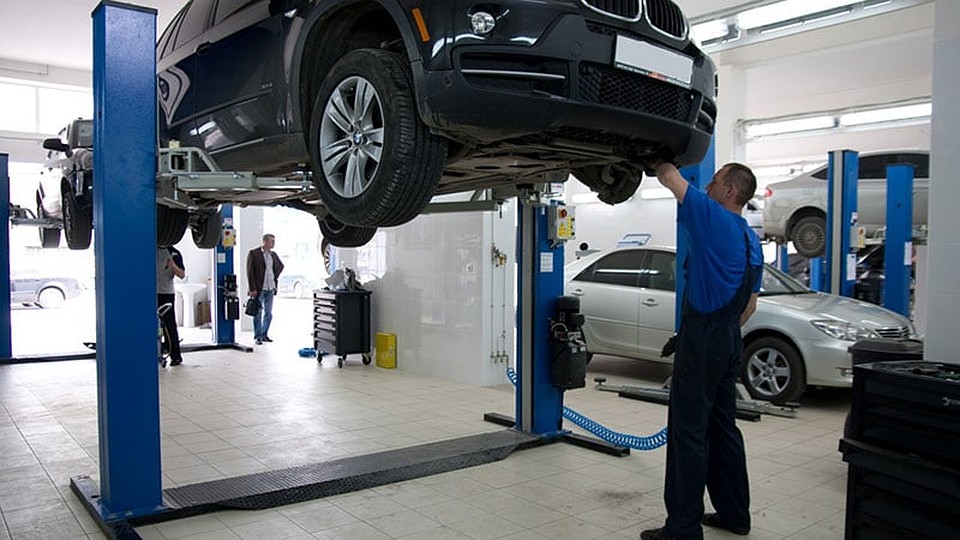
Фото: Центр кузовного ремонта Волга-Раст.
А теперь стоит поговорить о тех моментах, которые все же стоит учитывать при выборе сервиса. Это позволит избежать проблем в дальнейшем.
— Срок работы автосервиса. Под этим подразумевается общий срок работы организации, в крупных и давно известных сервисах заботятся о своей репутации.
— Наличие качественного оборудования. Многие неисправности требуют специализированного подхода к задаче. Например, удаление вмятин без покраски, невозможно произвести без приспособлений, обеспечивающих вакуумное крепление инструмента к детали.
— Стоимость. Пожалуй, это самый спорный вариант, именно по поводу нюансов этого выбора у автовладельцев имеются самые большие разногласия. Стоит помнить, что не нужно гнаться за низкой стоимостью, это может привести к плачевным результатам, обязательно учитывайте дополнительные факторы.
— Учтите, что ремонт кузова автомобиля достаточно сложный процесс, поэтому стоит его производить только в соответствии с рекомендациями производителя. Хорошо, если выбранный вами сервис проходил сертификацию у официального представителя. Это говорит о наличии всего необходимого оборудования, которое будет соответствовать стандартам.
Еще один момент, который нужно учитывать – правильность постановки задачи. Часто можно слышать жалобы на навязывание услуг, к примеру, приехал человек устранить царапины на кузове автомобиля, а ему еще и полировку кузова сделали. Как правило, такие люди делают ошибку при заказе услуги. Практически всегда на вопрос, что нужно сделать отвечают следующее: «Нужно убрать царапину, чтобы машина круто выглядела».
На основании Ваших слов мастер предлагает полировку, ведь убрать мелкое повреждение, это еще не значит, что авто будет хорошо выглядеть. Чтобы добиться такого эффекта, нужна полировка автомобиля. Отсюда и появляются разговоры о навязывании дополнительных услуг.
Всегда четко говорите, что вам требуется сделать. Если вы не слишком хорошо разбираетесь в вопросе авторемонта, можно проконсультироваться с более опытными автовладельцами. Такая подготовка позволит избежать недоразумений и непонимания.
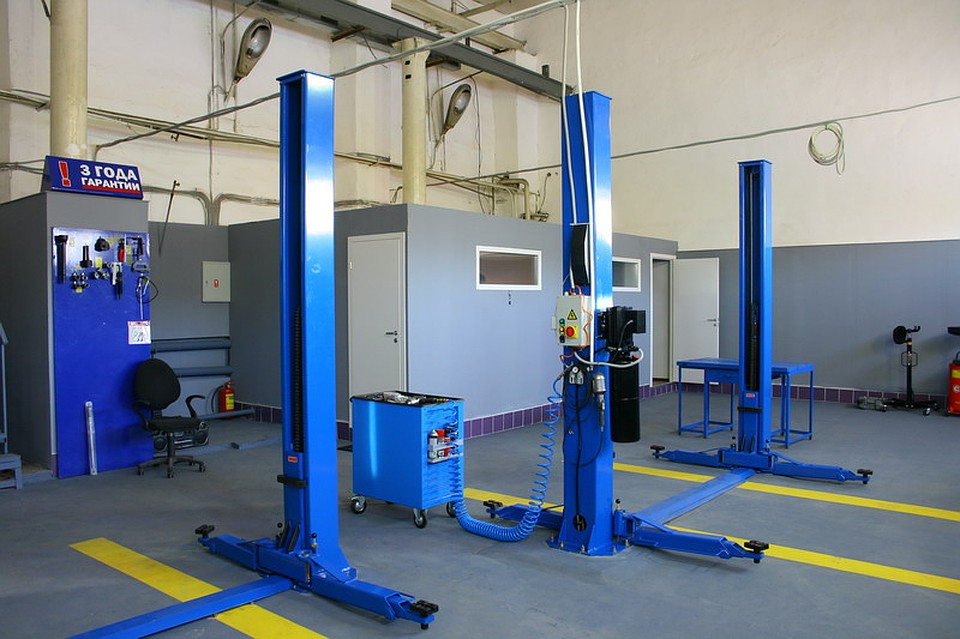
Фото: Центр кузовного ремонта Волга-Раст.
СЕРВИСЫ. ЧАСТНЫЕ ИЛИ ОФИЦИАЛЬНЫЕ
По традиции выделяют три группы сервисов:
— гаражные;
— частные;
— официальные.
Про гаражные ничего говорить не будем, качество их работы всем известно, а вот остальные рассмотрим более подробно.
Официальными сервисами называют организации, которые работают на базе дилеров. Они выполняют гарантийный ремонт, но могут качественно обслужить и другие марки автомобилей.
В официальных автосервисах основной упор делается на качество услуги. Отчасти это так, но опять же многое зависит от менеджера сервиса. Однозначно плюсом будет использование только оригинальных запчастей, это хоть и дороже, но проблем с машиной будет меньше.
Частные сервисы, как правило, отличаются меньшими ценами на работы. Также у водителей есть выбор, какие комплектующие ставить, в некоторых случаях выполненные по контракту запчасти не отличаются по качеству. Также в крупных ремонтных центрах регулярно выделяются деньги на обучение сотрудников, это положительно сказывается на качестве.
Однозначно сказать, в какой сервис лучше обратиться невозможно. В каждой конкретной ситуации ответ может различаться. Для выбора стоит смотреть на сервис, а также на особенности оказания им услуг.
КАК СДЕЛАТЬ ВЫБОР
А теперь, давайте посмотрим, как правильно выбрать сервис и не ошибиться при этом. Тут стоит учитывать несколько факторов:
— Наличие оборудования и сертификатов. Сейчас для многих моделей автомобилей требуется отдельный набор инструментов, поэтому лучше будет, если сервис приобретает только рекомендованное производителем оборудование. Это дает определенную гарантию, что ваше авто не сломают еще больше.
— Стоимость услуг. Например, цена на покраску авто в Волгограде может различаться в разных сервисах достаточно существенно, при этом не обязательно работу сделают дорого и качественно. Поэтому, цену при выборе учитывайте, как дополнительный фактор.
Иногда водители смотрят на удобство расположения, но это не важный фактор. Если, конечно, нет задачи ездить на ремонт каждый день. В остальном выбор лучше делать, опираясь на конкретные факты, а также советы знакомых.
На правах рекламы.
Инструменты для ремонта автомобиля: практические советы от профессионалов
Кузовной ремонт автомобиля – занятие, к которому приступают с наличием нужных навыков, инструментов и оборудования. Отдельные виды ремонта кузова выполняются самостоятельно в домашнем гараже – к ним относятся покраска, удаление коррозии, рихтование вмятин и другие процедуры. Серьезный ремонт автомобилей надо поручать профессионалам в этой области.
Кузовной ремонт[contents h3 h4]
Предварительно подготавливается помещение, в котором планируется проведение ремонтных работ: кузовной инструмент находится на рабочем месте, огнеопасные жидкости и материалы удаляются за пределы зоны ремонта, все лишние детали и предметы убираются.
Окрашивание автомобиля
Покраска авто – распространенная разновидность кузовного ремонта, которая под силу каждому автовладельцу. Чтобы результаты покраски радовали глаз как можно дольше, а само покрытие выполняло декоративную и защитную роль, надо грамотно подойти к процессу подготовки автомобиля к окрашиванию. В первую очередь подготавливаются материалы и набор инструментов для ремонта автомобиля, нужные для покраски поверхности. К ним относятся следующие:
- Шпатлевка, грунтовка и краска.
- Шлифовальная машинка и абразивные материалы.
- Пневматический распылитель краски.
- Маскировочная пленка и малярный скотч.
- Шпатель и малярный нож.
Указанные инструменты для машины должны быть в наличии в обязательном порядке.
Перечень можно расширить и воспользоваться дополнительным оборудованием и вспомогательными инструментами.
Подготовка машины к окрашиванию
Следующий этап покраски – подготовка кузова. Первоначально снимаются все наружные элементы, мешающие процедуре окрашивания. К ним относятся уплотнители, радиаторная решетка, молдинги, замки и другие детали. После «раздевания» авто надо тщательно вымыть и просушить, насухо вытерев тряпкой поверхность. Мойку проводится струей воды высокого давления в два этапа – первый смывает грязь, второй закрепляет первоначальный результат.
Подбор краски – важный этап. Лакокрасочные расходные материалы для кузовного ремонта должны гармонировать с общим цветом при окрашивании отдельных деталей. В противном случае, даже при различии в полтона, авто будет выглядеть нелепо. Выбору цвета уделяется внимание в профессиональных автосервисах – там подбор цвета осуществляется компьютерной программой, которая находит точное соответствие.
Когда расходные материалы для кузовного ремонта подобраны, приступают к подготовке поверхности перед покраской. На этом этапе все не окрашиваемые детали (стекла и другие) заклеиваются трафаретами или малярным скотчем. Далее покрытие кузова обезжиривается (используется любой растворитель) и насухо вытирается. После выполняется шлифовка поверхности. Очистка делится на типы:
Подготовка к окрашиванию- Тепловая. При помощи паяльной лампы старые слои краски выжигаются под воздействием температур. Использовать оборудование надо аккуратно – есть риск повредить конструкцию кузова.
- Механическая. Используется шлифовальная машинка, наждачная бумага с подобранной зернистостью и соблюдаемой разницей между номиналами, либо другой шлифовальный инструмент для кузовных работ (пескоструйный пистолет).
- Химическая. Наносимые на кузов растворители разъедают старое покрытие, в связи с чем оно легко удаляется щеткой. Надо позаботиться о защите кожных покровов и глаз.
Заключительные этапы подготовки кузова – шпатлевка и грунтовка. Первое действие подготавливает основу для грунтования – трещины, вмятины и другие дефекты выравниваются и становятся гладкими, подходящими для дальнейшей обработки. Далее наносится грунтовка, как правило в три слоя, временной промежуток между нанесением которых составляет от 10 минут. После высыхания слоев грунта можно начинать кузовной авторемонт – окрашивание кузова.
Инструменты для удаления коррозии
Качественный кузовной ремонт и покраска авто невозможны без предварительной антикоррозийной обработки кузова. Для удаления ржавчины необходимы специальные инструменты для кузовного ремонта автомобилей, а также проведение таких операций, как:
- Тщательная мойка авто под сильным напором и с использованием шампуня.
- Просушка кузова путем вытирания сухой тряпкой.
- Обработка пораженных коррозией мест поверхности крупной наждачкой.
Главный инструмент для кузовного ремонта по удалению ржавчины механическим методом – шлифовальная машинка с набором абразивных дисков. При помощи устройства ржавое место зачищается на глубину до одного сантиметра, после чего обрабатывается мелкозернистой наждачной бумагой. Для эффективности можно использовать растворитель.
Шлифовальная машинкаИнструменты для кузовного ремонта не ограничиваются шлифмашинкой. Химические средства не уступают механическим приспособлениям по эффективности. Помогут такие вещества:
- Ортофосфорная кислота. Содержится во многих «преобразователях ржавчины», но отличается меньшей ценой и повышенной эффективностью, особенно в концентрированном виде.
- Цинковый спрей. Это вещество, будучи распыленным на пораженное ржавчиной место на покрытии кузова, формирует защитную пленку, предотвращая распространение коррозии.
- Нейтрализатор ржавчины. Состав наносится на ржавчину, которая под воздействием активных компонентов трансформируется в мягкое вещество. В последствии оно легко убирается тряпкой или щеткой.
Своевременное уничтожение ржавчины продлит срок службы кузова машины и даст сохранить привлекательный облик автомобиля даже по прошествии десятков лет.
Инструмент для удаления кузовных вмятин
В специализированных магазинах можно найти все для кузовного ремонта, в том числе инструменты для ремонта автомобиля по устранению вмятин. Механические повреждения кузова портят внешний вид машины и ухудшают эксплуатационные характеристики авто. По этой причине удаление вмятин без покраски надо проводить сразу после их появления.
Нужные инструменты для ремонта авто и удаления вмятин представляют собой набор рычагов, которые отличаются друг от друга по длине, форме и размерам. Сюда входят отбойники, вытяжки на вакуумной тяге, молодки для устранения выпуклостей и насадки, подходящие для вмятин с определенными параметрами.
ПОСМОТРЕТЬ ВИДЕОИНСТРУКЦИЮ
Используя эти инструменты для ремонта кузова автомобиля, можно изменять форму вмятин на кузове и устранять их, закрепляя результат минилифтером, обратным молотком, пистонами и клеевым пистолетом. При наличии навыков может быть устранена любая вмятина!